Extruder technology will evolve over the next decade, and by 2030, OEMs foresee better control units, greater adoption of Industry 4.0 technology and more automation. Extruders increasingly will be connected to auxiliary equipment, and manufacturers will improve energy efficiency, several OEMs said.
Coperion: More growth, more technology
Coperion’s Markus Schmudde, head of R&D, predicts continued strong demand for extruders in 2030.
“I think the market will be quite good because we’re still experiencing growth in the plastics market overall,” Schmudde said. “I think extrusion technology will still be a leading technology in producing plastics in general.”
Schmudde said the basic mechanical systems will not change much, but control units likely will improve as processors embrace Industry 4.0, and they may adopt more automation to reduce labor costs.
“The plastics industry, at least in our part of the business for compounding machines and extrusion machines, is quite conservative,” Schmudde said. “For example, injection molding machines are already ahead of us — ahead of the compounding industry — in terms of digitalization, Industry 4.0, IoT, or whatever you call it. Connected machines and data analytics will come also in the compounding/extrusion business, I believe.”
By connecting devices and monitoring their performance more closely, processors will become more efficient because they will have more access to data analytics, he said.
Industry 4.0 analytics could help extruder operators keep track of failures and allow them to better focus on maintenance and other factors that can prevent unexpected downtime.
“The handling of the machine will become easier,” he said. “Insight into the process will get better and deeper. Therefore, I believe efficiency in the production will increase.”
Industry 4.0 analytics also could improve product quality and reduce the need for some of the quality control analysis now taking place in laboratories.
“A lot of quality analysis [currently] is done in a quality lab, and if we think about Industry 4.0 and online quality measurements, I think this will replace somewhat the QC lab,” Schmudde said. “If more and more machines have sensors built inside the machine that can measure quality or predict the quality from certain signals or data that comes out of the process, then I think less quality testing afterward is needed.”
Adoption of Industry 4.0 standards also may promote greater integration of auxiliary equipment into the primary machine.
“It’s important to monitor also the auxiliary equipment to increase the efficiency because the auxiliary equipment is supporting the primary processing machinery,” Schmudde said. “Therefore, it’s also critical for the efficiency of the whole process.”
It is likely that the main control unit for the extruder increasingly will control and display data from auxiliary equipment, such as dryers and feeders.
“I think we will in the future see that all these systems are combined more and more, and the data is getting more transparent and the producers are getting more insight into the auxiliary equipment as well,” Schmudde said. “Or, maybe the auxiliary equipment is not even displayed on the control system in 10 years because it’s also all controlled automatically by the main control system, so the operators don’t have to take care of the auxiliary equipment anymore.”
Coperion is working on a solution to a possible future problem: that Industry 4.0 technology monitoring could gather so much information that it overwhelms the operator.
“The key is to connect everything in one control system and show the user exactly the data he needs to know,” Schmudde said. “We showed a new HMI at the K Show 2019 where we try to do exactly that because I believe in the future, the danger of monitoring all the data and connecting all the equipment is that you overload the operator with data he doesn’t need or he cannot understand.”
Different information might be provided to the operator than to maintenance workers and production managers. The goal is to provide each person with exactly the data he or she needs.
“This is a challenge I think we will have to deal with in the next 10 years because more and more data will be available,” Schmudde said.
Machine manufacturers will need to optimize their control systems so they can be used by operators without a doctorate in electronics, Schmudde said.
Schmudde also is interested in whether processors will want to put their data into a cloud system instead of relying on local data storage, or if security concerns will preclude that.
“That, at the moment, is a very interesting development that we are trying to follow and observe because it is very critical when we think about developing our control systems or software we provide our customers,” Schmudde said.
Coperion also is seeing a greater interest among its customers in energy-efficient equipment.
“Energy efficiency is coming more and more into the discussion,” Schmudde said. “It’s been there for some years already, but I think we have to focus on that even more in the future. It’s an issue worldwide. In more and more countries, the regulations are getting tighter. Our customers, the production companies, are forced to save energy. An extruder or a compounding machine is one of the biggest consumers in a compounding facility.”
In some countries, governments are setting up programs to reward companies for energy savings, he said.
Robotics also may play a larger role.
“I can imagine in 2030 that automation in terms of robotics will start to come into the production so that the operators don’t have to do so many things manually during a product change,” Schmudde said.
He envisions robots being used for some maintenance tasks and for changing die plates. He also sees them lifting heavy parts.
In addition, Schmudde anticipates that an increasing number of processors will use automated guided vehicles for moving pallets, large bags of resin and other items throughout a factory.
US Extruders: Evolutionary, not revolutionary
Changes to extruder mechanics will take place slowly, said Bill Kramer, president of US Extruders.
“I don’t see a lot of revolutionary changes,” Kramer said. “It’ll probably be a continuing of the evolutionary kind of changes.”
The biggest change may be the adoption of direct-drive motors, which were introduced several years ago and praised for their energy efficiency and reduced maintenance requirements.
“They were touted quite a few years ago when the first extruders appeared with no gearbox,” Kramer said. “However, the cost has not fallen enough, and we haven’t really seen a big conversion, but I would expect that the motor costs will eventually come down enough so we will see more of that. It’s a machine that has no gearboxes, just a motor direct drive to the screw, and it requires a high-torque, low-speed motor. It’s a modern permanent-magnet motor.”
However, Kramer expects their adoption to be a slow process. The technology is more popular in certain segments, such as in the medical field, where eliminating a gearbox and the oil inside it has advantages. In addition, some processors are investing in direct-drive machines because they require less space.
One reason Kramer is hopeful about a reduction in direct-drive motor costs is a burgeoning interest in electric vehicles.
“The technologies are the same that are involved in the electric motors for cars and trucks,” Kramer said. As more direct-drive motors are produced, the costs should drop, he said.
Kramer also foresees improvements to control systems.
“I think control systems will continue to be more simple, more accessible,” he said. “The control systems on a plastic machine are based on and mirror what we see in our desktops and in our phones and all the other areas where we use computers. There’s just a general trend to make them more operator-friendly as time goes on, more intuitive.”
Kramer predicts a greater interest in Industry 4.0 and the ability to link all equipment on a production floor. He envisions production data from each extrusion line being fed to a production manager’s computer system, allowing for more efficient scheduling of new orders.
“Product runs would be communicated electronically directly to the operator through a control unit rather than sending down some sort of a paper order,” Kramer said.
The key to making this happen will be allowing different pieces of equipment and computer systems to better communicate with each other without the help of in-house IT employees, Kramer said.
“And it may take some time for that to improve just because of a lack of [communications] standards,” Kramer said. “There are a lot of different types of systems. It’s kind of a slow evolution of that occurring.”
Once all equipment is connected through Internet 4.0, a production manager would be able to not only send a production order to an extrusion line, but also could ensure the proper resins and other materials are delivered, the proper tooling is in place and the proper recipe is fed into the control unit.
SML: Rosy picture for film and sheet
The future is bright for the makers of extrusion equipment and the processors who use it, although some segments may fare better than others, said Mark Jones, North American director of support services for Austria-based SML.
“If you’re looking at durable goods, then I think there is no alternative to plastics, and so I think the future for that is rosy,” Jones said. “If you’re looking at single-use plastics, I think it’s much more of a mixed bag.”
Jones predicts continued demand for products like stretch wrap and basic food packaging.
“I think it is here to stay and will continue to grow,” Jones said.
Another growth area is post-consumer and post-industrial plastic in packaging products.
“You’re seeing increasing numbers of machines installed in plants with adaptations to allow direct use of post-consumer [resin] in packaging,” Jones said. “The machines change slightly to allow you to do that, but not a great deal.”
But Jones sees market contraction for extruders designed to process bioplastics.
“I think there was a lot of optimism that that might be a new market, but from what I’ve seen it tends to be fading,” Jones said. “Partly, I think it’s because biopolymers are competing against crops for food, so that has a negative social connotation.”
In addition, bioplastics tend to be more expensive than traditional polymers.
“I think that there doesn’t seem to be a lot of pressure to run those,” Jones said.
Jones expects extrusion lines to do a better job of regulating themselves, requiring less operator involvement.
“I think you’re seeing a general de-skilling of the workforce,” Jones said. “As a result, there is more demand for machines to be able to automatically adjust themselves for things like controlling film thickness and monitoring and adjusting process conditions, thus requiring less manual input.”
“In terms of controlling film thickness, automated systems have gotten more and more comprehensive to the point where you don’t need operator input at all,” Jones said. “I think you’re going to see more and more of that happening when you set up a film extrusion line. There’s a number of things you have to set up, which in the old days operators would do. They would look at things like the frost line and adjust settings to get it to a particular position. Machinery can now do that itself without the need for an operator to intervene, and I think that’s going to continue. It’s all about trying to get consistent product without the need to find technically savvy operators, which are harder and harder to find.”
Because many processors operate with very low profit margins, equipment manufacturers will continue looking for ways to boost efficiency by reducing consumption of energy and raw materials.
“There are different ways you could do that — mostly, it’s on machine design and control systems to try to make sure that whatever you’re producing is extremely uniform, and then you can minimize the amount of excess material you use,” Jones said. “Less material usage results in less energy usage. And a more uniform and consistent product results in a lower percentage of scrap, further reducing energy needs.”
Another efficiency trend is for machine direction orientation (MDO) units to be incorporated into stretch film lines. The MDO unit allows in-line production of very stiff film used for hand-wrapping pallets. At the same time, by bypassing the MDO, the same extrusion line can produce the very elastic stretch film used for machine wrapping pallets.
Incorporating the MDO units into the extrusion line instead of having them stand alone eliminates a separate step, increasing efficiency and reducing waste.
“Technically, that gets difficult, which is why it hasn’t been done a lot up to now because the machinery required to put all that together into the base extruder is quite tricky,” Jones said.
However, that technology has been developed, he said.
“They’re getting better all the time as machinery manufacturers get more adept at designing and controlling them,” Jones said.
Jones also foresees increased flexibility in the design of stretch film extrusion lines, so that they can produce a variety of stretch films, rather than being limited to one type.
Graham Engineering: Machine makers must innovate
The future will be demanding, meaning processors will need to innovate and machinery makers must follow suit, said David Schroeder, president and CEO of Graham Engineering.
“This means plastic processing machinery companies not only need to welcome customization but develop product architectures that enable the possibility,” Schroeder said.
Equipment manufacturers will place more emphasis on next-generation controls with seamless connections to upstream and downstream equipment and factory management systems, Schroeder said. Improvements will be made in the areas of predictive maintenance and quality control.
“Utilizing an advanced controls platform gives the plant quality and management systems data to analyze and trend, resulting in higher uptime, improved quality and a number of other equally important benefits,” Schroeder said. “Also, a continued focus on operator and technician safety, particularly in the way of electrical safety, puts more emphasis on controls platforms that allow the electrician to gather data without opening panels.”
While processors have always expected machinery suppliers to stay current with technology, to build machines meeting their requirements and to be responsive, those expectations will be particularly challenging in the future, he said.
“In the coming decade, the focus on communications, material source reductions such as lightweighting, and a circular economy place even more demands on the equipment supplier to continuously enhance their offerings,” Schroeder said.
Processors are demanding flexibility. “Processors want their capital equipment, such as extrusion systems, to be able to handle multiple materials, to adapt to the changing needs of their marketplaces,” Schroeder said. “Knowing what the processor currently extrudes and adding potential secondary resins during the project engineering phase allow us to provide a system that is capable and flexible.”
As an example, Schroeder pointed to the company’s development of a rotary blow molding system that allows for easy changes in bottle design.
“Anticipating changing market needs, not only in terms of polymer choices, but size and shape, requires close communication between the equipment supplier and the processor during the engineering phase of the project,” Schroeder said. “For an example, I will use our extrusion blow molding wheel technology. If a processor or CPG [consumer packaged goods company] believes that a certain bottle shape may change in the future, we may suggest our Revolution MVP technology, which allows for simple and inexpensive changes to the bottle height without significant capital investment and downtime.”
Designing machinery to be modular makes this type of flexibility possible, he said.
Control systems that also can monitor and control the auxiliary equipment will continue to evolve, Schroeder said.
“Graham Engineering embarked on an aggressive path 14 years ago to develop our own controls system, the Navigator series of controls. Using a Beckhoff industrial PC and a Windows-based platform, this constantly evolving system has proven to be incredibly effective at integrating with other factory machinery while also giving the processor more control and operating features than the older PLC-based platforms,” Schroeder said. “We expect to continue to develop new features and functionality to the controls platform in order to bring the processors into a new place with regards to machinery communications, such as in the areas of predictive maintenance and quality control.”
Graham Engineering Corp. sells single-screw extruders and extrusion systems under the Graham Engineering, American Kuhne and Welex brands.
Davis-Standard: Cutting downtime
Future equipment will have greater versatility for processing a range of resins and producing sheet with less material, especially for disposable or recyclable packaging, according Steven R. De Angelis, VP of the sheet, fiber, foam and reprocessing group.
“The influence of green processing will be seen in machinery developments that promote limited environmental impact on the total lifecycle of a given product,” he said. “We will also see a rise in combination technologies such as an extrusion coated barrier layer structure processed on a thermoformable sheet, to be made in one step with one station.”
Manufacturers will develop equipment that is more efficient and less prone to operator error.
“Just as AC drives have replaced DC drives, we will see the elimination of discrete controls,” De Angelis said. “They will be replaced by single-screen HMI controls for ease of setup and continued line repeatability. With the onset of IIoT and long-term data analysis, we envision a future with limited to zero machine downtime. Preventative and predictive maintenance will help processors avoid unmanaged part and machine failures.”
Downgauging of sheet and efforts to push the boundary lower will be another trend. Greater automation and “hands-free” extrusion will become more commonplace, “supporting repeatability of the end product with less variability introduced by operators,” he said.
“We believe the most significant demand is added support from OEMs in terms of process and engineering expertise,” De Angelis said. “Processors will continue to lean on OEMs for not only machinery but a complete process — just as a car dealer hands over the keys and you can start the car and drive. This is especially true as specific product lines become more mature.”
Innovations in screw design and downstream web cooling and handling will allow for production of thinner gauges of sheet and the use of more recycled content, according to Davis-Standard.
IIoT technology advances will lead to greater data collection and implementation of best practices by OEMs relating to machine design, process conditions and, most importantly, the ability to accurately predict equipment failures to prevent downtime.
“We feel this is a rapidly expanding capability that will very shortly become integral on every machine, just as digital surpassed analog control,” De Angelis said. “The DS Activ-Check System is a perfect example.”
DS Activ-Check is Davis-Standard’s cloud-based system for improving productivity. The system provides early notifications of potential failures through real-time tracking of preventive maintenance. The system offers long-term secure data storage, tracking and storing of key performance indicators and process analytics, machine monitoring, maintenance task management, and dashboards with performance data.
Brückner: Efficiency is key
Plastics processing machinery in the future will need to operate efficiently and produce sustainable products capable of being recycled, said Brückner spokesman Karlheinz Weinmann.
In addition, overall equipment effectiveness will be key, he said. Machinery must experience minimum downtimes and require short setup times.
“Processors will ask for machinery that helps them produce sustainable products with better optical and mechanical properties, according to future recycling and environmental regulations,” Weinmann said.
Production lines will integrate more tasks in the future.
“The integration of subsequent processing steps is a trend,” Weinmann said. He cited an inline coater and the company’s LISIM simultaneous stretching technology as examples of equipment that can be integrated into the extrusion line.
LISIM technology, also known as linear motor simultaneous stretching, stretches film transversely, as well as in the machine direction, all at once. This results in better tensile strength and shrinkage behavior. Additionally, the contact-free process does not scratch the film.
Advances in control systems will result in reduced energy consumption over the complete production process, optimize raw material consumption and improve production planning with a goal of minimizing storage costs, Weinmann said.
Leistritz sees control improvements
Charlie Martin, president and GM of Leistritz Extrusion, foresees improvements to control units and greater development of Industry 4.0 standards.
“The proliferation of PLCs with data acquisition will facilitate lot-to-lot traceability and allow analysis of processes run months or years ago that are involved with failures in the field,” Martin said. “Industry 4.0 will become better defined and embraced, but in a more narrow scope than envisioned.”
As part of Industry 4.0, equipment will be better able to communicate due to standard PLC communication protocols, Martin said.
Bruce Geiselman, senior staff reporter
For more information
Brueckner Group USA Inc., Portsmouth, N.H., 603-929-3900, www.brueckner-usa.com
Coperion Corp., Sewell, N.J., 201-327-6300, www.coperion.com
Davis-Standard LLC, Pawcatuck, Conn., 860-599-1010, www.davis-standard.com
Graham Engineering Corp., York, Pa., 717-848-3755 https://www.grahamengineering.com/
Leistritz Extrusion, Somerville, N.J., 908-685-2333, www.leistritz.com/en
SML North America Service Inc., Gloucester, Mass., 978-281-0560, www.sml.at
US Extruders, Westerly, R.I., 401-584-4710, www.us-extruders.com
Bruce Geiselman
Senior Staff Reporter Bruce Geiselman covers extrusion, blow molding, additive manufacturing, automation and end markets including automotive and packaging. He also writes features, including In Other Words and Problem Solved, for Plastics Machinery & Manufacturing, Plastics Recycling and The Journal of Blow Molding. He has extensive experience in daily and magazine journalism.
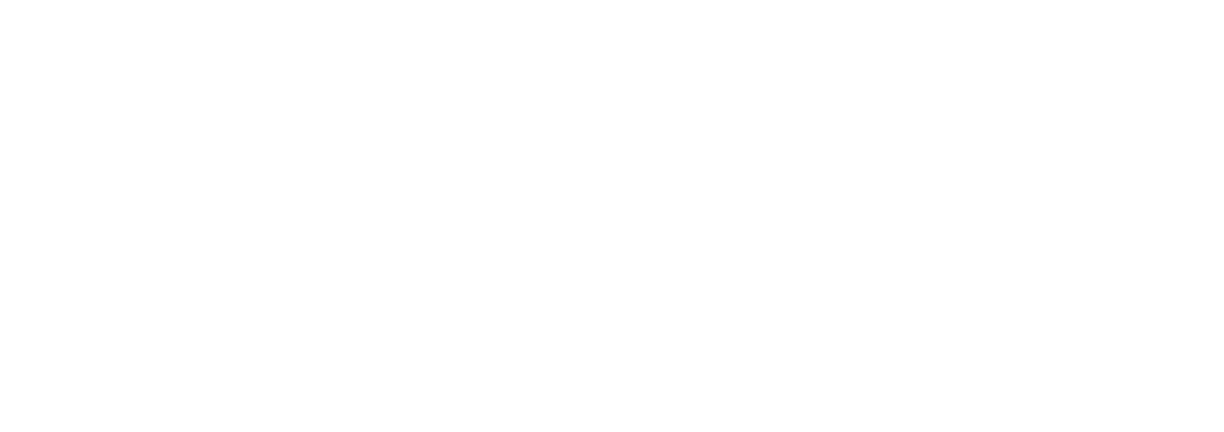