Environmental concerns spur demand for specialized extruders, CPM says
The green movement has created increased demand for specialized extruders, according to Adam Dreiblatt, director of process technology for CPM Extrusion, one of the largest companies selling twin-screw compounding extruders, including models designed for recycled plastics and bioplastics.
“It’s not like everybody and his brother is scrambling to get an extruder to process recycled plastic,” he said. Many smaller recyclers want to pelletize the plastic, which can be done using simple single-screw extruders.
Related: Graham customers devoting extruders full-time to bioplastics; Entek sees increased demand for compounding extruders; Milacron tailors screws to meet demand
However, many companies are looking for ways to reduce raw material costs and are increasing their use of recycled plastics as part of their sustainability efforts. The auto industry is one area in which recycled and recyclable materials increasingly are used, Dreiblatt said.
Dreiblatt said he also believes there may be a small increase in interest in bioplastics, like PLA, because manufacturers can market their products as biodegradable. In some instances, PLA can produce superior properties, such as when it replaces PS in products such as candy wrappers, he said.
While PLA is commercially compostable, one of the challenges is that few municipalities in the U.S. have a composting infrastructure, and most bioplastics are not compatible with traditional recycling streams. However, there are some sustainable plastics, like green PE, that can be made from sugarcane. They are expensive but are direct replacements for hydrocarbon-based plastics. That means those green plastics are processed in an identical fashion to their traditional counterparts and can be recycled.
Dreiblatt echoed opinions voiced by others that compounding extruders used for recycled plastic need additional venting and possibly the use of vent stuffers due to increased moisture and volatiles in the plastic.
“In addition to moisture, that stuff has been processed at least once before, so it will generate more gases and vapors when you melt that a second time around,” Dreiblatt said.
For bioplastics, moisture can be an even more significant problem because many of the natural fillers and fibers used in bioplastics contain as much as 10 times more moisture than traditional plastics, he said.
“The second challenge with bioplastics, because of the moisture, is corrosion,” Dreiblatt said.
Stainless-steel alloys in screws and barrels and other components can prevent corrosion, he said. However, that can lead to a slightly higher equipment costs.
In addition, because bioplastics tend to be more temperature-sensitive that traditional plastics, processing speeds may need to be adjusted, resulting in decreased production, he said.
Feeding natural fibers, like hemp, also can be a challenge, Dreiblatt said. Traditional feeders designed for materials like glass fiber might not work well with lighter-weight natural fibers, he said.
While companies engaged in closed-loop recycling usually don’t need to worry about consistency of their raw materials, it can be a significant challenge for companies buying recycled plastics from various sources.
“There can be tremendous lot-to-lot variation in melt flow, contamination and moisture vs. virgin resin,” Dreiblatt said. “This doesn’t affect the machine hardware itself, but requires different operating conditions such as screw speed, temperature settings, etc. each time to produce the same properties. This makes it especially challenging for the production staff.”
One way to improve consistency is to combine material from numerous lots prior to processing. That requires significant floor space to store resin and large blenders to combine it.
Depending on the level of contamination, which can vary from lot to lot with recycled plastic, specialized screen changers with large surface areas designed for recycling are sometimes necessary.
Bruce Geiselman
Senior Staff Reporter Bruce Geiselman covers extrusion, blow molding, additive manufacturing, automation and end markets including automotive and packaging. He also writes features, including In Other Words and Problem Solved, for Plastics Machinery & Manufacturing, Plastics Recycling and The Journal of Blow Molding. He has extensive experience in daily and magazine journalism.
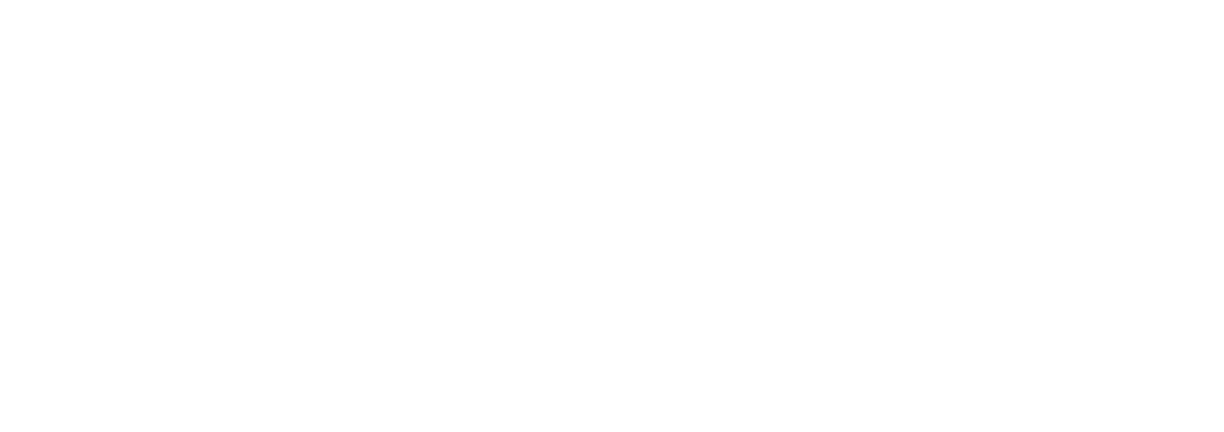