From the Spring 2024 issue of Plastics Recycling.
By Chris Voloschuk
The objective of Ocean Plastic Technologies always has been clear: to cut through logistical and economic challenges and make plastic recycling more accessible to communities lacking the infrastructure.
The company, established in South Africa in 2016, has developed a piece of equipment—the micro recycling pod (MRP)—and deployed it in six rural and lower-income communities across that country to help address social, economic and environmental challenges. The machine can fit inside a 20-foot shipping container and is portable enough to be stationed at or near sites where plastic scrap is generated. It also can be customized to fully process any type of plastic into flakes or pellets to be sold for manufacturing.
Since 2022, Ocean Plastic Technologies USA (OPT USA), the Chattanooga, Tennessee-based subsidiary of Ocean Plastic Technologies, has sought to deliver MRPs to various locations—from farms to factories to entertainment venues—in an effort to close recycling gaps throughout the Americas.
OPT USA President and CEO Americas Michael Vincent has 35 years of experience working in logistics for firms such as FreightWaves and Xpress Global Systems and has applied that knowledge to recycling along with co-founder and Chief Operating Officer Kenneth Martin, who moved to Tennessee from South Africa to help launch the business.
“With this technology, we can solve what I believe—and others believe—is a logistics problem of getting material from my hand, for example, into recycling and then back into manufacturing as quickly as possible,” Vincent says. “That’s the issue. Throwing [plastic] into the garbage and then trying to sort through millions of tons of garbage is not an economically viable way to recycle. There’s got to be a better way to do it.
“Right now, people are working on all kinds of really cool, nascent technologies like robotics. But what we saw was the opportunity to get recycling into places that are not big enough sources economically for larger recyclers to really worry about since it doesn’t work in their economic interest. So, if you scale it down, it [works] and it also gives you the ability to utilize this kind of sniper rifle approach instead of the shotgun approach to mine or go after specific sources of plastics that right now are difficult or not recycled,” he adds.
Making an impact
In South Africa, the company seeks to recycle plastics while also lifting up economically disadvantaged residents. “There’s huge disparities between different communities,” Martin says, adding that the company’s business model is to create “entrepreneurial opportunities for the community to put the power into their hands to clean up their communities and monetize the waste.”
Martin says Ocean Plastic Technologies works with nonprofits in those communities that oversee the daily MRP operations and employ locals to collect plastic scrap for processing. In exchange, those resident-collectors are paid in coupons to local grocers that can be redeemed for basic goods, such as bread, milk, beans and rice. The company doesn’t use cash because of security concerns.
“[People] in these communities might not even have running water or electricity, and they’re getting their water from the rivers,” Martin says. “So, as you can imagine, waste management is nonexistent. These communities are built around rivers, which lead to oceans. With our machines placed in the communities, they are seeing value in their plastic waste and they’re now bringing it down to our central hub where they get paid.
“We’re finding that the model’s working really well because a lot of these communities don’t have access to transport,” he continues. “Even if there’s a recycling center 10 or 15 miles down the road, they wouldn’t be able to get to that recycling center. [With the MRPs], you have some bringing their vehicles, but a lot of [scrap] is just brought on foot in a garbage bag daily, so they can go buy their bread and milk and feed their families for the day. The model for our micro recycling plants was born out of that need to get to the source of the waste.”
Vincent first learned of Ocean Plastic Technologies around five years ago when looking into producing guitar accessories from ocean plastics and jumped into OPT USA full-time in 2022. He wants to maintain the spirit of social impact while expanding its footprint to a multitude of locations., Earlier this year, OPT USA deployed a MRP in Chattanooga.
“The opportunities are there [across the Americas],” he says. “You’ve got the islands of the Caribbean that are completely dependent on tourism, for example, and have no recycling processes. So, obviously, they have a little bit more of a difficult economic time, and there’s those opportunities there. … Keeping that aspect to the company is very important to us.”
The process
The MRP measures 18 feet long and 9 feet tall and runs on about 90 amps, with its noise level registering at about 85 decibels, which Vincent compares with a vacuum cleaner or lawn mower.
The machine is assembled by the company in South Africa before shipping and is ready to use as soon as it is connected to a power source. In four steps, it can turn any type of plastic, including hard-to-recycle materials such as films and rigids, into flakes or pellets.
Scrap first is fed into a 2 ½-foot-by-2 ½-foot shredder box outfitted with 20 blades that can be customized to cut through whichever plastic type a user specifies and can process about 500 pounds of material per hour.
“If you’ve got low volumes, you can just sit there feeding bottles into it,” Martin says. “Or, with higher volumes, we can add a portable conveyor hopper system. So, you can just dump bags, and it takes [the material] up.”
Once shredded, the plastic goes through a two-stage cleaning process where jet nozzles spray the material with water and a cleaning solution, depending on the amount of contamination. Around 55 to 60 gallons of water are stored in a tank at the bottom of the machine and can be changed once per month or sooner, depending on what the MRP is processing.
During this process, water flows from the bottom of the shredder down into the secondary wash where additional jet nozzles are set up, then drains back into the tank through a two-stage filtration system with a water pump that continues circulating. “Once the water has reached the saturation level with contamination, then we just pump that out,” Martin says. “You’re looking at 55 to 60 gallons of water. Once it’s gone through the whole process, that can be used as irrigation water, for example.”
The shredded and washed plastic is dried in the third stage as it passes through a serpentine tube system. From there, it heads into a granulator where the remaining moisture is removed and the plastic can be pelletized or made into flakes ranging from 6 millimeters to 10 millimeters, depending on specification.
“Our solutions are customized to our customers’ application, so if it’s postconsumer waste, then our system is going to be different than the system for agricultural waste,” Martin says. “It’s the same with the pelletizing of it. If it’s postconsumer, it comes out as flake. If we’re going to be processing forms, it’s going to come out as a cold-rolled pellet because it’s more desirable for manufacturers and for their own densification and transportation of it.”
OPT USA works with MRP users via offtake agreements and handles the logistics of transporting gaylord containers of processed plastics away from a site and finding a buyer for them, sharing a percentage of the revenue with the client. Vincent adds that a site using an MRP can run the machine daily with its own staff, though OPT USA also can staff the machine. One to two individuals typically are required to operate the MRP.
OPT USA handles machine maintenance and provides data tracking through an app, allowing its customers to see where their processed plastics are going.
“The machine doesn’t get deployed and begin operating until there’s already that offtake agreement,” Vincent says.
Martin notes that while the MRP is a turnkey solution for a micro recycling presence, OPT USA does not set up collection programs in communities, for example. “We would look to partner with other companies on that side of it. You handle the collection, and we handle the processing, but we want to get as close to the source as possible.”
Where to?
Vincent and Martin have one MRP installed in Chattanooga but have been in discussions to install more at major retailers, sports and concert venues and rural communities that lack plastic recycling programs.
“We’re also talking to a major food and beverage company about utilizing these on a mobile scale to move from venue to venue to process plastics at stadiums, music events, places like that,” Vincent says.
Additionally, OPT USA has discussed setting up MRPs on farms to collect agricultural plastics, such as dripline tubing, throughout the Southeast U.S. and at marinas in the Great Lakes region to collect boat wrap.
“We have spoken to several [municipalities], especially around [Tennessee],” Vincent adds. “The interest is there. It’s figuring out how to fit in with those existing contracts [with haulers] that has been a bit of a challenge. So, it’s really going to those places where there isn’t already something set up.
“This is not designed to go in and disrupt a 20 or 100-tons-a-day New York City MRF, or even replace the MRFs here in [Tennessee],” he continues. “This is specific targets of specific places. A retail chain, for example, could use these. It could be so all their plastic bags could be brought back and processed right there on-site with that value right there to digital wealth transfer.”
For more information:
OPT USA, 423-322-4917, www.optusa.earth
Chris Voloschuk
Chris Voloschuk is Associate Editor of Recycling Today and can be reached at [email protected]. This story was published in Plastics Recycling, a joint publication of Plastics Machinery & Manufacturing and Recycling Today.
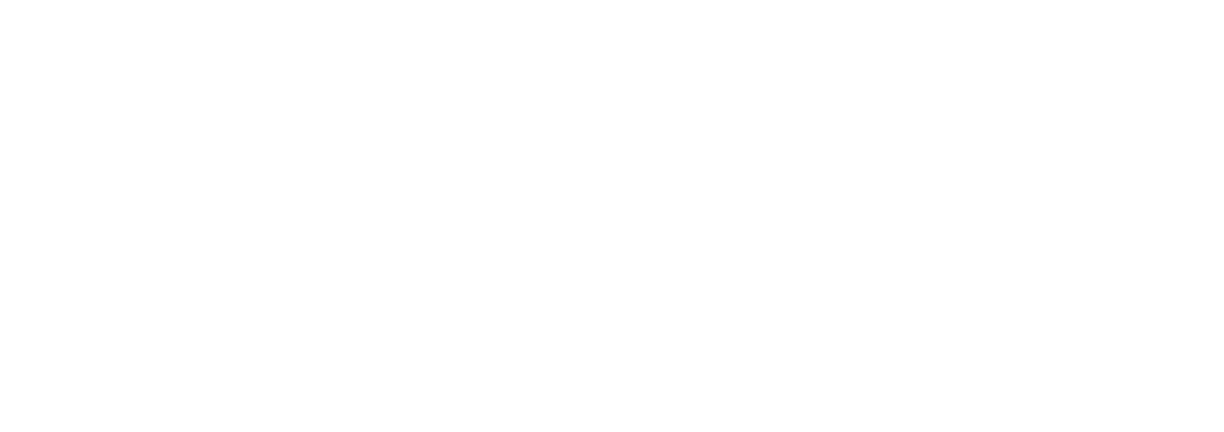