By Karen Hanna
A 3-D printer OEM established in the hope of helping would-be entrepreneurs and manufacturers overcome financial and geographical barriers is finding solutions using waste.
With a portfolio of large-format 3-D printers, some for less than the cost of a car, re:3D offers the opportunity for businesses and budding entrepreneurs to create big parts at low cost, using just the waste around them.
“For us, our testbed for that is the territory of Puerto Rico in the U.S., because their landfills are closing in one to two years and 80-plus percent — the statistics vary — of their goods are imported, and more importantly, they have a lot of manufacturing on the island,” company co-founder Samantha Snabes, said. “So, there’s just a really great opportunity to learn from the workforce that’s fluent in manufacturing, and to partner with manufacturers to think about more sustainable ways to use their scrap and waste.”
Along with Fiedler, Snabes, who’s based on the island, once worked for a contractor in spaceflight science at the NASA Johnson Space Center in Houston. Now, they and a team of other co-foundersRe:3D supplies two technologies: fused-filament-fabrication 3-D printers, which process filament at temperatures of up to 608 degrees Fahrenheit; and fused-granular-fabrication (FGF) 3-D printers, which process pellets, flake and granules at temperatures of up to 518 degrees. Depending on the model, build sizes max out in one dimension at 6 feet; the company also can supply printers with custom specs.
A number of the re:3D printers — including the Gigabot X, Gigabot X XLT, Terabot X and Exabot X — can print with waste plastics. As long as the materials have been sorted, cleaned and chopped to diameters no bigger than 5mm, a variety of material types, including PET, ABS, PC and polylactic acid, are acceptable. The company works with partners, including Canon Virginia Inc. (CVI) to obtain and test various resins and sources of recyclate.
In starting the company, Snabes and Fielder envisioned manufacturing durable essentials — like toilets, water buckets and couplings for plumbing in areas still developing infrastructure, or replacing it after a disaster — using printers priced within the grasp of individuals around the globe.
But, the partners said, the reality has proved so much more expansive.
A former Iowa farm boy now based in Houston, Fiedler ticked off some of the other ways he has seen users enlist the aid of the 3-D printers.
“It could be a manufacturing facility in Iowa that is using it to create welding fixtures for the components of the truck bodies that they’re assembling. It could be the university that’s using it in their ... research laboratory to do material compounding and mixing and 3-D printing these test specimens so they can put them in their tensile-testing machine and look at material properties from an educational and research perspective,” he said.
He recalled a trip to Puerto Rico in 2017, the year two massive hurricanes smashed the island. In one case, farmers used a re:3-D printer to create a more comfortable pouch for collecting coffee beans.
Pandemic demonstrated the need
For Snabes, the pandemic’s constriction of the supply chain demonstrated the urgency of being able to work onsite. With a 3-D printer, manufacturers and makers can carry on unhindered.
“A recent market has been Southeast Asia and looking where this technology can really shine — even with COVID — is in island nations, whether it’s the territory of Puerto Rico or islands of Southeast Asia or even the country of Japan or the country of New Zealand or Australia, or anywhere that’s dependent on resources right now, especially during COVID, within their own borders that recognizes that it may be a long time before things go back to pre-pandemic,” Snabes said. “So, they see this as an opportunity to build some other local infrastructure using local resources.”
Having access to a printer lubricates the supply chain, but access to material is just as important.
The company’s experience trying to print recycled materials has brought home the challenges of dealing with different waste streams. To address the difficulties, it might become more involved further upstream.
It currently is developing a granulator that works with its printers and chops material to diameters ranging from 1mm to 5mm.
Testing is ongoing at re:3D, which shares results of its material studies within the open-source community.
“How do we make sure that we’re sorting the plastic and that it’s clean enough and that it’s dry enough, the granules are the right size?” Fiedler asked. “There’s a lot of steps in that process that we’ve had to go through in trial and error and research, and to see, ‘OK, what really works and what doesn’t work?’ ”
As part of the learning process, re:3D partners with materials suppliers, including CVI, which provides pellets it produces from recycling its toner cartridges.
Rhonda Bunn, the senior director of human resources and corporate communications for CVI, praised re:3D’s work.
“They make a variety of products from furniture to frames to sinks, and they’re all made out of recycled plastics. It’s really, really cool. And they have done some great things ... 3-D printed some benches for Habitat for Humanity, for example,” she said. “Right now, it’s a very early collaboration, and we’re excited to see where that partnership or that relationship goes.”
Printers' possibilities are still developing
The former contractors for NASA said they’re still charting the possibilities, guided by the ingenuity of their printers’ users.
For some users, the printers are a tool toward independence and economic empowerment, Snabes said.
“We have a customer in Kenya that basically is using it to start and scale their business doing small manufacturing locally to reduce the dependence on imported goods,” she said.
Hospitals, small- to medium-sized manufacturers, hobbyists and schools all have found applications, Snabes said. In one example, printers are deployed to make molds to create building facades out of concrete.
For every 100 printers it sells, Snabes said, the company donates one machine to someone trying to make a difference in their community. First to receive a donation was a user in the Kibera slum, the biggest in Nairobi, Kenya. That printer is used for training purposes.
With printers available that can transform waste into parts, re:3D has found a way around the bigger expenses users typically encounter trying to source filament.
Re:3D’s executives believe the sky’s the limit.
“When you think about the ability to leverage all the advantages of pellet-price flake printing, it's allowing you to print really big objects that maybe otherwise would just not be feasible with other solutions,” Snabes said. “So, now we even have solicitations and work with partners, potential partners, federal agencies and companies to make a container bot, which is a [shipping] container-size version of the printer.”
Karen Hanna, senior staff reporter
Contact:
Re:3D, Houston, 512-730-0033, https://re3d.org
Vital Statistics
Printer | Build volume (feet) | Price |
Exabot X | 2.5 by 2.5 by 5.3 | $80,000 |
Terabot X | 2.9 by 3 by 2.8 | $48,500 |
Gigabot X XLT | 1.9 by 2.4 by 2.5 | $22,000 |
Gigabot X | 1.9 by 2 by 1.5 | $16,950 |
Karen Hanna | Senior Staff Reporter
Senior Staff Reporter Karen Hanna covers injection molding, molds and tooling, processors, workforce and other topics, and writes features including In Other Words and Problem Solved for Plastics Machinery & Manufacturing, Plastics Recycling and The Journal of Blow Molding. She has more than 15 years of experience in daily and magazine journalism.
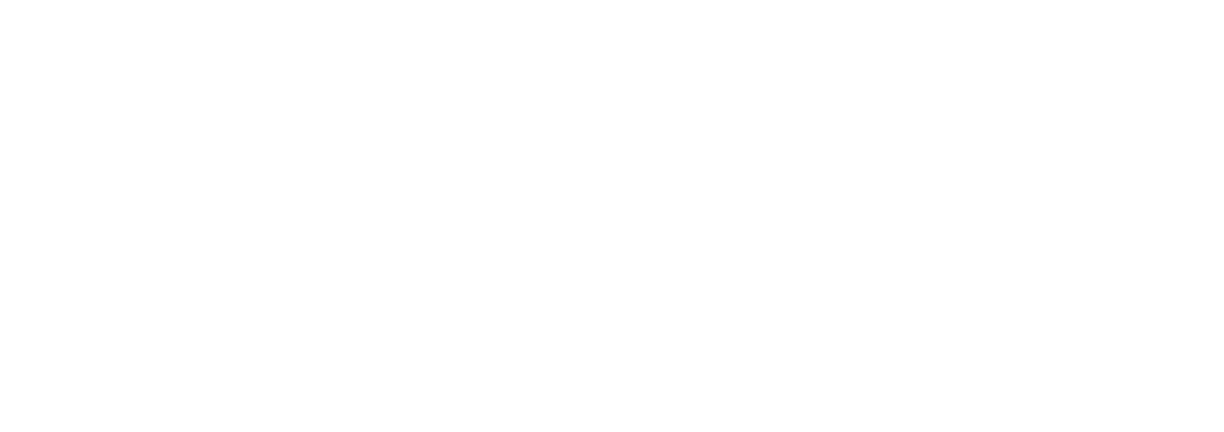