Robots are increasingly finding applications in recycling operations. The machines don't experience the fatigue and focus problems that humans do while sorting through materials, so they can perform significantly more efficiently.
AMP Robotics
AMP Robotics' Cortex robotic sortation system now is commercially available for plastics applications after the launch of a pilot program at a material recovery facility (MRF) earlier this year.
The pilot program, at Alpine Waste & Recycling's Altogether MRF in Denver, focused on cartons, but AMP also has tested the system's ability to sort plastics, said Matanya Horowitz, founder of AMP.
"We've already tested the system doing No. 1 plastics, both clear and green-colored PET," he said. "And we've also tested the system doing QC [quality control] lines with plastics materials as well," Horowitz said. "I think what's very powerful about the system we've created is that it learns from everything that it sees, using nothing but a plain, color camera. We trained our system with millions of examples of bottles and cans and everything else to understand the No. 1 plastics, No. 2 plastics, colored HDPE, other generic fiber products, and it's been able to distinguish all of these."
The AMP system relies on color sensors rather than infrared sensors. "We're able to hit very aggressive price points because we don't need these more expensive (infrared) sensors," Horowitz said.
The robot fits inside a safety cage, which has a camera attached to it. The camera looks at the material as it enters the cage, and the robot picks the material and deposits it in a designated spot, such as a bin next to the belt, Horowitz said. The robot can easily be programmed for particular materials; for sorting plastics, it features a special gripper and specific parameters for the vision system.
The robot itself looks like a spider and hangs from the top of the enclosure, over the conveyor belt. It reaches down and uses a suction system to grab material. It moves within a diameter of 5.2 feet.
"And we also put these enclosures on these existing lines where people might be working in front of or behind the robot, so it's really designed so you can fit it on those existing lines, have people work side by side with it," he said. "It expects that. It's totally safe."
AMP estimates humans average 40 picks a minute, while robots can handle between 55 and 80 picks a minute. And they can maintain that pace 24/7.
The robots have a picking accuracy of more than 90 percent, sometimes significantly higher, depending on the specifics of the facility, Horo-witz said. And the nature of the software is that the robots are continually learning.
"We can be very specific about what the robots select," Horowitz said. "We can be more specific than No. 1 plastics. We can say, that is a Pepsi bottle, that is a Coke bottle, or if it's some sort of brand-specific material, then maybe it might have an exterior material of one type but an interior material of another. So, if you have a multilayer piece of packaging, you want that separated out, we can do that."
A company investing in a robotic system generally sees a return on its investment within two years, he said. AMP also leases the Cortex system for a monthly fee that includes a hardware warranty and software updates. For most facilities, the monthly operating fee will be less than the labor costs that the system offsets, Horowitz said. "In many ways, you can see us as less of an equipment vendor and more of your favorite temp agency," he said.
Bulk Handling Systems
Recycling equipment maker Bulk Handling Systems (BHS) has launched a sorting system powered by artificial intelligence. The system, called Autonomous Quality
Control (AQC), includes a sorting robot that has brains and a vision system that are known as Max-AI.
"Max-AI technology opens the door for many applications. The robotic sorter is a tool to act on the artificial intelligence — eventually, we could use different tools," said
Peter Raschio, marketing manager for BHS. As many as two robotic sorters can use one vision system, and the artificial intelligence enables the robots to identify and properly handle particular materials.
Max-AI can identify dozens of materials and differentiate between similar materials, such as PET trays and bottles, Raschio said.
"Max can identify and separate colored PET, PET thermoforms, aluminum, mixed plastics, paper and even residue, leaving clear PET bottles," Raschio said. "The limitation is the reach and number of chutes we include — we can pick up to six separate types of items with each AQC based on the available space."
GreenWaste Recovery, a privately owned company that operates a MRF in San Jose, began using five AQC units, along with other new technologies, in June. CEO Frank Weigel predicts the systems, which operate on last-chance residue lines, will improve recovery of plastics, metals and paper.
"The new technology is exciting for our team and our stakeholders," he said. "We'll be able to increase our diversion rates while adding the necessary capacity to accept more material."
According to BHS, Max-AI can prioritize picks based on market conditions or the operator's discretion. It can even create products based on a recipe. "In the material recovery facility or plastics-recovery facility worlds, Max will make possible an autonomous system that will dynamically optimize itself and operate continuously," Raschio said.
Even without a robot, Max-AI has benefits, he said. The technology can be used to compile data to analyze performance at an existing MRF or to better design a new MRF.
"We show Max hundreds of thousands of images of objects, and we classify those images with their actual identification," Raschio said. "We give Max the answer, and time and time again, Max discovers the best path to take through the neural network to reach the correct answer on its own. Through all of this training, Max becomes capable of recognizing new images, correctly classifying objects never seen before."
Robotic sorting has existed for some time, Raschio said, but primarily to make predictable movements with predictable materials. But technology like Max-AI opens new possibilities.
"Our vision is a completely autonomous processing facility with Max-AI vision systems throughout. Max will monitor the material compositions in terms of the mix and volume in various locations and dynamically adjust parameters, like in-feed speed, conveyor speeds, screen angles, optical sorters, robotic sorters, baler settings, etc.," he said. "The challenge is to build the systems and logic to integrate Max throughout our equipment mix and system controls."
Plexus Recycling Technologies
A recycler of construction and demolition debris, Recon Services Inc., earlier this year became the first in the U.S. to install a robot from ZenRobotics, Helsinki, Finland, at a facility at its Del Valle, Texas, headquarters.
The robot is distributed by Plexus Recycling Technologies. Recon originally started using a ZRR2 and now also is using a ZRR1. The numbers reflect the number of arms. The two-arm system can make as many as 4,000 picks an hour, and each arm can pick out up to eight different materials. Due to its optical sensors, the system is able to distinguish between PVC, HDPE and PET.
Recon Services also now will purchase a Komptech 10300 ballistic separator to increase production and allow one line to concentrate on 3-D material such as rigid plastics and a second line to concentrate on 2-D material such as film, said Will Hancock, VP of operations for Plexus. The ZRR1 is being used on the 2-D line.
"We will also install a bunker system for the 3-D material that will allow Recon to operate 24 hours a day with only a small workforce needed during the day," Hancock said. "The robots will speak to the bunker during the night and run until the bunker is empty, and completely shut down after 10 minutes of operating without a pick made."
Plexus also will equip the front of the line with a static Electric Komptech 3400 shredder to size material for the entire operation. That will likely exceed 500 tons processed per day.
Hancock said one of the biggest advantages with robots is their reliability.
"With robots, you don't have any downtime, you don't have any holidays. There are no sick days. You are able to run 24/7, which allows you to increase your productivity, increase your profit."
The robotic presorting removes a significant number of contaminants from the stream, allowing downstream optical sorters to work more efficiently when the material goes past them, Hancock said.
"So, we're actually increasing the productivity of your optical sorters down the line because instead of your optical sorter having to separate all those different polymers, we're sending [cleaner] polymers to it," he said.
Allan Gerlat, correspondent
For more information
AMP Robotics,Denver, 720-470-0812, www.amprobotics.com
Bulk Handling Systems,Eugene, Ore., 541-485-0999, www.bulkhandlingsystems.com
Plexus Recycling Technologies,Westminster, Colo. 720-890-9090, www.plexusrecyclingtechnologies.com
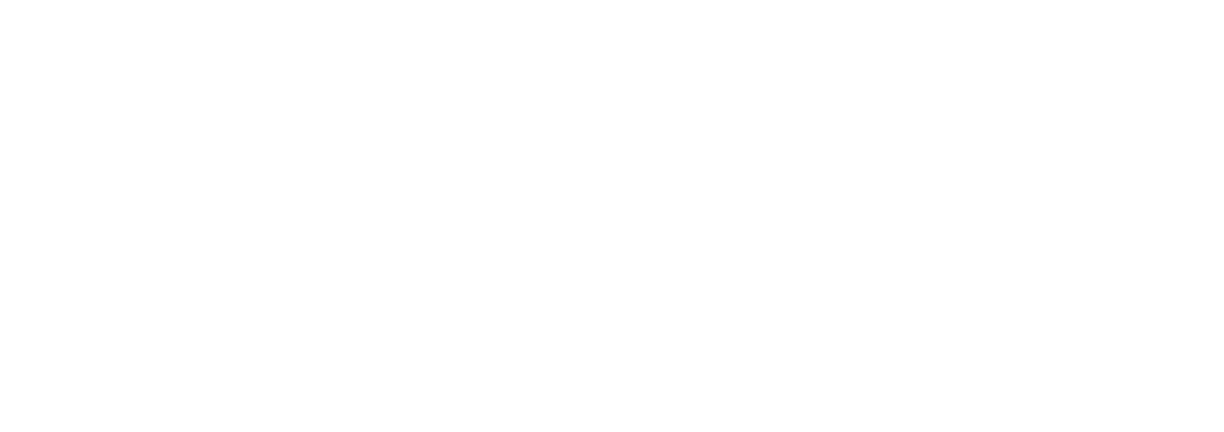