Makers of thermoforming equipment have improved operating speeds, increased versatility, and added automation and other features to new and upgraded models that debuted at K 2019.
Gabler Thermoform
Gabler Thermoform has redesigned its Swing 3 thermoformer for cups, lids and bowls to make it more accommodating of frequent product changes.
The new thermoformer is suitable for all commercially available thermoplastic resins, including recycled PET.
“This is a good machine for markets where the customer needs quality but does not have high volumes,” said Gary Sowden, North American sales director for Gabler, during an interview at K 2019.
“The U.S. mindset has historically been ‘bigger is better,’ ” Sowden said. “But that is changing. People are finding that not everything is a 500-million parts run.”
Gabler said the new Swing 3 has a small footprint and low material and energy consumption. These attributes make it cost-efficient for shorter production runs.
The maximum film width is 27.6 inches, and the forming area is 23.6 inches by 10.7 inches. The standard depth of draw is 7.1 inches.
The maximum closing force is 33.2 tons. The top heater consumes 39.6 kilowatts per hour, and the bottom heater takes 26.4 kilowatts per hour.
The machine’s footprint, including the control cabinet and stacking and counting device, is 19 feet long, 10 feet wide and 10.5 feet high.
The Swing 3 has a patented drive system consisting of just one servo drive, cam and sliding block guide for mechanically coupled lifting and swiveling motion. It can produce as many as 50,000 cups per hour.
The thermoformer forms and punches in a single step to improve product quality and reproducibility.
An integrated tool-changing system enables changes in one hour or less.
The control system now has a user-friendly HMI display.
The stacking and counting function permits products to be stacked either vertically and horizontally. Changeover between different parts is easy to adjust, Gabler said.
The Swing 3 is compatible with many peripheral devices and can interface with IoT systems through Siemens’ MindSphere cloud platform.
Gabler said the Swing 3 is Industry 4.0-ready and includes integrated sensors and remote access.
WM Thermoforming
WM Thermoforming launched a new steel-rule-die machine it said features better parallel stability, cutting resolution and die longevity. The machine can be used with an extensive variety of molds without major modification of the molds.
WM Thermoforming executives at K 2019 described the Flex 92 as breakthrough technology that gives users more choices in what they can manufacture on a single thermoformer and that provides consistent quality and extreme flexibility.
The Flex 92 has a maximum forming area of 36.2 inches by 27.5 inches, and maximum forming depth of 6.3 inches.
At K 2019, the machine was running a 24-
cavity mold manufacturing 36,000 PP food container lids per hour. The sheet was 0.018-inch thick.
The Flex 92 features a moveable clamping frame, plug assist and an electric ejector.
Heating elements are ceramic with individual temperature controls.
WM Viewer, a remote interface that allows real-time monitoring of the machine via smartphone, tablet or PC is standard.
The controller includes a machine learning system for initial settings of cycle parameters that optimize machine sequencing and increase output.
Kiefel Technologies has upgraded two popular thermoforming machines — the KTR 5.2 Speed cup-forming machine and the Speedformer KMD 78.2 Speed steel-rule system. The company made major improvements in forming speed and intuitive operator controls.
“Despite achieving a significant increase in performance, we have not had to increase the footprint,” said Christian Stockinger, head of engineering at Kiefel Packaging, in describing the new KTR 5.2 Speed.
He said the drivetrain has been redesigned to be more rigid, which reduces vibration throughout the system. A new motor-gearbox combination can run at 50 cycles per minute. Punching force is 45 tons.
The new forming station also includes a backlash-free upper yoke adjustment function.
The forming area is 29.5 inches by 15 inches and the maximum part height is 5.9 inches.
Forming air lines have been optimized to reduce filling time by 25 percent and venting time by 30 percent, Kiefel said. The company also has optimized the rapid tool-changing system.
Stockinger said the nominal heating capacity has been reduced by about 15 percent without sacrificing heat input. To achieve this, Kiefel reduced the distance between the heating elements and the film, insulated the heating elements better and improved the temperature and process control.
The KTR 5.2 Speed has two separate cooling circuits for the upper and lower tools and an extended sensor system for more precise control. Start-up automation is also sensor-controlled.
The new machine also comes with the Kiefel Speedstacker, which is designed to stack a variety of different-sized products. Its operation is controlled through the single-system control panel.
The control panel has pictograms and graphics that help the user set machine parameters and diagnose faults. Kiefel said non-experts can use the control system.
The new Speedformer KMD 78.2 Speed is suitable for both food and non-food products. It has a 20 percent higher heating capacity than its predecessor but uses less energy. It also has an energy-recovery system that further improves energy savings. The heating system uses black HTS ceramic elements.
The company has redesigned the film feed table to gently guide the film to the film transport system. Kiefel said this feature reduces waste.
Improvements have been made to the tool-change system to shorten setup times.
The maximum tool size is 30.7 inches by 23.6 inches, and the maximum part height is 5.9 inches.
The stacking station can stack up or down, or in tilted or pick-and-place modes.
The operator needs to input only a few parameters to start operation. The rest are automatically determined by installed algorithms. The display shows the entire forming process and other important processes and functions. Operator training is easier, Kiefel said.
Kiefel is a unit of the Brückner Group GmbH, headquartered in Siegsdorf, Germany.
Thermoforming equipment manufacturer Brown Machine Group introduced the ComPack-series case-packing system to take advantage of demand for automation due to a shortage of labor.
“The growth we have seen over the last two years for automation has been substantial,” said Bob Gordert, the VP of sales and marketing at Brown.
Brown introduced the HTP-1 case packer in 2018 and since then the market for case packers has gained momentum, Gordert said. “With the lack of skilled and general labor, the demand for automation increases by the day.” Brown has increased its sales and engineering staff because of the demand.
The company said that since the HTP-1 was introduced, numerous features have been developed and improved for the ComPack series, particularly for reducing floor space and increasing flexibility in configuring the packer for different jobs. Gordert said the ComPack series uses only one-third as much floor space as some competing units.
The ComPack-series case packer erects cases and packs products sequentially within the same machine. It is initially targeted at food and beverage products, but Brown said it will be developed for additional products.
The case packer has a powder-coated steel frame, Allen-Bradley CompactLogix PLC controls with a high-resolution touch screen and Lexan guarding.
Brown said the control system is user-friendly with intuitive controls for easier training and operation.
The unit features servo-driven linear guide movements and the capability for remote access for service support. It comes in side- and top-load configurations.
Options include quick-change parts, multiple lane feed systems and bottom and top case sealing capability.
At the K show, the ComPack case packer received individually wrapped sleeves of cups and positioned them in a pre-set pattern. It then placed the staged sleeves into an erect carton, and closed and sealed the box. The loaded carton was then pushed out of the packer.
The ComPack system can be adjusted to accommodate different sizes of boxes and different products.
For more information :
Brown Machine Group, Beaverton, Mich., 989-435-7741, www.brownmachinegroup.com
Brueckner Group USA Inc., Portsmouth, N.H., 603-929-3900, www.kiefel.com
Gabler North America, Louisville, Ky., 989-615-6365, www.gabler-thermoform.com
WM Thermoforming Machines SA, Stabio, Switzerland, 41-91-6407050, www.wm-thermoforming.com
Ron Shinn | Editor
Editor Ron Shinn is a co-founder of Plastics Machinery & Manufacturing and has been covering the plastics industry for more than 35 years. He leads the editorial team, directs coverage and sets the editorial calendar. He also writes features, including the Talking Points column and On the Factory Floor, and covers recycling and sustainability for PMM and Plastics Recycling.
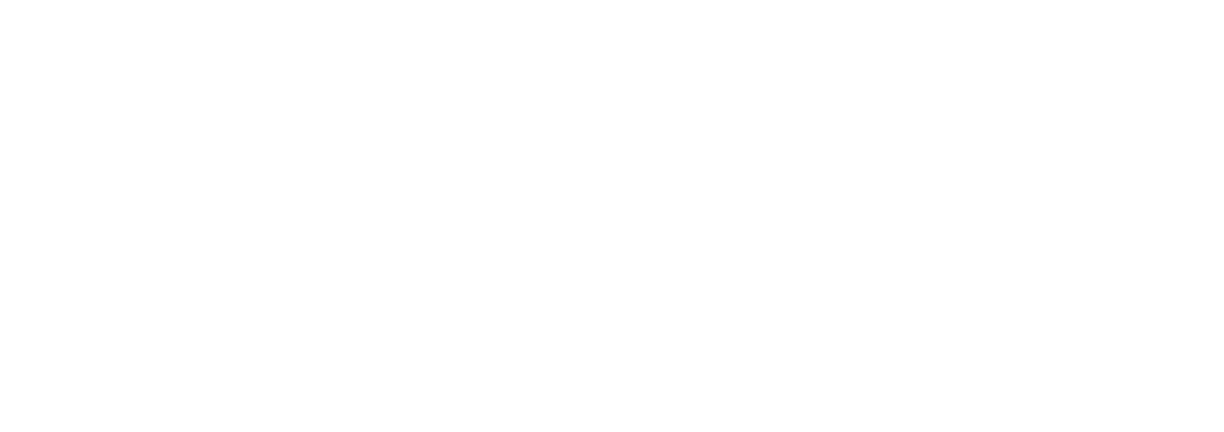