Historically, single-screw extruders have been considered inferior to intermeshing co-rotating twin-screw extruders for compounding. However, Keith Luker, president of Randcastle, said his company has developed a "3-D mixing screw" that can outperform twin-screw extruders.
Randcastle began marketing what it calls its 3-D Elongator mixing screw about a year ago, Luker said.
"By a show of hands, how many of you here believe heretics should be burned at the stake?" Luker jokingly asked attendees of the Extrusion 2017 conference in Charlotte, N.C., Oct. 18-20. "Three of you. I want the rest of you to protect me from those three."
Luker said that while twin-screw extruders are widely thought of as the best choice for mixing or compounding plastics, he developed — partly by accident and partly by design — a single-screw technology that is superior for mixing plastics.
Twin-screw extruders work by stretching the melt in two directions, Luker said. They repeatedly elongate the plastic melt widthwise and lengthwise, randomly distributing the materials being blended. Luker worked for years on developing a single-screw design that could replicate the performance of twin-screw extruders, he said. The advantage to mixing with a single-screw extruder is that the equipment is significantly less expensive.
Twin-screw extruders aren't perfect, Luker said. The melt isn't stretched uniformly. Some material isn't stretched at all, and some is stretched more than once. The result is that materials aren't perfectly mixed. There can be agglomerations of materials after the melt goes through a twin-screw extruder.
Luker describes mixing with a twin-screw extruder as "chaos." However, he said mixing with his company's new screw is more uniform, avoiding agglomerations of materials.
It was only after Oak Ridge National Laboratory purchased one of Randcastle's extruders with a mixing screw that Luker discovered how effective the screw was and figured out why. The government purchased the extruder to mix carbon nanotubes with polymers.
At the time of the purchase, in 2010, Luker thought his patented screw design only stretched materials along two axes — length and width. However, the government did what Luker couldn't afford. It analyzed the end product under an expensive scanning electron microscope and took detailed photos that showed the uniform dispersal of the carbon nanotubes. Luker said there were no agglomerations, and he was puzzled by the success.
"These pictures confused the hell out of me, and I didn't want to publish them because, quite frankly, I didn't understand how it could be that good," he said. "But, eventually, if you keep thinking long enough, you might solve it."
Luker eventually concluded something unintended was happening in the extruder — there was a third dimension of mixing. In addition to stretching the melt along length and width, the final section of the screw was folding the melt into itself. To better visualize what is taking place, Luker said to envision the melt rolling in a circle.
After studying the photos from the scanning electron microscope and concluding a third dimension of mixing was taking place, Luker modified his screw design. He increased the size of the third channel in the screw to maximize the folding effect, he said.
That led to the release of the new mixing screw about a year ago.
Bruce Geiselman, senior staff reporter
Contact:
Randcastle Extrusion Systems Inc.Cedar Grove, N.J., 973-239-1150, www.randcastle.com
Bruce Geiselman
Senior Staff Reporter Bruce Geiselman covers extrusion, blow molding, additive manufacturing, automation and end markets including automotive and packaging. He also writes features, including In Other Words and Problem Solved, for Plastics Machinery & Manufacturing, Plastics Recycling and The Journal of Blow Molding. He has extensive experience in daily and magazine journalism.
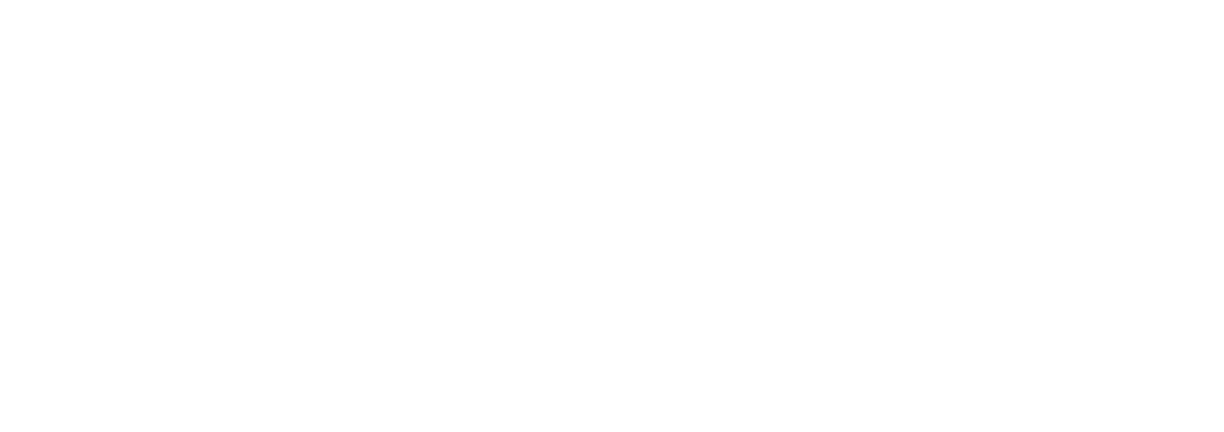