Origin, based in San Francisco, made its debut at Rapid + TCT, held May 20-23 in Detroit, with its Origin One 3-D printing system.
It has taken several years to get here, but the company believes it has what the market wants: a machine primed for mass production with a portfolio of materials unmatched in the industry. The materials are made possible through strategic partnerships with companies like BASF and Royal DSM, which are developing them specifically for the Origin One; many more partnerships are still to be announced. Officials said that Origin One has successfully printed more than 50 different resins from material partners, and the company has made 13 of those available to customers; several more will become available in the fall.
“We are a software-focused company,” said Chris Prucha, CEO, who co-founded the company with Joel Ong, its CTO. “We built Origin as a software-focused company to improve the 3-D printing process.
“Our analogy is that it’s like a self- driving car,” Prucha said, noting that the smartphone industry influenced the technology. “The printer itself has six processors, three cameras, thermal imaging and dozens of other sensors.” The data is recorded in real time, and the printer constantly adapts to change the print process in a closed feedback loop.
The machine has a compact footprint — 1.3 feet by 1.5 feet by 3.6 feet — and a build volume of 7.6 inches by 4.3 inches by 1.1 feet. Its programmable photopolymerization process precisely controls light, heat, humidity and other variables when converting resins into isotropic parts that are ready for end use after post-processing. For the uninitiated, isotropic means having uniform physical properties when measured in different directions like injection molded parts, a key factor when creating parts via 3-D printing.
According to Origin, the isotropic parts achieve peak mechanical properties and require minimal supports. The machine continuously monitors the prints via vision and other types of sensors. Its software has responsive algorithms that allow it to provide quality assurance in process. It prints at a voxel resolution of 50 microns in the X and Y direction, lower in the Z. The printers, which will begin shipping in the fall, can be heated to enable the printing of viscous resins and new chemistries that are not yet commercially available, officials said. The heating technology is an upgrade over the company’s beta-version printer.
Finished parts require no polishing, baking or dyeing. After a part is printed, it is bathed in a solvent — acetone, isopropyl alcohol or glycol ether TPM — then is UV-cured. The machine is offered on a subscription basis at a rate of $1,500 per month.
“A lot of systems are leased,” Prucha said, referring to other brands of 3-D printers. “A lot of systems are purchased. All of ours are done on a subscription basis.”
The company recently announced its partnership with footwear maker Ecco, which is using BASF materials with the 3-D printing system. Ecco is using the Origin platform at its R&D center at its headquarters in Bredebro, Denmark. It is printing with Ultracur3D elastomeric reactive urethane photopolymer from BASF, Ludwigshafen, Germany. A BASF official said that Origin is able to achieve consistent Class A surface finishes.
It’s an example of how Origin also is partnering with materials suppliers, including DSM and Henkel. Ten more material partners are yet to be announced. Origin provides the tools to develop and validate new materials, and the materials are engineered so that they have extended shelf life and are easy to handle, print quickly and can be rapidly post- processed. The materials include elastomers with elongation at break above 300 percent; biocompatible materials that have been assessed for the ways in which they might exhibit cytotoxicity, or cause humans irritation; and optically clear resins.
“We led off with the materials partnerships,” Prucha said. “That is the message with Origin One, that we’re investing in enabling a diverse set of new materials chemistry. Our customers can invest in one system and print all the materials that are available across those partnerships.”
More research is being conducted in materials. Origin’s investors include Stanford University, which is doing development work on materials it believes will be significant in the future. Prucha noted that Origin does not take any margin on its material sales.
“That makes us neutral. There are no kickbacks. We are completely neutral there. We offer economies of scale, lower price and customers can truly choose the material that is best for them.”
Angie DeRosa, managing editor
Contact:
Origin San Francisco, 415-943-6850
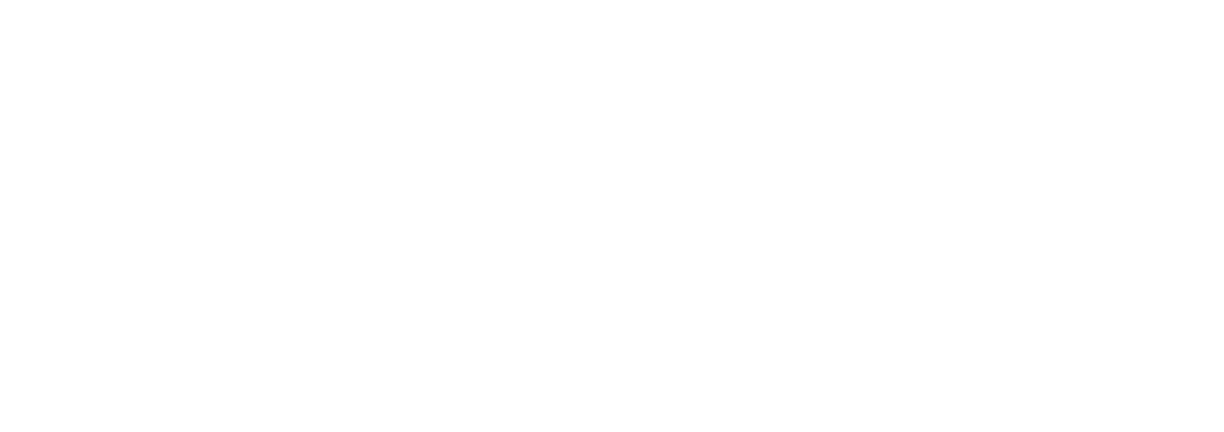