Servo-valve-gate system cuts chainsaw molding issues
Problem: The Stihl Inc. manufacturing plant in Virginia Beach, Va., was experiencing cosmetic issues with chainsaw handles it injection molds.
Solution: The company switched from a pneumatic valve gate to a servo-valve-gate system from HRSflow to gain more control over the molding process.
An increasing scrap rate due to cosmetic flaws forced the management team at Stihl to take another look at how the company was molding a curved chainsaw handle. To improve parting lines to meet Stihl’s standard, the part frequently required time-consuming trimming and sanding after it came out of the mold. The company also was experiencing excessive downtime to maintain valve gates.
Fixing the problem required an interesting collaboration between Stihl, hot-runner manufacturer HRSflow and mold maker Industrial Molds. “It required that we all work very closely together,” said Guido Feit, mold engineering manager at Stihl.
Related: On the Factory Floor at Stihl's Virginia plant
The handle is approximately 9 inches by 8.7 inches by 14.2 inches and is surprisingly light.
“We were using a pneumatic valve gate on the hot runner,” said Kevin Tombling, mold design engineer at Stihl. “It used timers to determine when to open and close. Historically, there were problems with not getting a lot of feedback if the position was either opened or closed.”
Stihl unsuccessfully tried different in-house solutions, including sequential valve gating, valve gates, cold runners and hot tips, to modify its older molds to improve the handle.
It eventually took the problem to Industrial Molds. The company specializes in building complicated molds, said Randy Hanson, director of engineering and account management at Industrial Molds.
“They asked us to build a tool,” Hanson said. “Stihl had a design for a tool that was similar, so we took a look and discussed the issues they were having.”
Hanson said Industrial Molds, which had never built a mold for Stihl, started by contacting several hot-tip suppliers and telling them exactly where they planned to install gates and air nozzles for gas assist. “We needed really precise control,” he said.
HRSflow told Industrial Molds and Stihl it had a system that might work. “We had never worked with them before we sat down and went through the design,” Hanson said. “We started running analysis with them, then started designing the mold. HRSflow was running flow analysis to show how this was going to work.”
Patrick Clark, sales account manager at HRSflow, said the problem with the pneumatic valve gates was that sometimes a valve pin was not closed all the way when the gas assist kicked in, which allowed the gas to back up into the manifold and cause a defect in the part.
Bob Harvey, sales director North America at HRSflow, recommended the FLEXflow Evo, a servo-valve-gate system that is designed for precise control.
The FLEXflow Evo system includes a control panel that picks up an injection signal from the molding machine so that it detects the actual injection position of the barrel. This provides visibility into the process that is not available with standard hot-runner systems.
“There is no modification to the molding machine for FLEXflow Evo,” Clark said. “We pick up a couple signals that are readily available so the integration cost for the molding machine is basically zero.”
Harvey said FLEXflow Evo is a game-changing technology. “Once a customer gets a chance to feel and experience the repeatability, visibility, control and clean operation, they want this. Compared with older technology, it is like the difference between the Jetsons and Flintstones.”
FLEXflow Evo represents the evolution of the FLEXflow servo-driven valve gate system. It is characterized by responsive software that simplifies the operator’s work and new optimized tips based on the type of polymer. The on-manifold actuators make FLEXflow Evo a compact solution ready to be installed on the mold, Harvey said.
Several hundred FLEXflow Evo systems are currently in use worldwide, Harvey estimated.
Industrial Molds’ Hanson said the FLEXflow Evo is designed “for something like a TV that has a long strip where you open a valve and open a valve and open another valve, and you can time the flow as it rolls through.
“There are a lot of things you can do, such as open the valves really slow or really fast, or open them only partially. There are a lot of really neat processing things you can do with this system.”
HRSflow said the controller provides accurate, easy-to-operate, flexible control of pressure and flow rate at each individual gate during the injection process.
The first tests of using the system to produce the handles took place at Industrial Molds, with personnel from HRSflow and Stihl on hand. “We got it all set up, and we shot it. It immediately worked really good,” Hanson said.
The project took six months.
Stihl currently has molds with the FLEXflow Evo servo-valve-gate systems making two different-sized chainsaw handles running on two 500-ton Engel presses. Scrap rates and maintenance downtime have been reduced significantly.
Feit said the parts look better, and Stihl is now considering the technology for molds for other products. “We are looking outside of that improvement to see what else we can do,” he said.
Ron Shinn, editor
Contact:
HRSflow, Byron Center, Mich., 616-228-6900, www.hrsflow.com
Industrial Molds Inc., Rockford, Ill., 815-397-2971, https://industrialmolds.com
Ron Shinn | Editor
Editor Ron Shinn is a co-founder of Plastics Machinery & Manufacturing and has been covering the plastics industry for more than 35 years. He leads the editorial team, directs coverage and sets the editorial calendar. He also writes features, including the Talking Points column and On the Factory Floor, and covers recycling and sustainability for PMM and Plastics Recycling.
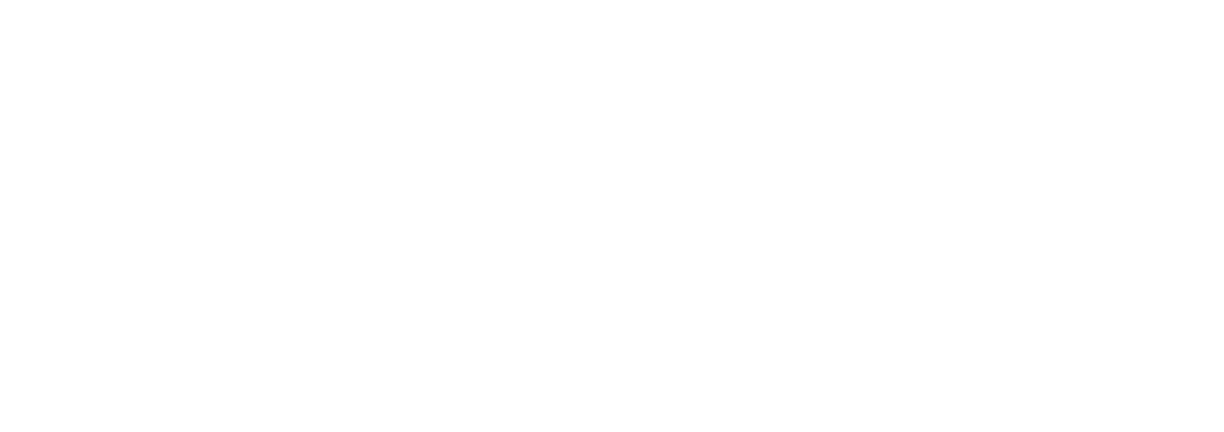