Problem: The breakdown of a puller/cutter forced an extrusion company to cut certain types of tubing by hand.
Solution: After initially not meeting the company’s demanding machine specifications, Versa Machinery designed a puller/ cutter that exceeded requirements, dramatically reducing cycle times.
Hudson, Ohio-based HEI has a puller for each of its 11 extruders and several servo-cutters that it designed in-house. But the company’s only puller/cutter that could perform angled, high-speed cuts broke down and was beyond repair.
HEI produces a wide variety of plastic tubing with outside diameters ranging from 0.04 inch to 6 inches. The plant uses 14 resins, including PE, PP, flexible vinyl, rigid PVC, nylon 6, nylon 11, nylon 12, PC, acrylic and urethanes.
The company manufactures stock and custom products, including tube to test underground water levels, and tube for dishwashers, fish tanks, hula hoops and sprayer bottles that require 45-degree-angle cuts.
The cut is a critical feature required by many of HEI’s customers, who often need one end of the tube cut straight and the other cut at an angle. Finding a manufacturer that could build a puller/cutter to meet HEI’s demanding requirements proved difficult, and the ISO 9001-certified company was forced to revert to making those angled cuts manually.
“We could cut 12 pieces a minute by hand, which is 720 pieces in an hour,” HEI plant manager Keith Kramer said. “When we got the new puller/cutter from Versa Machinery online, we could cut 720 pieces in a few minutes.”
But getting that high-speed cutting capacity online wasn’t easy. HEI contacted Versa Machinery in Elkhart, Ind., and Versa agreed to tackle the project.
Versa is a 70-year-old company that supplies downstream equipment for plastic and rubber extrusion. It designs and manufactures feeders, cutters, conveyors and lathe-control systems. But Versa had never built a puller/cutter that could run as fast and as accurately as the machine HEI was seeking, which was a double-angle cutting system that could cut a tube with a straight cut on one end and an angled cut on the other. It needed to make cuts to within 0.01 inch of specifications or better while cutting at speeds as fast as 300 feet per minute.
“We had sold double-angle cutters prior to this, but HEI required a higher level of accuracy. We built three different machines for a company in Mexico to cut at different angles on each end,” Washburn said. “This was an opportunity to improve dramatically on those machines. It took a lot of re-engineering to achieve 300 feet per minute, because our machines ran at about 150 feet per minute.”
Versa’s first attempt at building the puller/cutter fell short of HEI’s expectations. The good news was that HEI got a full refund of its down payment; the bad news was that workers still had to make the angled cuts themselves. Washburn told HEI that Versa would continue working on the machine. Versa learned that in order to build it, the company had to completely redesign its standard ACT series puller/cutter.
Two years later, Versa had done just that, and Washburn contacted HEI to let one of its owners know that Versa had built an automated puller/cutter that could meet the company’s requirements.
“I still remember that day,” Kramer said. “Harry emailed one of our owners and said they built the machine. I was in shock because this was off my radar. When a company can’t build your machine and they tell you, ‘We’ll keep working on it,’ it’s unheard of for them to come back and fix it. But they came through for us.”
Washburn said Versa had to redesign the layout of the two cutters to get the bushing holder, where the cutting is done, down to a minimal size.
“With our previous cutters, the shortest cut you could make was 5 inches,” he said. “Now we can make a cut at 1.25 inches.”
Achieving the required accuracy was the main challenge, he said.
“We had to use a master drive for both cutters and a slave drive, which is a brainless drive with no computing ability, for the puller,” Washburn said. “Each cutter can think for itself and work independently. The puller is always communicating to those two cutters its exact position, how fast it is going and how far it has gone. Each cutter can react to the speed of the puller, so the cutters will speed up or slow down based on the speed of the puller.”
The new puller/cutter can operate in three modes: on-demand mode, cam mode or flywheel mode. On-demand mode resets the knife to a home position after every cut for maximum accuracy. Cam mode allows the machine to cut short lengths at full knife velocity without stopping, while flywheel mode rotates the knife at a constant speed for high cutting rates. Versa-designed software that is built into the master drives of each cutter head automatically selects the best mode for each application, Washburn said.
All the redesign work paid off. HEI went to Versa to see the new machine and bought it during that visit. But the story doesn’t end there.
“When we delivered the machine, we saw how HEI was using it, and we said we were working on a software upgrade to store hundreds of recipe files,” Washburn said. “They expected a basic machine with a few software options or controls. Their jaws dropped when we showed it to them. There is a remote control that you can hook a laser outside-diameter gauge to; you can control the speed of the puller from that. Plus, we loaded a program for them to pull up hundreds of different recipes to cut different parts. After you load that, it will automatically pull out of its memory the line speed, the cut length, the knife rotational speed, as well as a lot of other things that they probably don’t use.
“This is a one-of-a-kind machine,” Washburn said. “We are looking for other applications, but we’ve been so busy we haven’t had time to go out and look for other customers who might want to buy it.”
The new machine can cut tubes with outside diameters of 1 inch or less. It achieves accuracy to within 0.003-inch tolerance at 300 feet per minute, which exceeds HEI’s requirements of 0.01-inch tolerance at that speed. It can make up to 1,800 cuts per minute in double-angle-cut mode or 3,000 cuts per minute in single-angle-cut mode.
“We could build it to handle larger tubes, but there is no apparent need for that,” Washburn said. HEI is using the machine to cut dip tubes for spray bottles.
The standard machine costs about $60,000, he said, but HEI’s machine cost more due to several custom items, including a waterproof cabinet.
Kramer said HEI uses the new machine only for angled cuts and uses its other cutters for straight cuts.
“We could use the machine daily, but we choose not to,” Kramer said. “We only have one, and we don’t want to beat it up.”
Bruce Adams, senior staff reporter
Contact:
Versa Machinery Elkhart, Ind., 574-266-0780
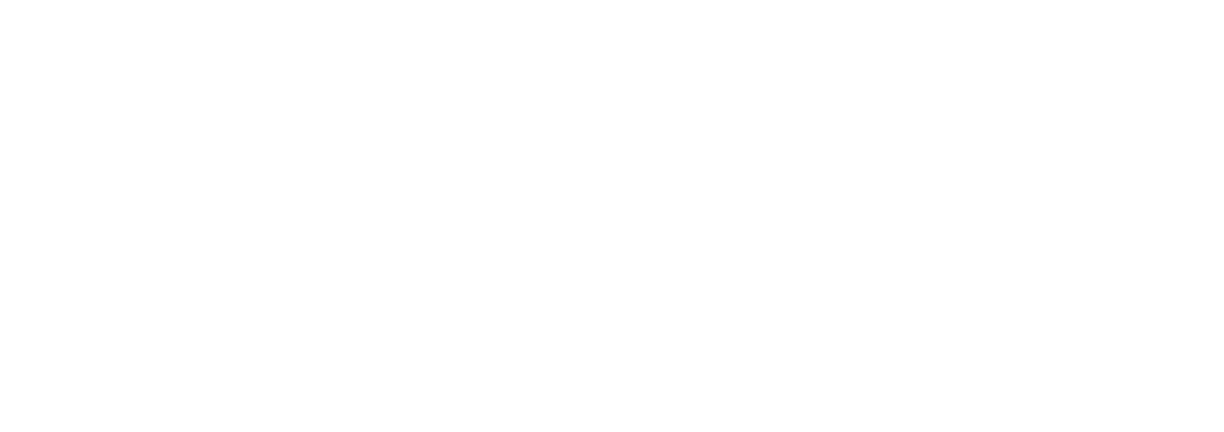