S-Max Dual 6 Capable of chopping up large sprues and parts, this screenless granulator from Wittmann has been designed for central scrap reclamation. It has two counter-rotating cutting rotors, six blades, eight toothed rollers and a stainless steel feeding chamber. An optional feeding shaft keeps large parts in motion and cuts them to size before sending them into the hopper, reducing the chance for material bridging or overflow. An optional Automatic Reversing System, which allows the rotor to reverse for better part positioning under heavy load, also is available. Featuring a cutting chamber of 20.8 inches by 18.4 inches, the S-Max Dual 6 can achieve a maximum throughput of 88 pounds per hour.
What’s new? The granulator, which offers improvements over Wittmann’s comparable Junior Double 6, or JD-6 granulator. Like the JD-6, it has two 2.2-kilowatt motors, but, to save space, the units are installed vertically. Redesigns of the JD-4 and JD-8 will follow later this year.
Benefits Compact size, safe operation and the ability to handle a variety of materials, including hard, brittle and glass-fiber-filled parts. The S-Max Dual 6 has been designed to minimize component wear, and the generation of dust, fines and noise; and it allows free access for maintenance and cleaning from the top.
Wittmann USA Inc., Torrington, Connecticut, 860-496-9603, www.wittmann-group.com/en/usa
Vital Statistics
Maximum hourly throughput |
About 88 pounds |
Cutting chamber |
20.8 inches by 18.4 inches |
Options for tooth size on toothed rollers |
5mm, 7mm, 10 mm |
Speed of rotation |
27 rpm |
Karen Hanna | Senior Staff Reporter
Senior Staff Reporter Karen Hanna covers injection molding, molds and tooling, processors, workforce and other topics, and writes features including In Other Words and Problem Solved for Plastics Machinery & Manufacturing, Plastics Recycling and The Journal of Blow Molding. She has more than 15 years of experience in daily and magazine journalism.
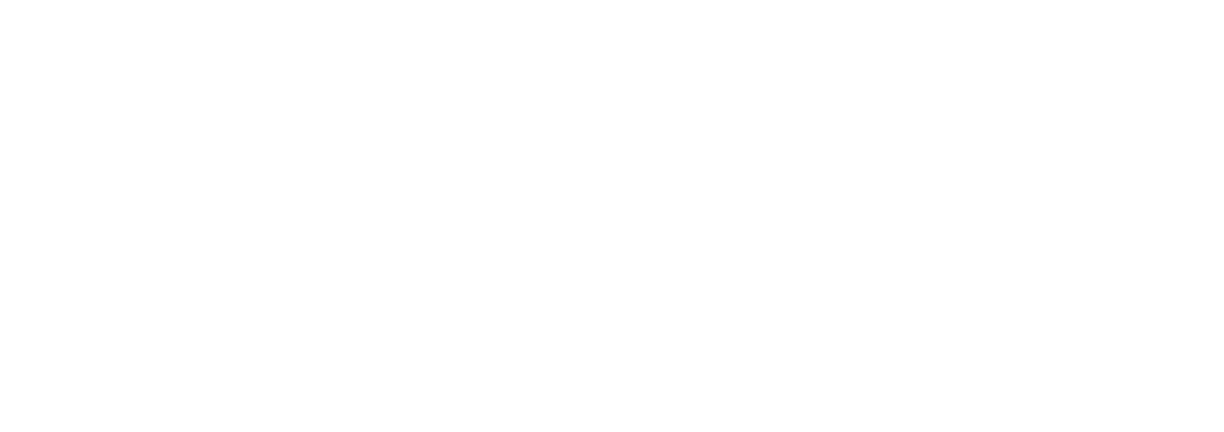