By Ron Shinn
All types and sizes of new plastics recycling machinery were evident at K 2022, from small shredders that can be placed next to a processing machine to collect trim all the way to complete recycling lines.
New technology allows processors to efficiently reuse more of their own scrap.
Here are some interesting new products.
Compact trim handling unit is for processors
Kongskilde Industries A/S demonstrated the all-in-one Compact Unit for handling trim waste.
The unit, shown for the first time at K 2022, is designed to be portable and can be used beside the machine that generates trim waste. It was named CompactTrim for the introduction, but the name was changed to Compact Unit afterwards because the original name was similar to another product.
“We are super-excited to showcase our brand-new, all-in-one unit for fast and efficient plastic trim removal,” said Kim Johnsen, chief commercial officer of Kongskilde Industries, based in Denmark. “It is flexible, smart and transportable. With its low noise level and small footprint, we expect many plastic foil producers to opt for this plug-and-play unit.”
The unit sucks in trim waste and compresses it for storage in a continuous bag. The user can adjust the suction level. There are no knives or rotors to replace, Kongskilde said.
The bag extends to almost 279 feet and an operator decides when to cut it and carry it away for storage or recycling. The bag can be cut while production is running.
A large silencer and internal filtration system mean the noise level is 79 decibels at about 3.3 feet from the unit.
There are built-in, easily accessible pre-filters and HEPA filters so the air can be recirculated. Processed air also can be piped away.
Kongskilde said anti-static equipment is not needed because of the unit’s fast air speed.
The trim handler is 7.2 feet long, 2.5 feet wide and 6.6 feet high. Weight is 1,433 pounds. Maximum power consumption is 3 kilowatts (KWh) per hour.
In addition to the Compact Unit, Kongskilde introduced the AirWash system to clean and convey regrind simultaneously. The patented design uses one blower to evacuate, convey and clean material while collecting fines, stringers and dust in a sealed drum.
The system uses air density to vacuum material, process it through a cyclone and then separate it for storage or recycling. It is typically used on material that comes out of granulators or mixers.
Kongskilde said it is suited for in-house recycling because after cleaning, the material can be used directly in the production line again. This means more production scrap can be reused.
AirWash can process PP, PET, PS, HDPE, linear low-density PE (LLDPE), LDPE, nylon, ABS and acrylics.
Lindner has a bigger Micromat HP shredder
Lindner showed the biggest model of its Micromat HP series of single-screw shredders for the first time at K 2022. The Micromat 2500 HP has a bigger motor, more knives and new features such as an automatic belt tensioning system to make it more efficient.
Two smaller Micromat shredders — the Micromat 1500 HP and Micromat 2000 HP — have been in production for several years. The model number refers to the approximate length of the rotor in millimeters. The Micromat 2500 HP has a rotor that is 2,525mm — 99.4 inches — long.
The new model uses a gearless, direct-belt drive. An adjustable safety clutch protects the shredder from items in the material stream that cannot be shredded. The 86-blade knife system also is adjustable. It has an automatic belt tensioning system that adjusts the belt to the correct starting point. This makes the shredder more efficient and reduces maintenance requirements.
Lindner said the new model has a higher throughput. It cited as an example the ability to produce 5 tons of recyclable bales per hour, rather than 3 tons.
It has a hopper opening of 10.8 feet by 7.9 feet. An internal pusher provides constant shredding. It has five screens.The inward-opening maintenance door is hydraulically operated.
The single motor uses 160 KWh.
Coperion and Herbold present complete PET line
Coperion GmbH, which acquired Herbold Meckesheim in September, presented itself as a turnkey provider by running a complete PET recycling line.
To integrate recycling products from the two businesses, Coperion established its Recycling Business Unit after the acquisition.
The centerpiece of the PET line running at the trade show was a high-performance ZSK 58 Mc18 twin-screw extruder with a 70mm-diameter screw.
Coperion used its SWB-300 Smart Weight Belt gravimetric feeder with an S100 single-screw pre-feeder plus the new ZS-B 70 Megafeed side feeder.
Melting, devolatilization and homogenization of the melt take place in the ZSK 58 Mc18 extruder. The material is then transferred by a gear pump and through a filter to an underwater pelletizer.
Pellets are condensed in the solid-state polycondensation reactor and then are ready to be processed again into bottles, fibers or films.
The company said its process eliminates the need for the PET to be pre-dried and flakes to be crystallized before they can be reprocessed. The PET recyclate can be fed directly into the ZSK extruder. The system costs less and needs less energy to operate, Coperion said.
Coperion said the U.S. Food and Drug Administration filed a letter of non-objection for the system to be used to make food-contact packaging.
Ron Shinn, editor
Contact:
Coperion Corp., Sewell, N.J., 856-256-3175, www.coperion.com
Ron Shinn | Editor
Editor Ron Shinn is a co-founder of Plastics Machinery & Manufacturing and has been covering the plastics industry for more than 35 years. He leads the editorial team, directs coverage and sets the editorial calendar. He also writes features, including the Talking Points column and On the Factory Floor, and covers recycling and sustainability for PMM and Plastics Recycling.
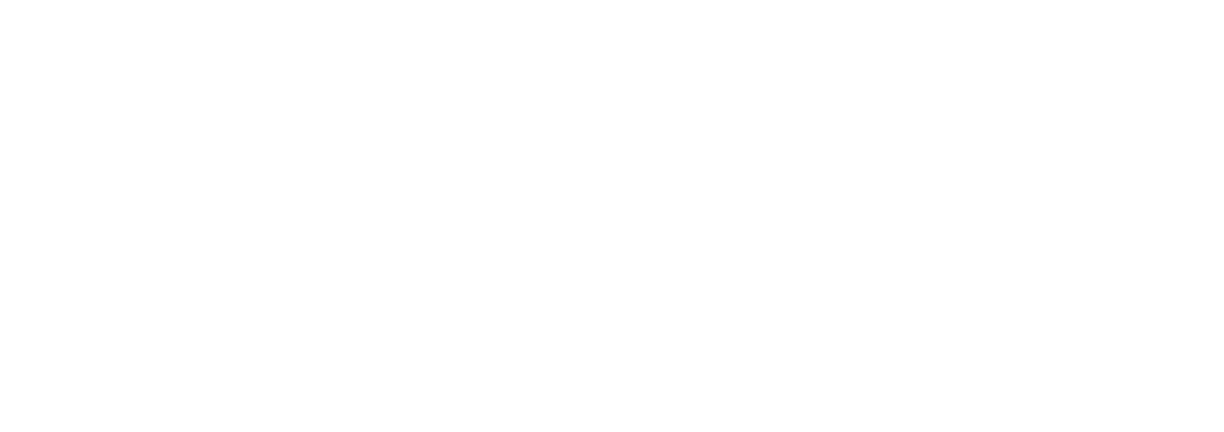