Custom injection molder Plastikos Inc. is in the midst of a 17,000-square-foot expansion that will add 30 percent production capacity at its Erie, Pa., headquarters plant.
The bricks-and-mortar expansion should be complete by late April or May, officials said during PMM's site visit in February. Winter weather at the time was causing a slight delay. Erie's northern neighbor is the Great Lake of the same name, which completely froze over for the fourth time in 40 years. But there was no deep freeze at Plastikos, where management always is energetically making plans and pursuing its strategy.
With this project in particular, the company is honing its ability to handle shorter runs and perform higher-volume work with a focus on productivity and efficiency, said Philip Katen, Plastikos' president and general manager. In dollar terms, this expansion is the largest in the company's history. Plastikos just celebrated its 26th birthday.
"It's a culmination of our strategy and a long journey to expand and grow," he says. In the medical market, that growth has been significant, he says. Seven years ago, the company had little to no sales into medical; now, annual sales from that sector are $5 million and still growing. Molded products are used in fluid delivery systems, pumps and pump systems, eye care, diabetes care, and medication delivery, to name a few.
Building on Tradition of Innovation
"Made in the USA" is a mantra for Plastikos and for mold-making sister company Micro Mold Co. Inc., located less than 10 miles away.
Tim Katen and David Mead started Micro Mold in 1978; in 1989 they started Plastikos with Gary McConnell, a junior partner. Plastikos has been innovative in many areas. For example, rather than rely on beside-the-press cameras, Plastikos is using custom-designed thermal imaging technology to detect problems in the mold with software that interfaces with the presses.
The company employs an in-house welder, Dena Spacht, who can weld down to 0.003 of an inch. That is essentially the diameter of a strand of human hair. Plastikos used to outsource welding but decided to bring it in-house to be able to do repairs on site. This allows it to get a mold back into production in hours rather than days, and keep tools up and running at full cavitation.
Sixteen all-electric Arburg presses occupy the main production area within Plastikos' building and four three-axis robots help perform the work. That will grow to six three-axis robots over the next few months as well as three additional new Arburg machines in Plastikos' medical expansion. Automation is a focus as the company moves forward. Robert Cooney, manufacturing manager at Plastikos, said they are developing automation on one press to perform overmolding work. That will include the addition of more robust end-of-arm tooling (EOAT) and the corresponding robot with a higher payload capacity to support that. Think of 33 pounds of payload capacity versus about 13 pounds of payload capacity, which is what it will replace. Because the project will be higher volume, an Arburg Multilift Select robot will orient the parts to be overmolded and load them into the mold. Once the overmolded cycle is completed, the EOAT also will assist in removing the TPU part from the cavity before loading the next set of ABS parts. The part being molded is for an external feeding tube system that allows a doctor or nurse to change feeding lines while the patient remains connected to the feeding system.
From three of those presses, products are shuttled into a clean room via a window, which isn't the ideal setup, said Ryan Katen, general manager of Micro Mold. The biggest limitation is the inability to install a three-axis robot above the press and use EOAT during the molding process to remove parts that require special handling.
"Also, we are somewhat limited to the types of parts that can successfully pass through our conveyor and [air-conveying] system," he said. That will be addressed with the expansion, which will operate as a wholly enclosed Class 10,000 ISO 7 clean room environment.
The new manufacturing space will have a mold transition room, and a human transition room where workers will suit up for clean room work — donning hair nets, shoe and clothing covers. The area will begin with three presses — one 220-ton and two 88-ton Arburgs — with the plan to install a total of eight.
Design-Build-Run for Competitive Advantage
No one at Plastikos is focused on saving a few bucks on the cost of a new mold. Quality comes before cost, always. Micro Mold supplies Plastikos in a relationship based on design-build-run production management.
"We have seen firsthand the poor design, poor quality and shortcuts that other mold fabrication/tool shops take in order to save a couple of bucks on the cost of a new mold," says Philip Katen. "And we feel the pain of trying to run and maintain those sub-par molds over the months and ultimately years that our customers expect the mold to run production to support their products."
Currently, 80 percent of the new molds and tooling projects completed at Micro Mold are to support production at Plastikos.
"Our strategic focus is to increase that percentage to 90 percent or more since those full-service design-build-run projects are the most profitable over the lifetime of the project and they reinforce the long-term strategic relationships that we forge with our customers," says Philip Katen.
Here, all mold bases are built in-house, says Ryan Katen. "We can design our mold base around our part, which is a big advantage," he says, especially in terms of cooling channels.
A five-axis machining center — GF AgieCharmilles Form 200 Sp — is complemented with a robot that allows it to run 24/7.
"It can cut and burn all night long," he says.
Micro Mold is continuing to update its technology. In its wire EDM room, an EDM DrillMate 430i produces high-speed, precision holes. In a dedicated R&D room, three injection presses handle all of the initial tool samples.
Back in the Plastikos facility is Old No. 1, the original Van Dorn 55-ton injection molding machine that started Plastikos. Ryan Katen managed to track it down from another nearby company that had purchased it. It is displayed with a plaque of its history and a reminder that it was replaced as part of the company's strategy to continually invest in new technology.
Angie DeRosa, managing editor
Contact:
Plastikos Inc.,
814-868-1656, www.plastikoserie.com
Micro Mold Co. Inc.,
814-838-3404, www.micromolderie.com
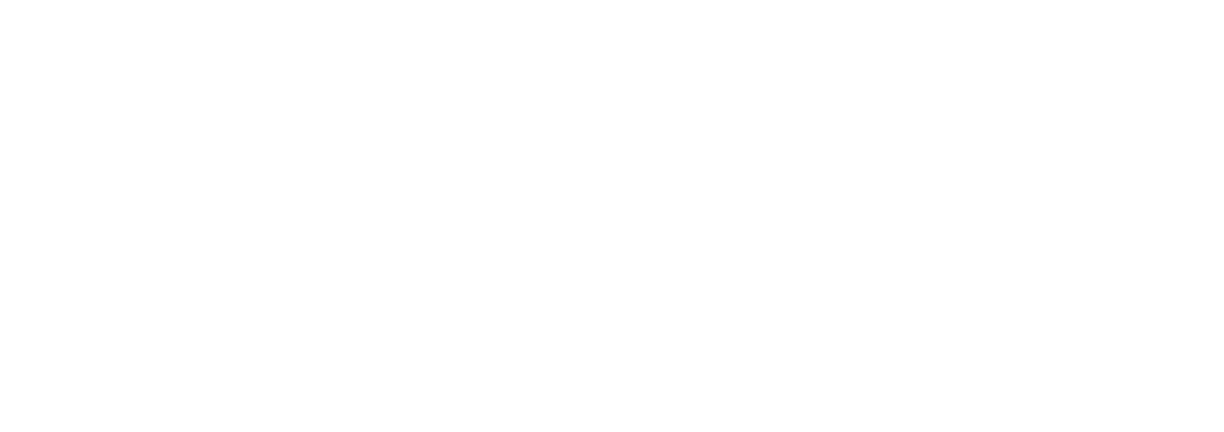