recoStar Starlinger’s recycling lines have been designed to handle all kinds of thermoplasts, including PE, PP and PET, in a variety of shapes and sizes, from fluffy film to hard-to-grind start-up lumps, to produce regranulate that’s fully usable for subsequent production.
What’s new? The recoStar PET. Starlinger’s newest line, it includes technologies for first-in-first-out (FIFO) pre-drying, pelletization, filtration, single-screw extrusion and FIFO solid-state polycondensation. It is designed for recycling used water bottles into recycled PET granulate that can be used to produce new bottles. Starlinger calls it a flake-to-pellet line, rather than an integrated flake to preform line. Five models are available, with footprint dimensions ranging from about 72 feet by 67 feet, to 115 feet to 105 feet, with hourly outputs ranging from 2,204 pounds to 9,259 pounds.
Benefits A savings in production costs of about 21 percent. Compared with the earlier version, the new lines use 25 percent less energy consumption, require 46 percent less maintenance time and achieve 15 percent higher production outputs. They also have a 21 percent smaller machine footprint.
American Starlinger-Sahm Inc., Fountain Inn, South Carolina, 864-297-1900, www.starlingersahm.com
Karen Hanna | Senior Staff Reporter
Senior Staff Reporter Karen Hanna covers injection molding, molds and tooling, processors, workforce and other topics, and writes features including In Other Words and Problem Solved for Plastics Machinery & Manufacturing, Plastics Recycling and The Journal of Blow Molding. She has more than 15 years of experience in daily and magazine journalism.
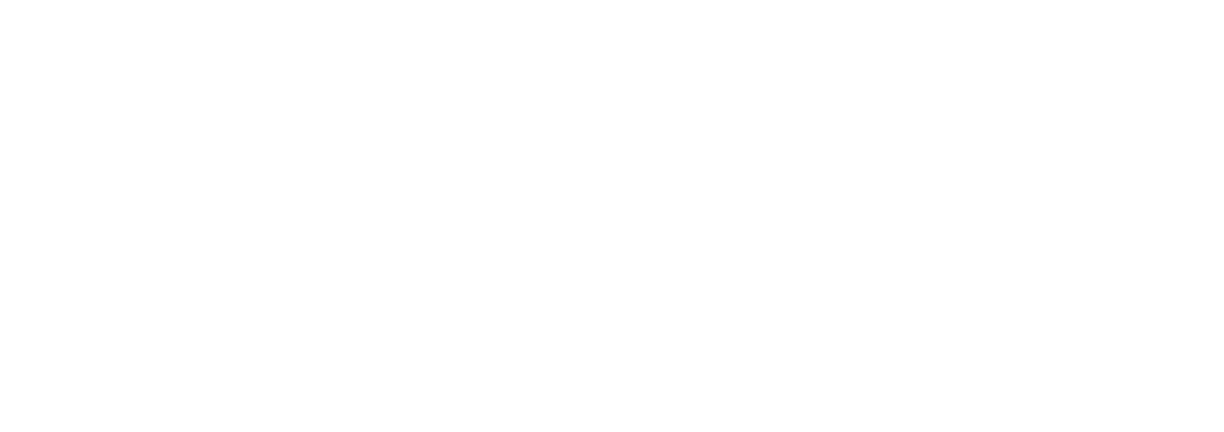