By Karen Hanna
The blood tube your phlebotomist reaches for when you’re getting your cholesterol checked could have problems of its own.
For example, it might not roll straight.
“Nobody really cares if the part is rolling down the table equally,” conceded Thomas Bechtel, global sales director for Mold-Masters' packaging and medical division. “But what is relevant is a part that is much more straight has significant downstream advantages. … The more straight your part is, the faster your labeling machine can be set up. And it’s not only the labeling, it’s basically any downstream [process].”
To address this problem, Mold-Masters has recently rolled out a hot-runner system designed to create blood tubes that are completely symmetrical — its new Symfill technology. The process can speed up cycle time, as well as downstream processing.
According to Bechtel, in conventional hot runner systems, the melt enters the nozzle from the manifold from one direction, passing around the valve pin. This causes the melt to fill one side of the tube more quickly than the opposite side. The valve pin restricts the flow and causes a “valve-pin-shadow” effect that’s similar to a tree blocking out the sun. While invisible to the naked eye, the tube can have uneven wall thicknesses, with the thicker side bowing inward.
“This valve-pin shadow effect, you don't see it, or you hardly see it, or if you see it, it's not really a big deal. It starts to become problematic for parts, such as a PET blood tube, because of the very aggressive L-over-T, and this very, very narrow and slim core. That's where you start to see you're reaching a natural barrier, or limit, with the conventional technology,” Bechtel said.
With conventional hot-runner systems, the difference in the wall thicknesses of the resulting blood tubes can be as much as 1.5mm from side to side.
To allow more even filling, Symfill systems allow the melt to flow through multiple inlets, so it isn’t split by the valve pin. They eventually could be used to produce a variety of long and narrow parts, such as pens, mascara applicators and needle shields.
“This allows the melt to flow at equal velocities and fill the part without any bias,” Bechtel said.
“And, so, basically we're hiding this valve-pin shadow. It's like if we if we stick to this tree-on-a-playing-field picture, instead of one sun, we're having multiple suns, like in a movie studio. So, this means the melt travels with an equal velocity along the nozzle, and the part is filled symmetrical … so the core remains straight.”
He explained that Symfill uses Mold-Masters' iFlow manifolds, rather than conventional manifolds. Unlike conventional manifolds, created by gun-drilling through single blocks of steel or other mold materials, iFlow manifolds feature carved channels. Mold-Masters makes them by digging out mirror-image channels on separate plates, then sandwiching the plates together.
Cross sections of the manifolds reveal very different melt paths: Conventional manifolds have channels that run in straight lines or at angles to each other, like the streets of Upper Manhattan, while iFlow manifolds can feature cul-de-sacs, roundabouts and turnarounds.
“We can mill those very, very fine details. We can be a lot more creative when it comes to how we deliver the melt to the nozzle than conventional hot-runner technology can ever be,” Bechtel said.
Symfill systems can be specified for a range of cavity configurations, though 48 or 96 cavities are typical for blood-tube production, he said.
The systems can limit wall-thickness deviation to within 0.15mm; in recent blood vial applications, the technology reduced barrel bow by up to 90 percent. They can do that extending pack-and-hold steps — the tack molders with conventional systems sometimes take to compensate for part bowing.
In all, cycle times can be as much as 2 seconds faster, Bechtel said.
The resulting tubes not only will roll better, they’ll avoid gumming up the works when it comes to downstream processing.
That will increase productivity — and cut the fat in downtime.
Karen Hanna, senior staff reporter
Contact:
Mold-Masters, Georgetown, Ontario, 905-877-0185, www.moldmasters.com
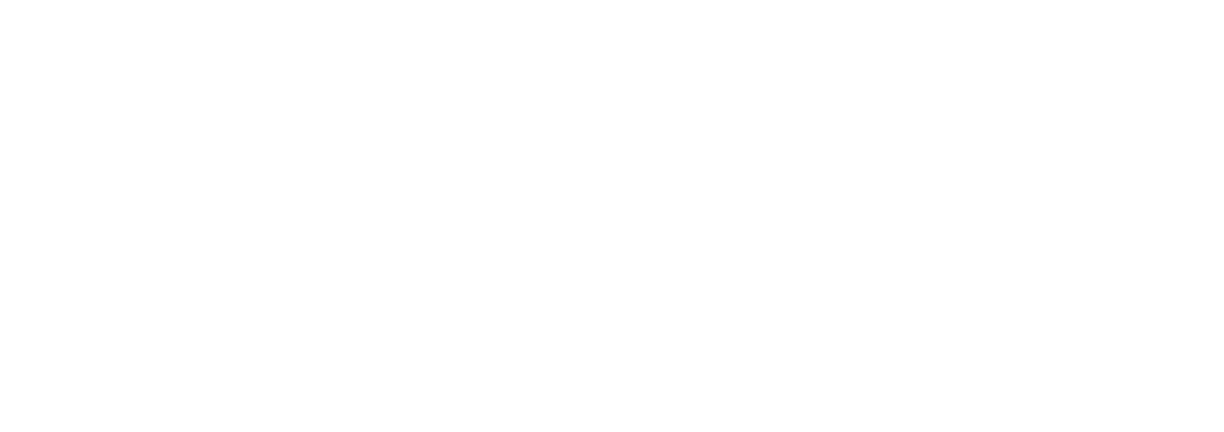