From the Fall 2023 issue of Plastics Recycling.
By Ron Shinn
The largest stand-alone bottle-to-bottle recycling plant in the Americas is now fully operational after an arduous journey from a greenfield site through a company bankruptcy then to machinery commissioning during the COVID-19 period.
The 270,000-square-foot plant in Reading, Pennsylvania, was built by CarbonLITE Holdings LLC, then acquired by DAK Americas LLC – now Alpek Polyester USA – for $96 million when CarbonLITE declared Chapter 11 bankruptcy. That happened just as the machinery commissioning process was in its early stages.
Plant construction started in 2019 and equipment commissioning started in early 2020, and the final production line got approval in March 2022. The process was delayed in large part because technicians from foreign machinery manufacturers could not travel during COVID travel restrictions, according to Rodrigo Castro Uribe, flake operations manager.
The facility is now producing bottle-grade recycled polyethylene terephthalate (rPET) from waste bottles collected mostly in New Yok City, Washington and Baltimore, Castro Uribe said. Most of the resin goes back to bottlers in the region, giving Alpek Polyester a key role in the area’s bottle-to-bottle circular network.
“Our mission is to promote that circularity,” says Ricky Lane, Alpek Polyester’s director of public affairs, trade relations and corporate communications. “The benefit that we do have is true circularity in bottle-to-bottle by those pellets going directly back into bottles.”
Castro Uribe says approximately 95 percent of the plant’s feedstock is post-consumer material.
Capacity is 60,000 tons of flake per year and 45,000 tons of pellets per year. Alpek Polyester would not provide the current output but says there is more capacity available when resin demand increases.
All flake now being produced goes into rPET pellets.
The facility is a model of efficiency. It can take in as much as 360 tons of post-consumer bottles per day through a single bottle line. At this step, bales are broken, initial separation between clear and color bottles takes place and the material goes through a grinder. The final product of the bottle line is prewashed flake.
In addition to two optical sorters, two robots with Max-AI from Bulk Handling Systems (BHS), Eugene, Ore., identify and pick out non-PET materials in the stream.
Next, the material goes through one of two Sorema wash lines with capacities of 185 tons per day for clear bottles and 53 tons per day for colored bottles and other by-products. Separation of other polymers in the stream continues during this step, and the flake is cleaned and sorted by two Tomra flake sorters.
The washing process involves six different steps, according to Castro Uribe. Adhesive and pieces of labels are removed, a flotation process takes out caps, and then the material is dried and sorted by size, and color contamination is removed.
The next step puts the clean flake through one of three Starlinger extruders with a capacity of 47 tons per day each. Each extrusion line is equipped with a Starlinger solid state polycondensation (SSP) reactor needed to produce food-grade material.
The extrusion step removes organic contaminants, pelletizes and crystallizes the material and increases intrinsic viscosity (IV). The final product of the extrusion phase is a food-grade pellet.
The SSPs, which are part of the extrusion step, raise the IV of the material back to acceptable levels for food-grade applications. IV is a measure of the polymers’ molecular weight and reflects the material’s melting point, crystallinity and tensile strength. It is used to determine the right grade of PET for a particular application.
The materials-handling system in the plant is from BHS.
The plant has six grinders manufactured by Sorema, Como, Italy.
Five silos store flake and pellets. All material shipped in or out of the plant is by dry truck or supersacks in dry trucks. Incoming material and finished product is stored inside the plant since there is no separate warehouse.
Alpek Polyester does not compound material, but the 100 percent-recycled-content rPET pellets can be compounded with Alpek Polyester virgin resin manufactured at other sites in customers' processes.
Since taking over, Alpek Polyster has needed to add only one flake sorter.
The facility was launched with electric power coming from three on-site diesel generators that can produce 3.6 megawatts, but a 69-kilovolt line to the plant is in the works, according to Todd Reilly, site director for the Reading facility.
The plant has 105 full-time employees and runs seven days a week with two 12-hour shifts. Employment has grown from 70 when Alpek Polyester took over in May 2021. All CarbonLITE employees were retained.
Feedstock comes primarily from material recovery centers (MRFs), but Castro Uribe says the facility is trying to work with municipalities that have deposit laws. “Most of the time, those are higher-quality bales,” he said.
The location of the plant gives it a strategic advantage.
Several major bottle manufacturers are in the vicinity of the Reading plant, which is 30 miles southwest of Allentown, Pennsylvania. Lane says Alpek Polyester is a leader in the production of virgin and recycled PET and has relationships with almost all of the major brands using those products. “We are the largest recycler in North America, as well as the largest PET producer, so that leadership position allows us to work with most of the major players,” he says.
Lane says Alpek Polyester expects demand for rPET to increase as laws mandating recycled content increase. “As more and more policy and legislation is put in place, there will be higher demand,” he said. “It will not be a demand caused by desire (to use recycled material), but by legislation. Those periods are coming soon.”
Lane continues: “It is very important all the process steps that we have to bring true circularity, and that’s what the brand houses and the customer relationships that we have are focused on so they can make their marketing claims that they are a circular producer.”
Alpek Polyester also has recycling operations in Richmond, Indiana, Fayetteville, North Carolina and Argentina. It is a subsidiary of Alpek S.A.B. de C.V., headquartered in Monterrey, Mexico. Alpek had revenue of $10.5 billion in its most recent fiscal year, with about 66 percent, or $6.9 billion, coming from the Alpek Polyester business. The company does not release U.S. sales figures.
Contact:
Alpek Polyester USA LLC, 704-940-7500, www.alpekpolyester.com
Ron Shinn | Editor
Editor Ron Shinn is a co-founder of Plastics Machinery & Manufacturing and has been covering the plastics industry for more than 35 years. He leads the editorial team, directs coverage and sets the editorial calendar. He also writes features, including the Talking Points column and On the Factory Floor, and covers recycling and sustainability for PMM and Plastics Recycling.
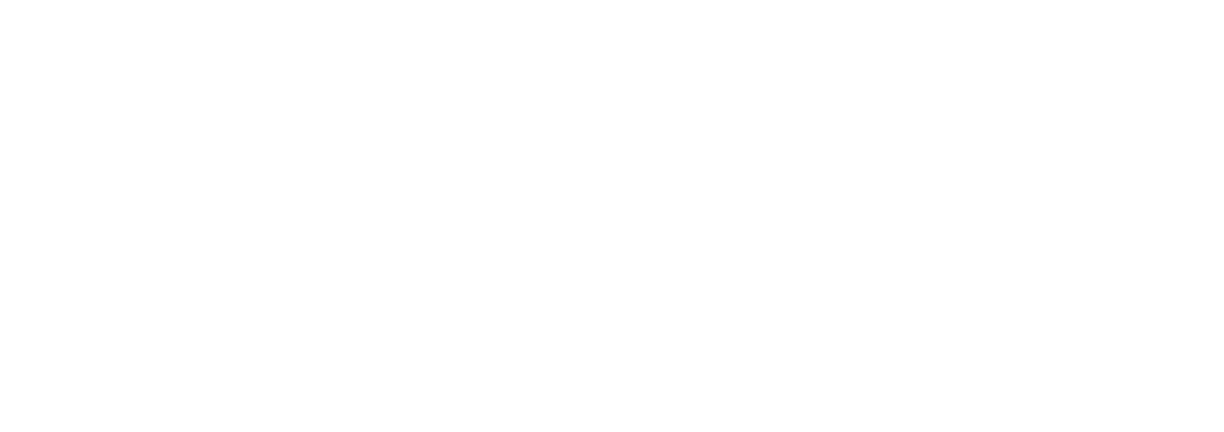