This story appeared in the Summer 2020 edition of Plastics Recycling magazine.
Big bag recycling line Starlinger has developed a process for the production and recycling of flexible intermediate bulk containers, known as big bags, used in the shipment of free-flowing materials. The process starts with a proprietary, mono-material PP bag, designed by Starlinger especially for recycling. Starlinger's production and recycling process comprises tape extrusion lines, winding machines, circular looms, coating lines and recycling lines. The lines include a special configuration of Starlinger’s recoStar dynamic equipped with two filtration systems to eliminate higher levels of contamination.
What’s new? The possibility of producing and recycling big bags in a closed-loop system. According to Starlinger, the lines are the first to provide a circular-economy solution to the problem of the waste created by big bags, which have been treated as a single-use product.
Benefits The reuse of a product that’s typically been regarded as disposable. Normally, big bags are made of multiple materials and feature designs or printing that complicate recycling. They have been difficult to recycle because they come in a variety of forms: with or without a PE liner; coated or uncoated; and with loops and seams consisting of different kinds of plastic. According to Starlinger, about 380 million four-loop big bags are sold each year; about three-quarters of big bags are used only once, before being incinerated or sent to a landfill. Using Starlinger’s bag design, process and lines, manufacturers can produce big bags with recycled PP content of up to 50 percent.
American Starlinger-Sahm Inc., Fountain Inn, S.C., 864-297-1900, www.starlingersahm.com
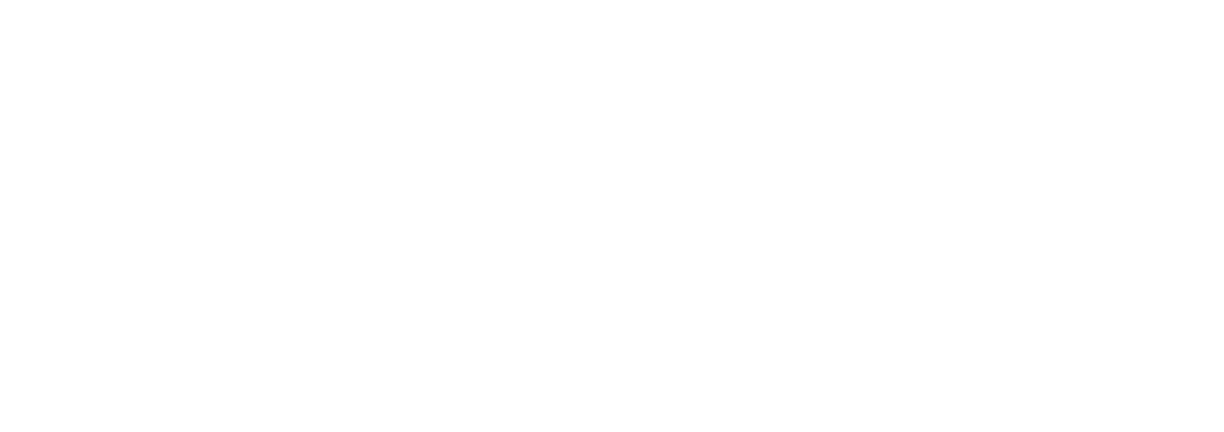