New extrusion processor turns to KraussMaffei, Inoex to meet tight tolerances
Have you found an innovative equipment solution to a plastics processing challenge? Let us know.
Problem: A company that had no experience with plastic extrusion needed user-friendly equipment that made maintaining strict tolerances easy.
Solution: Extruder maker KraussMaffei and extrusion technologies specialist Inoex provided equipment and the support processor Worthington needed to start making hybrid plastic and steel water-storage vessels.
By Karen Hanna
Hand-holding and professional expertise — along with machinery and equipment — were key selling points for a company making its first foray into extrusion.
When Columbus, Ohio-based steel-products maker Worthington Industries first began investigating how to make plastic water tanks at its Amtrol Inc. subsidiary, it had some experience with injection molding and blow molding. Amtrol, however, had none, putting it far behind the customers KraussMaffei salesman Artie Riegger typically sees.
“Most of these people that come into new companies and maybe new products, they have experience in the extrusion process, as opposed to this customer that had absolutely no knowledge of extrusion or plastics. Zippo,” said Riegger, sales manager for the Northeastern U.S. “So that that made it a very interesting challenge because they came up with this idea, and they wanted to see if it would work. And lo and behold, it does.”
Amtrol joined Worthington's portfolio in mid-2017. It was a good fit for the pair of former competitors — the West Warwick, R.I., plant made steel vessels for storing water.
But customers had started to express interest in vessels that were lighter, made up of a mix of steel and plastic. An idea was born: Extrude plastic pipes, cut them into segments and cover each end with steel domes.
Alex Spires, a senior project engineer for Worthington, conceded his company was starting from scratch.
“We’re like, ‘We don’t know much about extruding. We don’t know much about the dies or an
y of it,’ so we wanted to find one person that essentially we can have on the hook for making the whole system operate. And then all the vendors we talked to were like, ‘Well, that’s not typically what we do,’ ” he said.
But, whether working with metal or moving into plastic, the company had expertise it could leverage, Spires said.
“A large project, whether the product’s steel or plastic, you have the same hurdles and obstacles,” he said.
With operations around the world, including composite vessel plants in Europe, Worthington has some experience processing PP — the material it decided to use for the water vessels.
But, with no extruders and no extrusion experience, Worthington reached out to the experts — fellow manufacturers — for help. One extrusion processor stepped up to the plate, welcoming Worthington officials to a site visit and recommending Inoex, which in turn recommended KraussMaffei.
Adam Grier, president of Inoex, summed up his view of Worthington’s needs going into the project: “You’ve got to have your OEM partners that work well together. You’re going to need support at a level that most people can’t even imagine.”
While other extrusion processors might make pipes with wall thicknesses of 3 or 4 inches, Worthington envisioned products as big as 26 inches around, with wall thicknesses of just 0.125 inch. Plastics extrusion also requires greater temperature control than the steel products Worthington has grown accustomed to making, Spires said.
Following extrusion, the plastic tube would be wrapped in epoxy and fiberglass, giving it the strength it would need for water storage.
“The challenge became that, ‘Yes, we can provide a pipe line,’ but for the thin-gauge wall they were talking about, this was not going to be easy because it wasn’t another cookie cutter [project],” Riegger said.
The specifications Worthington required exceed the tolerances of many experienced extrusion processors, Grier observed.
“It is a pretty unique thing … because it wasn’t just that they came to us and said, ‘We’ve never extruded pipe. We want to extrude pipe. … And by the way, we want to extrude a fairly difficult pipe.’ On its face, I think this had like a 30 percent chance of success,” Grier said.
To meet the challenge, Inoex and KraussMaffei worked together to design a line featuring Inoex’s gravimetric feeding system and Aurex ultrasonic technology, along with a die, vacuum tank and chipless cutter from KraussMaffei.
The Inoex setup ensures wall-thickness accuracy of the entire pipe, Riegger said.
But the haul-off system KraussMaffei originally envisioned required rework, he said.
“We originally quoted the haul-off to be the same size as the rest of the downstream [equipment], and we quickly realized we had to go to a larger haul-off because the smaller [one] — the one that was close in size to a traditional pipe for that diameter — it could possibly crush the pipe because it’s a thin wall,” Riegger said.
To accommodate the extrusion line, Worthington renovated its Amtrol plant.
“We’ve carved off the end of our plant and put up new walls, put in a new HVAC system to maintain humidity and temperatures, so we’d have a little more control,” Spires said. “So, overall, it’s a lot different looking. You walk through the rest of our plant, and you’ll see some 30-year-old steel presses, and then you get back to the composite area, it’s all brand-new.”
But in the midst of all the preparations, the project hit a snag; just as the end seemed in sight, the COVID-19 pandemic shut down travel.
“We couldn’t bring the people over that were supposed to install it, so we were uncrating equipment that would have German Post-it Notes on it because the guy who wrote the note thought he was going to uncrate it, like, next week — and then we did it six months later,” Spires said.
Having overcome all the challenges — including the unexpected delays imposed by the pandemic — Worthington last year became a plastic extrusion processor. Out of a workforce of several hundred people at the Amtrol plant, about 20 people work in the new extrusion section, Spires said.
With KraussMaffei’s C6 controls, set up by the company to Worthingon’s specifications, operators have all necessary information at their fingertips. Based on the amount of material sent through the extruder and the measurements of pipe walls, Inoex’s technologies can make real-time adjustments anywhere along the system as needed.
For Grier, the project’s success is a testament to the professionalism and expertise of everyone involved —including Worthington personnel who showed an openness to learn. He praised all the partners in the project for coming together on a project he considers a professional highlight.
“These folks just continued to push forward and solve the problems systematically,” he said. “That’s what it takes to win in the extrusion business, is really a systematic problem solving. And the faster you can do those iterations, the faster you’ll pull ahead and get the things solved. But I see too many times: There’s six different possibilities, and people want to think they’re going to solve it faster, fire all six bullets at once, and then you know nothing. There was no controlled variable, and so you’ve accomplished nothing; you just made up a chaotic mess.”
And Worthington continues to push forward — according to Spires, pipes for water vessels might not be the only products the company eventually extrudes.
Its new KraussMaffei extruder, it turns out, can produce plastic pipe at a much faster clip than the equipment Worthington uses to produce the vessels’ other components.
For a company that’s taking on plastic extrusion, in addition to exercising its steel-product expertise, further diversification might not be out of the question.
“A lot of people had plastic expertise that they might not have been using so much in the current role at Worthington. Whether it’s plastic, metal, I mean, certainly there’s differences, but, at the end, it’s a lot of engineering. ... I guess the process for solving the problem doesn’t change any,” Spires said.
Karen Hanna, senior staff reporter
Contact:
Inoex LLC, Lancaster, Pa., 717-672-0870, www.inoex.com
KraussMaffei Corp., Florence, Ky., 859-283-0200, www.kraussmaffei.com
Karen Hanna | Senior Staff Reporter
Senior Staff Reporter Karen Hanna covers injection molding, molds and tooling, processors, workforce and other topics, and writes features including In Other Words and Problem Solved for Plastics Machinery & Manufacturing, Plastics Recycling and The Journal of Blow Molding. She has more than 15 years of experience in daily and magazine journalism.
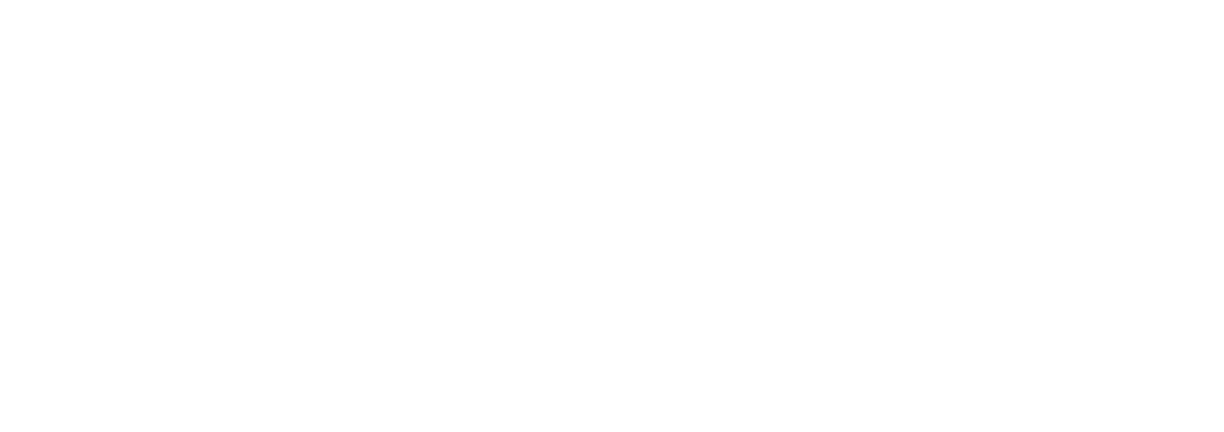