Battenfeld-Cincinnati rolls out new controller for small extruders
Battenfeld-Cincinnati has launched a new controller for its smaller extruders, including its uniEX single-screw extruders, as well as a new series known as Alpha Plus.
Over the past 18 years, the company has sold more than 1,200 Alpha single-screw extruders for producing small technical profiles and pipe. The Alpha extruders come with relay controls, and they’re now known as Alpha Basic extruders when ordered with them. Alpha Plus models are distinguished from the Alpha Basics in that they come with the new control system, the BCtouch UX compact.
Based on the company’s existing BCtouch UX controller, which is standard on Battenfeld-Cincinnati’s other extruder lines, the BCtouch UX compact is designed for smaller-scale lines. It is a digital controller that is simple and intuitive to operate and has optimized software, the company said. Battenfeld-Cincinnati calls the new control unit the “little sister” to the BCtouch UX, which features a 21.5-inch screen.
The BCtouch UX compact comes with a 12-inch screen that provides operators with an overview of how the extruder is performing. The controller can monitor and report on the status of components like the motor, drive, gearbox and heaters.
A high-performance temperature-monitoring module is integrated into the control system, which is critical for processing temperature-sensitive raw materials, the company said.
All Alpha extruders feature a plug-and-play design that allows for simple and quick setup. They are compact, which makes them well-suited for use in production facilities with limited space, the company said, and are available with screw diameters of 45mm, 60mm and 75mm.
The Alpha Basic and Alpha Plus extruders can be used to make profiles, small pipes, hoses, medical tubes and seals.
Battenfeld-Cincinnati also has updated its DTA 160 direct cutting machine, making available an all-electric version.
Designed to cut both polyolefin and PVC pipes to customers’ specifications, the DTA 160 now operates entirely without hydraulics, which reduces the weight of the saw carriage by about 60 percent as compared to conventional systems. The reduced weight allows the saw carriage to move more quickly and allows short pipe lengths to be cut at faster speeds.
“What’s new with this cutting unit is we don’t use a hydraulic system anymore,” process engineer Brigitte Diekhaus said. “A hydraulic system means you have an oil change; you have an oil system, which is very heavy. With this new construction, you can build it very compact.”
In addition, the all-electric operation results in easier maintenance, the company said.
Bruce Geiselman, senior reporter
Battenfeld-Cincinnati USA, McPherson, Kan., 620-241-6843, www.battenfeld-cincinnati.com
Bruce Geiselman
Senior Staff Reporter Bruce Geiselman covers extrusion, blow molding, additive manufacturing, automation and end markets including automotive and packaging. He also writes features, including In Other Words and Problem Solved, for Plastics Machinery & Manufacturing, Plastics Recycling and The Journal of Blow Molding. He has extensive experience in daily and magazine journalism.
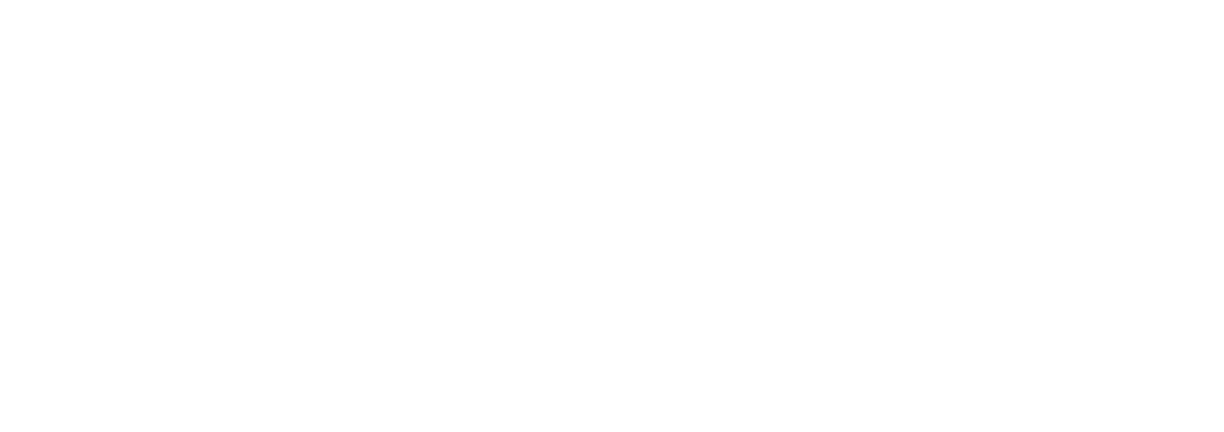