NPE Booth W5089
RAS First introduced about 20 years, this Fimic line of automatic, self-cleaning melt filters can handle any type of contamination. Each has a non-augur valve. As part of the process, two blades scrape the contamination collected by the filter. A scraper traps the contamination, then automatically discharges it via a front valve. Various modes adjust for the volume of material being processed. According to Fimic, about 530 filters are in operation worldwide.
What’s new? A bigger model, the 800mm — about 31.5-inch — RAS 800, available for delivery in May. It has 766 square inches of filtration surface, which is 30 percent more filtering surface than the next biggest size, the RAS 700. Filter screens can be created by punch or laser. The RAS 800 also has a new radial discharge valve, and the body is heavier. Two support arms have been added to raise and lower the lid.
Benefits A 40 percent increase in production, thanks to the RAS 800’s larger filtering surface. It is designed to operate without human intervention, according to Fimic. It can be used on a wide range of materials, including PP, LDPE, HDPE, PS, expanded polystyrene, ABS, PVC and PET. Overall, using the Fimic filters results in reduced quantity of waste and low maintenance costs.
Fimic srl, Carmignano di Brenta, Italy, 864-415-1639, www.fimic.it
Ron Shinn | Editor
Editor Ron Shinn is a co-founder of Plastics Machinery & Manufacturing and has been covering the plastics industry for more than 35 years. He leads the editorial team, directs coverage and sets the editorial calendar. He also writes features, including the Talking Points column and On the Factory Floor, and covers recycling and sustainability for PMM and Plastics Recycling.
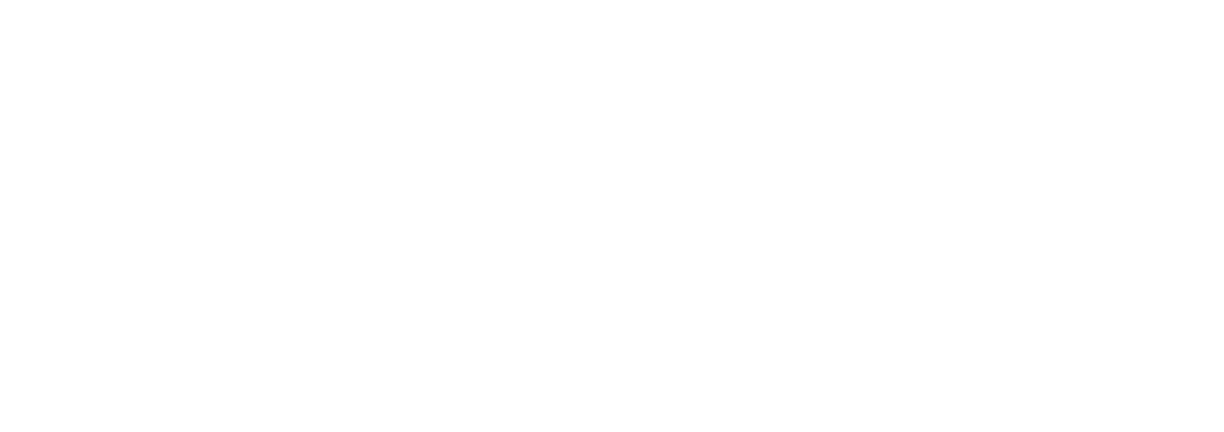