Conair helps tame challenging material
Problem: The tackiness of a new urethane material, plus the need for sterility, presented challenges for cooling medical tubing.
Solution: A water-quenching unit from Conair kept the task clean.
By Karen Hanna
The parts and tooling components that Teel Plastics manufactures to serve customers in the medical industry can have tolerances much smaller than the head of a pin. Development cycles — including work to customize quality-control and measurement devices — can take years.
“We’re able to leverage and bring a higher level of intelligence to their product with our processing equipment that we have at Teel,” said Steve Schick, the CTO for the company, which has four production plants in Baraboo, Wis.
In a multiyear quest to design and manufacture new tubing for a blood-separation device, technologies for building and measuring extrusion tooling, cooling profiles off the line and checking miserly tolerances all recently played a role.
It can extrude profiles with outer diameters ranging from 10 inches all the way down to 0.025 inch.
In all, the new tubing has about 24 important dimensions, with specs for attributes such as roundness and wall thickness.
Schick and his team emphasized that the goal isn’t just to fall within a tolerance range, it’s to narrow that range as much as possible, so that every dimension is on-spec repeatably.
“It isn’t just that you meet what’s in spec; it’s that you use enough less than the entire spec, you’d expect that you have an extremely low defect rate per million opportunities in any of these dimensions,” said Christian Herrild, director of growth strategies. “You don’t get to use the whole tolerance.”
For Teel and its medical customer, meeting the challenge started with tooling design.
Robert Kirkliauskas, the engineer who was involved in developing the tooling, said Teel used a Haas CNC lathe and mill combination equipment with high-speed heads, as well as special cutters, to manufacture an intricate pin and die set.
The pin isn’t in the shape of the circular holes in the tubing. It’s a modified polygon with holes on the inside to model the shapes of the holes in the tubing.
“The design takes into account the speed at which the plastic moves into the pin and then swells (or bulges) out as it exits,” a case study about the project states.
To prepare for production, Teel added a 2,500-square-foot Class 8 clean room to its 140,000-sqare-foot headquarters, to go along with one clean line already in operation.
“It required us to relocate some lines out of our current facility into one of our other facilities in town to free up the space,” said Bruce Martin-Wright, director of new product and process development.
That big change was just one of the challenges the tubing presented.
Many of the other challenges involved going small.
“Tooling has to be built within a half a 1,000th of an inch, which is smaller than a sheet of paper,” Kirkliauskas said.
Dealing with the part’s tricky material — a new thermoplastic urethane — brought issues of its own.
According to the case study, the tooling Teel made creates just enough draw to move the plastic through the die while avoiding the use of forced air and excessive stretching.
“If Teel would have used a more standard drawdown ratio, the process would have required much more manual adjustment,” the case study states.
“As far as difficulty, from a process standpoint, it was tackiness also on the surface of this particular material. Because, depending on how you stretch it and how you shape it, before it gets solidified, and how fast it gets solidified, that it gets too tacky ... all the parts get clumped up in one piece,” Kirkliauskas said.
The material’s stickiness when warm also drove decisions further down the line.
Because of that, cooling the tubing as it exited the extruder has to be a strictly non-contact operation, said Kirkliauskas, who compared the warm urethane to a glue stick.
A Conair MedLine water-quenching line was an obvious choice, according to Martin-Wright.
“Their water-management system is really at the forefront of the industry, and allows us to maintain the precise tolerances that we have to with this product,” Martin-Wright said.
Ernie Preiato, VP of extrusion sales at Conair Group, said the company’s MedLine equipment is specifically designed and configured to meet the demanding requirements of medical applications.
In the case of urethane, water is a good choice.
“Urethane is a soft, tacky material that can be challenging when it comes to vacuum sizing. Our MedVac series tanks use non-contact sizing to apply a thin layer of water around the tube as it enters the vacuum tank. Sizing uses digitally controlled vacuum and water/air separation for optimum stability. This is the best approach. … ,” Preiato said.
“I think the things that make it appropriate for our systems is the control systems they put into the vacuum and also the water levels for fill rate, as well as for the cooling rate. And, also, the size of the equipment fits our process window for running medical-type applications,” Schick said.
The urethane isn’t the only difficult material with which Teel works — in an average year, it processes more than 50 thermoplastics, from HDPE and PP to TPU and flex PVC to fluorinated ethylene propylene to polyetherether ketone.
Making sure the tubing comes out right was another challenge, calling for several custom solutions, the Teel team said.
“I would say I think our biggest challenge is probably identifying the right optical equipment to measure all 24 dimensions,” Schick said.
Making things a bit easier is Teel’s identification of what it calls the tubing’s“We’re monitoring that power dimension using a Zumbach laser gauge, which gives us continuous feedback while we’re running, and then we take samples periodically and then use a Keyence vision system to measure and interrelate all of those 24 dimensions,” he said.
The company also worked with Keyence to develop nonstandard methods for using measurement devices to ensure the quality of the tubing, Schick said.
In addition, a team at Teel designed and assembled a custom quality-control device that can measure the tubing without exerting pressure on it or bending it.
Both Schick, at Teel, and Preiato, at Conair, emphasized the importance of vendors’ relationships with processors when they take on tough projects.
“Conair is all about relationships with our medical customers,” Preiato said. “This is what separates us from our competition. Customers like Teel often come into Conair for their extrusion trials and to work with Conair engineers to establish the best solution.”
Schick praised the companies that provide support for Teel.
“We do a lot of work, but we also highly leverage our supply base,” he said.
Schick said he’s humbled by the company’s mission of “making products that matter and make lives better,” and he’ll have more opportunities to do so in the years that come, as Teel’s expansion of its clean room shows where business is headed.
While it serves other markets, including making cosmetics packaging and pipes for water treatment, Teel is preparing for a future where the medical sector plays an even larger role.
“We see a lot of growth coming in medical. We already are putting together plans for — again — doubling the clean-room space that we have available, potentially as early as next year,” Herrild said.
Schick is looking forward to it.
“That’s what we all like to see, that things that we’re manufacturing with our team of people at Teel is that they do have an impact on people’s lives in all the markets that we serve,” he said. “It’s humbling to know that the work that you do is helping somebody else live a better life.”
Karen Hanna, senior staff reporter
Contact:
Conair North America, Cranberry Township, Pa., 724-584-5500, www.conairgroup.com
Karen Hanna | Senior Staff Reporter
Senior Staff Reporter Karen Hanna covers injection molding, molds and tooling, processors, workforce and other topics, and writes features including In Other Words and Problem Solved for Plastics Machinery & Manufacturing, Plastics Recycling and The Journal of Blow Molding. She has more than 15 years of experience in daily and magazine journalism.
Request More Information
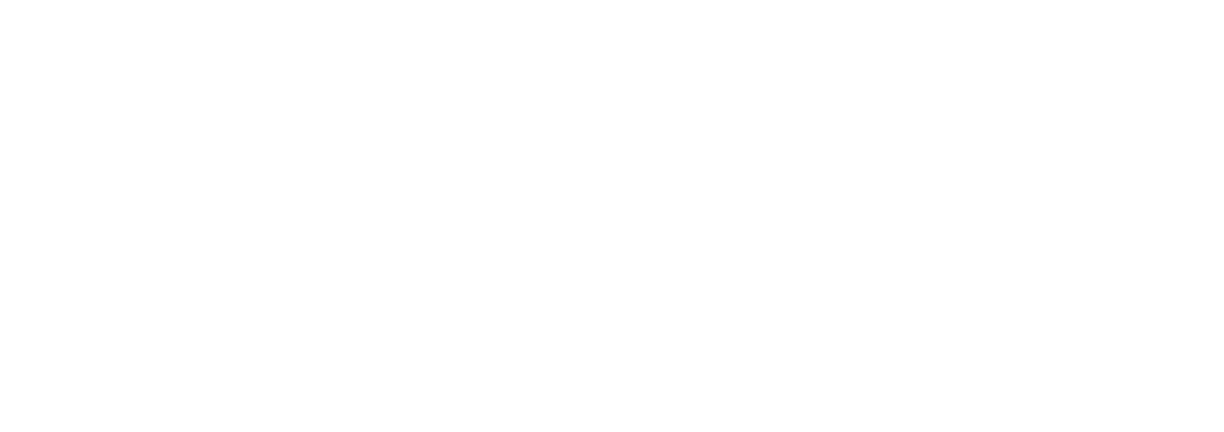