Chroma's carbon black alternative aids sorting of black plastics for recycling
This story appears in the Summer 2021 issue of Plastics Recycling. Read more from the issue.
Chroma Color recently introduced a carbon black alternative for producing black plastic products that are compatible with sorting equipment at materials recovery facilities (MRFs).
MRFs typically use near-infrared (NIR) sorting systems to mechanically separate recyclable plastics. The challenge with NIR technology is its inability to properly identify most black plastic products.
NIR sorters use light in a range between 760 nanometers (nm) and 2,500 nm that is invisible to humans but can identify different types of plastics depending on how light reflects off of them. The challenge is that carbon black, the most common type of black colorant used in plastics, absorbs light emitted from NIR devices and prevents the successful identification of plastics.
These unsorted products typically end up mixed in with trash hauled to landfills.
“Carbon black is a relatively inexpensive pigment,” said Hari Rajaraman, an R&D and marketing specialist with Chroma Color. “It’s safe. It’s available in different particle sizes. We can control the jetness and the undertone. So, most of the products that are black are colored using carbon black, but the problem with carbon black is it absorbs IR, and in a recycling process, the technology uses NIR sorters.”
Increasingly, consumer goods companies are looking for other options as they adopt aggressive sustainability goals that require a “quantum leap” in the recyclability of their plastic packaging, according to Chroma Color. Instead of sacrificing packaging aesthetics, they are looking for ways to produce black packaging that is compatible with recycling technology.
Chroma Color’s NIR-sortable black concentrates allow MRF sorters to accurately and repeatedly identify and sort plastic articles, the company said. The concentrates are based upon IR-reflecting/transparent pigments and a proprietary combination of dyes and organic pigments.
The solid concentrate masterbatches, are available in a variety of resins, including the most common packaging resins: ABS, PET, PE, PP and PS. The colorant is non-migratory, meaning it does not transfer from the package to the contents, is heat stable and FDA-approved, the company said.
Chroma Color also recently launched the ChromaPCRPET colorant line for recycled PET.
ChromaPCRPET allows brand owners to increase the amount of post-consumer resin (PCR) in their packaging. It is a solid concentrate masterbatch that uses a 100 percent post-consumer PET carrier. ChromaPCRPET can be used to produce PET sheet, bottles and other products. It is FDA-compliant with a no objection letter, the company said.
It’s becoming increasingly important to companies that they can state they use 100 percent PCR in their packaging, Rajaraman said.
“In many cases, the resin that’s currently used in the color concentrate is a virgin resin,” Rajaraman said. So, the end user cannot claim that the bottle or the cap is 100 percent PCR, and there is an increasing demand to address that. To address it, we have launched a product in PET that uses a PCR carrier, so that when a customer uses our color concentrate, they can claim the packaging is made of 100 percent PCR.”
The company also is developing similar PCR products for PE and PP, he said.
Contact information:
Chroma Color Corp., McHenry, Illinois, 815-385-8100, https://www.chromacolors.com/
Bruce Geiselman
Senior Staff Reporter Bruce Geiselman covers extrusion, blow molding, additive manufacturing, automation and end markets including automotive and packaging. He also writes features, including In Other Words and Problem Solved, for Plastics Machinery & Manufacturing, Plastics Recycling and The Journal of Blow Molding. He has extensive experience in daily and magazine journalism.
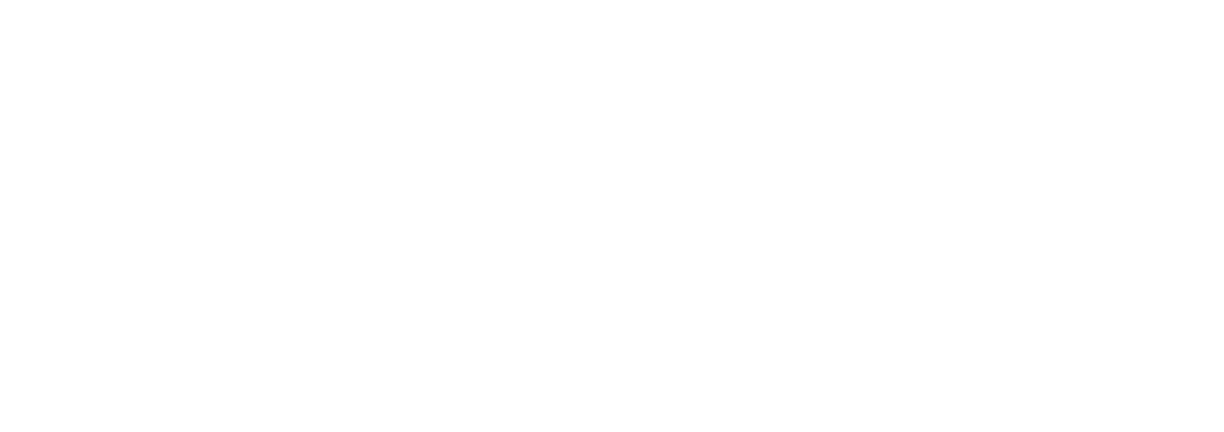