WARP The Inoex WARP family of products uses radar technology to provide precise contactless measurement of pipe diameter and wall thickness as pipe is being extruded. The WARP 8 has eight measuring points and comes in five sizes that can measure pipe diameters from 60mm to 1,200mm, and wall thicknesses from 5mm to 250mm, depending on the material. The WARP 100 has 38 measuring points for pipe with high quality demands, such as pressure or gas pipes. It comes in three sizes, measuring diameters from 90mm to 630mm, and wall thicknesses from 5mm to 125mm. The WARP XXL has eight to 32 measuring points, for measuring diameters from 630mm to 3,500mm, and wall thicknesses from 5mm to 250mm.
What’s new? An updated design. All WARP models now have a smaller footprint, which offers more flexibility for placement on an extrusion line. The design also allows for easier access for maintenance during production and remote commissioning.
Benefits Maximized productivity and quick return on investment. The WARP collects process data, allowing an extrusion line to operate with closed-loop control, and stores that data for future reference. It has a user-friendly interface and is Industry 4.0-ready. Information can be tailored to the needs of the user — for example, line operators might see information to help them optimize production, while quality-control personnel might see higher-level production data. This level of data transparency helps optimize processes to yield more feet of pipe per pound of resin, cuts time required to bring the production process into specification and improves quality control while reducing manufacturing costs. Inoex says these systems typically have a payback of less than 12 months.
Inoex LLC, Lancaster, Pa., 717-672-0870, www.inoex.com
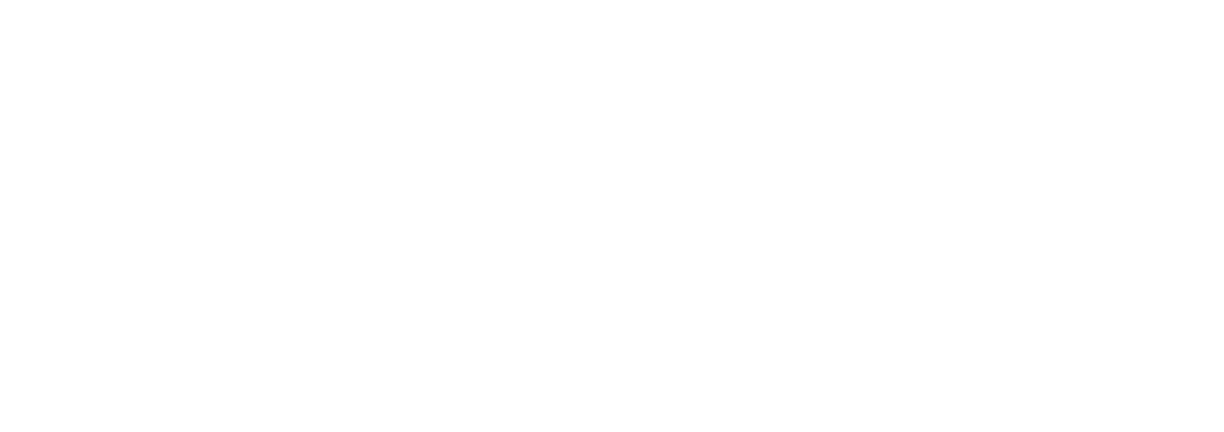