Tom Murdough is 77 and already has founded and sold two successful rotomolding companies — Little Tikes Co., Hudson, Ohio, and Step2 Co. LLC, Streetsboro, Ohio. But his love affair with rotational molding has spurred him to start a new company in Streetsboro — Simplay3 Co.
The products are similar to ones his earlier companies made — children's toys, and home and garden products, primarily. But now he's using rotomolding equipment from a manufacturer with whom he hasn't previously worked. Rotoline, which is based in Chapecó, Brazil, and assembles machinery in Kent, Ohio, has supplied three machines to Simplay3. They are the manufacturing focal point for Simplay3's 70,000-square-foot building in Streetsboro.
During a recent visit from Plastics Machinery Magazine, some employees fine-tuned equipment and performed testing. The smallest rotomolding machine will be used for prototyping, Murdough said.
Manufacturing began on a small scale in early November, but regulatory bottlenecks have slowed the production timetable. "It could be faster, but we're held up by so many roadblocks," he said. Those regulatory hurdles haven't had any effect from a machinery standpoint, but they do have influence in terms of other decisions. For example, each children's product has to be tested and approved by the Consumer Product Safety Commission, and the process can cost as much as $5,000 per test, with the company planning to undergo tests for 15-20 products a year.
Murdough pointed to the increase in regulation in comparing Simplay3 to his previous experiences. "It's vastly different than the start-up issues associated with Little Tikes and Step2," he said. "We expect it [the regulatory atmosphere] to be vastly different under the new [presidential] administration."
In beginning his latest project, Murdough, who retired from Step2 in 2007, said he had some difficulty finding the right building. What he found was a building that formerly housed a wine distributor. The facility, built in 1992, has 30-foot-high ceilings, five enclosed sliding doors, a truck door and eight other shipping doors. It has taken a lot of work to get it ready for production, plant manager Gabe Parsons said.
It offers plenty of possibilities — Simplay3 has the potential to expand another 65,000 square feet.
When production is fully underway, the floor will have a raw material and finished material area. Simplay3 also has added auxiliary equipment, including a grinder, granulator and mini-silo, Parsons said.
So far, Simplay3's products include child-sized cars, a wheelbarrow and a step stool. The company is selling the products only through its website at https://simplay3.com.
To make the products, the rotational molding machines use a carousel of four rotating arms. On the arms are mounted spiders, metal structures that hold the molds. Each one is unique to the product that's being made.
Simplay3 currently has three spiders. The company makes them in-house, buying the steel ring that forms each spider's skeleton and building from there. By the end of the year, Murdough hopes to have 25 or 30 spiders.
The molds within the spiders are made by various mold makers; Murdough declined to identify them.
Resin powder is introduced at a loading and demolding station. Once the resin is loaded, the mold goes into an oven, where it is heated to between 600 and 660 degrees Fahrenheit.
To cool the products once they come out of the oven, each rotomolding machine has three fans operating in a cooling chamber.
Initially, Simplay3 purchased its resin in powder form, but it has since added an R.E. Scheer pulverizer.
Murdough said that, going forward, the company will get its material in pellet form. The company also will blend material, so that it has a 10 percent regrind mix.
It uses blenders from Marion Process Solutions, Marion, Iowa; the company's batch mixers for plastic powders feature air-actuated doors and slide contour discharge valves. One key to the process is using finely powdered material with a size of 35 mesh.
Overall, Murdough said he plans for the company to perform most of its work in-house.
"We try to be vertically integrated as much as possible," Murdough said. "If we can do that internally — that's what we prefer."
Rotational molding is a process near to his heart. "I got fascinated with what you could do with rotational molding," said Murdough, who worked for Wonder Products Co., a maker of rotationally molded toys, as VP of marketing in the 1970s.
The advantage of rotomolding is that manufacturing is faster and more efficient than injection molding the kinds of products Simplay3 makes, Murdough said. The process works well for the company's product line, because rotational molding is good for larger and unusual shapes. Also, it can handle both big and little products.
"Typically, our products are more durable than those made by more conventional processes," he said.
Rotational molding doesn't employ the automation of injection molding or blow molding, because the resin is loaded manually. Murdough said making products with rotational molding requires labor costs comparable to other processes.
There are few rotational molding equipment suppliers, but that doesn't present any particular challenges for Simplay3, he said.
He has seen the evolution of rotational molding in his long career, including advancements in machines, materials and molds. Murdough said continual improvements have been made in the auxiliary equipment used in rotational molding. "It's important to stay abreast of what's happening on equipment," he said.
And he's not so concerned with brand loyalty. "What's more important is functionality."
Of rotomolding's evolution, what stands out, though, is the processing speed of the primary equipment.
"The ability to run fast, introduce new products in rapid succession, and the commitment of our people allows us to do what we do," Murdough said.
Allan Gerlat, correspondent
Contact:
Simplay3 Co., 866-855-0100, https://simplay3.com
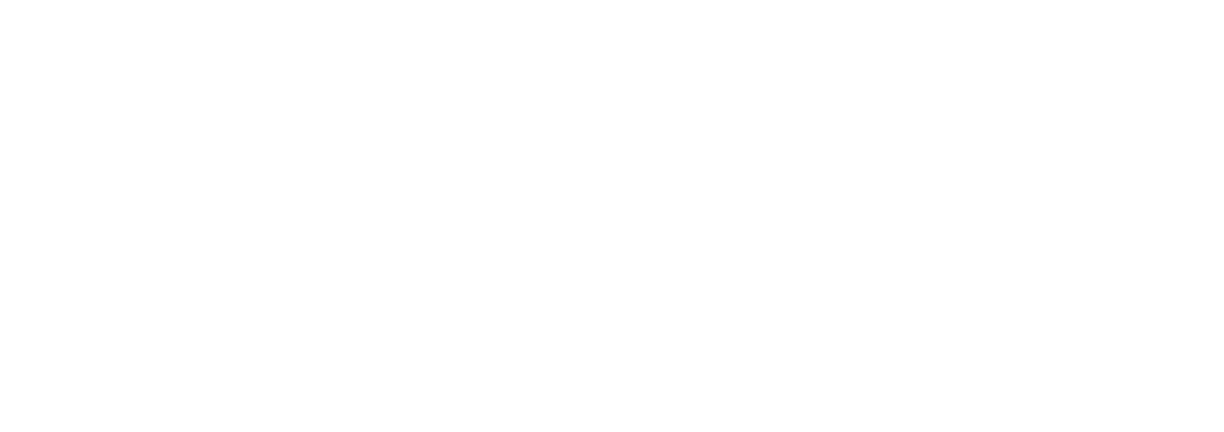