“The DS-Blend is a patent-pending design to improve the performance of a single-screw extruder for difficult mixing applications,” said John Christiano, VP of technology. “It’s used to provide both distributive and dissipative melt mixing.”
Distributive mixing involves homogenizing compatible melted resins, while dissipative mixing involves combining melted resin and unmelted material, such as fillers.
A typical application for the new mixing section would be mixing high concentrations of fillers, such as talc and calcium carbonate, with PP for sheet production. In those instances, the DS-Blend mixing segment is incorporated into the screw of a two-stage, vented single-screw extruder.
“The optimum, two-stage DS-Blend screw design achieved a similar output to a single-stage barrier screw, achieving a much lower melt temperature while using less energy,” Christiano said.
The result is a thorough mixing of PP with high concentrations of fillers and additives while controlling melt temperature. It also is ideal for use in mixing high-viscosity polymers, Christiano said.
The design “uses unique geometry to improve distributive and dissipative melt mixing performance,” he said. “This is accomplished by varying the channel geometry to improve mixing while reducing pressure drop. This helps to improve energy efficiency while maintaining a low melt temperature.”
The number of channels, helix angles and channel depths can be varied to optimize mixing performance.
The DS-Blend screw elements are custom- designed for each customer’s particular application. They can be installed on new or existing single- screw extruders from Davis-Standard or competitors. The company encourages customers who are interested in seeing the technology in operation to visit the Davis-Standard R&D facility in Pawcatuck, Conn., where the company is headquartered.
The company introduced the DS-Blend as part of its efforts to meet an increasing demand among customers for equipment that can successfully compound PP with high concentrations of fillers for sheet production.
“We see a big uptick in that market,” said Steve DeAngelis, VP of sheet. “There are really two reasons behind it. One, obviously, the filler is much cheaper than the resin, but the other half to it is being able to say it is a green product because it has less plastic in it.”
To meet the needs of plastics processors using large proportions of fillers, Davis-Standard is equipping more of its extruders with vents to eliminate volatile compounds that are common when nonorganic materials, such as fillers, are introduced. Also, the company has changed the vent design.
“We have gone to oblong or oval vents to allow for higher surface area within the vent,” DeAngelis said. “Instead of having a circle, we go to an oval and expose more surface area of the melt with the filler in it to the vacuum or atmosphere.”
Without adequate venting, finished plastic products can have bubbles and other defects.
The company has also altered the screw metallurgy for those customers blending in high concentrations of highly abrasive fillers, which otherwise would shorten the life of a screw.
“We have typically gone from the standard Colmonoy 56 and X101 materials from Nordson and gone to their X-800 with our blend of Colmonoy 83, which is a matching material, and then we get into different coatings like plasma coatings,” DeAngelis said.
Colmonoy 83 and X-800 are trade names of Nordson’s hardening materials that are welded onto the surface of the screws to add wear-resistance.
“Different types of plasma coatings have been used to encase the screw to, again, promote longer wear and in some cases are necessary when you are running these sorts of fillers,” DeAngelis said. “In the case of fillers, you need a lot of abrasion-resistance.”
Bruce Geiselman, senior staff reporter
Contact:
Davis-Standard LLC Pawcatuck, Conn., 860-599-1010,
Bruce Geiselman
Senior Staff Reporter Bruce Geiselman covers extrusion, blow molding, additive manufacturing, automation and end markets including automotive and packaging. He also writes features, including In Other Words and Problem Solved, for Plastics Machinery & Manufacturing, Plastics Recycling and The Journal of Blow Molding. He has extensive experience in daily and magazine journalism.
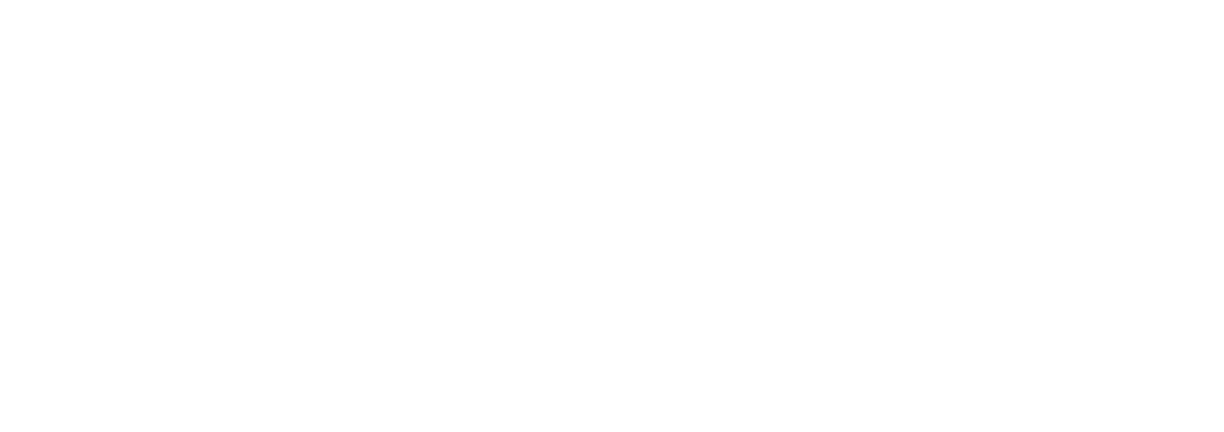