By Allan Gerlat
Makers of size-reduction equipment and other machinery used to process scrap are continually tweaking their product offerings to meet the evolving needs of their customers, whether those customers are processing post-industrial or post-consumer materials.
Vecoplan
Vecoplan recently launched its VIZ line of single-stage shredders, all-around machines that can be adapted to process a wide range of materials. “This machine can run absolutely anything,” he said.
At K 2019, Germany-based Vecoplan showed the VIZ 1300, which has an infeed opening of 4.1 feet wide by 6.1 feet high. The VIZ 1700 has an infeed opening of 5.5 feet by 6.1 feet.
VIZ-series shredders have a new rotor design that uses bolted tool-holder plates with variable cutting-tip sizes. The rotor does not have to be removed to change plates. This means that the cutting geometry can be easily changed with the rotor remaining in the shredder. Also, if a tool holder is damaged, it can be replaced without welding or removing the rotor.
“So, if you want to be running 23mm cap cutters one day, and you want to be running 60mm cram cutters the next, you’re just removing segments in the rotor,” Darley said. “And now, you’ve got a rotor that is purposed for a completely different application, just by changing out rotor segments.”
The rotor on the VIZ 1300 is 1.6 feet in diameter by 4.1 feet long. The VIZ 1700 rotor is 1.6 feet in diameter by 5.5 feet long. The rotor speed is 105 rpm to 265 rpm on the VIZ 1300 and 110 rpm to 280 rpm on the VIZ 1700. Three rotor configurations are available for each machine.
Users can choose between two drives: The HiTorc drive, which offers extra start-up power and high torque; and the ESC, a frequency-controlled, belt-driven direct drive.
The greater ram height and larger cutting chamber, compared to prior models, allow the VIZ to handle entire bales. The shredder also has a robust, swing-away screen that can easily be changed. Users can adjust the size of the output material by using screens with different hole sizes. VIZ shredders also can be equipped with a second counter knife.
“It’s kind of a one shredder fits all,” Darley said.
Rapid Granulator
“What we’ve done with this new machine is we’ve given the user the ability to control the rotor speed,” he said. “Slower rotor speeds are more desirable for the more rigid materials. Softer resins have a need to be cut. They can’t just be pulled apart or broken like the more brittle materials.”
Rapid Granulator’s FlexiSpeed system uses a frequency converter to let the user adjust the speed based on the material. By providing a range of speeds, the low-speed granulator is more versatile and can handle a wider range of materials.
Running at 15 rpm, the OneCut Pro improves the quality of ground brittle materials and minimizes dust. The noise level is reduced by 3 dBa to 5 dBa, when the rotor speed is reduced from 25 rpm to 15 rpm, Rapid said. DBa, or A-weighted decibels, measure how loudly sounds are perceived by the human ear.
The company said reducing the speed by 40 percent results in an energy savings of about 30 percent. The speed can be increased to 35 rpm to boost throughput.
Typically, low-speed granulators can be difficult to clean. The design of the OneCut Pro allows the operator to separate the motor from the rotor without tools. “It’s something you’ve never been able to do before with a screenless granulator, or a low-speed granulator,” Hoffman said.
In general, the open-hearted design of the company’s machines allows users to quickly and easily open them to maximize uptime. “As long as you can get in there quickly, things like knife-setting jigs and fixtures are really key to keeping that machine operating at its peak.”
The OneCut Pro comes in three models, the 100-22, 100-33 and 100-44.
The standard motor is 2.2 horsepower (hp); a 3-hp model also is available.
An optional hopper-mounted metal-detection accessory is available that stops the rotors before metal reaches the cutting chamber.
Maguire Products
The focal point of Maguire Products’ offerings for recycling is its purging recovery system, the PRS-20, which is a two-stage granulator, said Frank Kavanagh, VP of global sales and marketing for the company.
During the first stage, the operator fills a chamber with purging lumps. The chamber moves back and forth over a high-speed rotary blade, which shears an inch of plastic off the bottom of the lumps. The smaller chips then travel to a second-stage radial granulator underneath, which further size-reduces them. Then, a blower moves the material into a gaylord for collection and reuse.
Size-reduction machines aren’t the only auxiliary equipment with a role to play in recycling; Maguire’s new WSB-1200 series of weigh-scale blenders can handle multiple types of regrind and post-consumer resins, as well as virgin resin. The blenders can be used as part of injection molding, blow molding and extrusion processes.
The blender addresses a growing need, as processors increasingly use multiple materials. “It can still dispense up to 12 ingredients, but it offers expanded capacity for the additional recycled content, as well as the virgin production,” Kavanagh said.
He said the blender comes in seven sizes that can be configured in 120 ways, to meet a wide range of requirements.
Wittmann Battenfeld
Wittmann Battenfeld’s new beside-the-press G-Max 9 granulator is targeted at injection molding machines with up to 100 tons of clamping force. It is designed to process scrap that is fed directly back to the molding machine.
The G-Max 9 can handle material throughputs of up to 44 pounds per hour, depending on the shape, type and quality of material.
The technology is “an economical solution to create the granulator that exactly fits to application needs and can be modified in the field,” said Denis Metral, international granulator sales manager.
The granulator has three options for the height of the material hopper. A hopper with a feeding height of 25 inches can be used below a chute connected to the injection press. The granulator is fed directly from the machine.
A hopper with a feeding height of 34 inches is suited for use below a conveyor belt or drum separator. The standard hopper, which has a feeding height of 45 inches, is for use beside the press in conjunction with a sprue picker or robot.
The hoppers feature sound-dampening material sandwiched between two sheets of stainless steel. The granulator’s cutting rotor has a 7-inch diameter and comes with staggered three-by-three blades. The cutting chamber is 5.11 inches by 7.87 inches and the motor output is about 3 hp.
An automatic belt-tensioning system is standard.
The G-Max 9 is electrically interlocked with the injection molding machine so that it operates only when the top opening of the hopper is underneath a safety cover. Additionally, an optional electrical interface stops the granulator when the press is turned off.
A tilting material hopper and swing-down screen cradle facilitate cleaning and servicing.
Allan Gerlat, correspondent
For more information
Maguire Products Inc., Aston, Pa., 610-459-4300, www.maguire.com
Rapid Granulator Inc., Leetsdale, Pa., 724-584-5220, www.rapidgranulator.com
Vecoplan LLC, High Point, N.C., 336-252-4066, www.vecoplanllc.com
Wittmann Battenfeld Inc., Torrington, Conn., 860-496-9603, www.wittmann-group.com
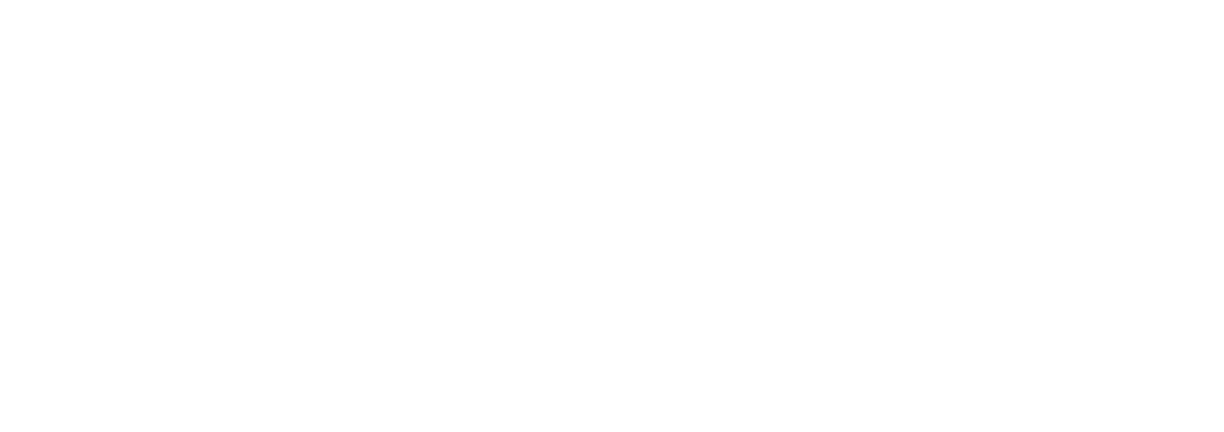