By Karen Hanna
Parts that eject from a molding machine every few seconds begin life as an idea, then a design.
To speed up the process from concept to reality, mold makers, along with part designers and engineers, turn to simulation packages, such as software from Altair, Autodesk and CGTech’s Vericut, which all have been recently updated. The packages can help them work together better, while reducing design time and optimizing the performance and manufacturability of the final designs.
“For the mold maker, a main benefit is knowing that even before the designer sends through his design, when the product is still under development, that the part can be manufactured. The injection molding simulation has shown it will fill, and any common problems with defects are resolved,” said Ken Welch, senior VP for Inspire Design and Manufacturing Solutions, Altair. “Once he or she knows the part can be produced, the design of the mold is key for cost reduction and part quality.”
Hanno Van Raalte, the product manager for Autodesk’s recently updated Fusion 360 subscription-software package, said his company’s latest offering can help users easily answer three questions vital in planning both the part and the mold: Will the part fill? Will I have sink marks and weld lines in aesthetically important areas? Will I have problems with excessive warpage?
“Simulation can, and should, be done early in the design process, so beneficial changes to the design, uncovered by the simulation, can be made before those changes might have an impact on downstream processes,” he said.
Making this process easier are several updated software offerings.
Altair Inspire Mold continues to evolve
Altair makes software that helps engineers and designers prepare parts for a number of processes, including stamping, extrusion, PU foaming, additive manufacturing and casting. These packages can be integrated with the company’s performance analysis products, including extensive material modeling and structural optimization solutions.
“Whether you are a designer looking to make, say, bottle caps or the front end of a car — it’s for you. Likewise, if you are an analyst and need to dive deeper, for example, into the structural performance of a large, complex-geometry part, then you can,” Welch said.
Launched in November 2020, Altair Inspire Mold has been regularly updated over about the past year, Welch said. New and upgraded features include a seamless interface for stress, strength and warpage analysis of fiber-reinforced and filled materials; with it, users can map fiber-orientation results at the click of a button.
In addition, with the software’s CAD-to-solution feature, Welch said, “users can set up the analysis on CAD parts, click one button, get the mesh, launch the solution and then post-process.”
He said Altair Inspire Mold can help accelerate the creation, optimization and analysis of parts and assemblies.
“By offering our unique integrated solution, the designer can check that, say, the part will fill. If not, make some changes and try again, no need to return to CAD. This is very fast — from seconds to minutes — and does not need analytical expertise because it is all geometry-based,” he said.
Autodesk integration supports non-molding specialists
Autodesk has integrated its simulation technology into Autodesk Fusion 360, a cloud-based subscription program for the entire design-to-make process.
Using technology from Autodesk Moldflow, the integration allows engineers who have less experience with injection molding to better understand the manufacturability of a plastic part, Hanno said.
Intended to streamline the process from design to manufacturing, Fusion 360 offers simulations that can help resolve part design issues that might later add huge costs to the project, Van Raalte said.
“New workflows enabled by Moldflow simulation being offered from within Fusion break down the isolation and disconnects that can tend to crop up between the highly specialized injection molding side of the house and the much more ‘connected’ CAD world, where efficient collaboration is the watchword,” he said.
By enabling more efficient collaboration, Fusion 360 can provide team members who are not well-versed in injection molding with insights into the designs being studied.
“The intent is to free up the time of expert analysts to work on more difficult challenges that require a great deal of expertise, where they add the greatest value,” Van Raalte said.
CGTech updates Vericut
“Mold and tooling makers are facing a greater push to be competitive and as productive as possible. They’re feeling the pressure to machine high-quality parts faster and on tighter timelines,” he said.
Now available as Version 9.2, the Vericut portfolio simulates traditional machining equipment, such as milling and turning centers, as well as additive machines, for the production of parts across a wide array of industries, including tool, die and mold making. It allows the makers of molds, tooling and screws to plan cutting paths and strategies, optimize automation, and prevent collisions between workpieces and workholding and cutting equipment.
A Vericut-enabled environment makes it easier for plastics processors to deliver high quality plastic parts in a shorter amount of time,” Vericut product manager Gene Granata. “Checking for collisions, gouges, and surface finishes prior to machining makes it easier to reduce lead times without sacrificing the quality of the part and reducing the amount of post-processingFeaturing improved cutting-tool support and faster collision checks, the software now can simulate material removal at tight cutting resolutions up to 30 percent faster. It also features a new 3DLive interface, which allows users to upload Geometry Description Markup Language files containing information about colors, CNC machines, fixture components and cutting toolholders.
The software draws upon an expanded database of materials and equipment. For example, users can specify among an extended array of component assemblies, such as robot end effectors, interchangeable machine heads, bolt-on rotary tables, and part/fixture setups.
The database now includes conical end mills, spherical end mills and new thread mills, allowing it to check for machining errors according to the specific tools’ capabilities and limitations. Information about stock materials available from Sandvik and Walter also has been added.
According to CGTech, Vericut makes it easier for plastics processors to deliver high quality plastic parts with shorter lead times and minimal post-processing.
“Vericut detects possible collisions and errors without putting their machines, materials, or tools at risk, preventing errors or miscalculations that could result in costly damages. The closer a simulation is to the real world, the easier it will be to predict what’s going to happen once a program reaches the shop floor,” Granata said.
Karen Hanna, senior staff reporter
Contact:
Altair Engineering, Troy, Mich., 248-614-2400, www.altair.com
Autodesk, San Rafael, Calif., 415-507-5000, www.autodesk.com
CGTech, Irvine, Calif., 949-753-1050, www.cgtech.com
Karen Hanna | Senior Staff Reporter
Senior Staff Reporter Karen Hanna covers injection molding, molds and tooling, processors, workforce and other topics, and writes features including In Other Words and Problem Solved for Plastics Machinery & Manufacturing, Plastics Recycling and The Journal of Blow Molding. She has more than 15 years of experience in daily and magazine journalism.
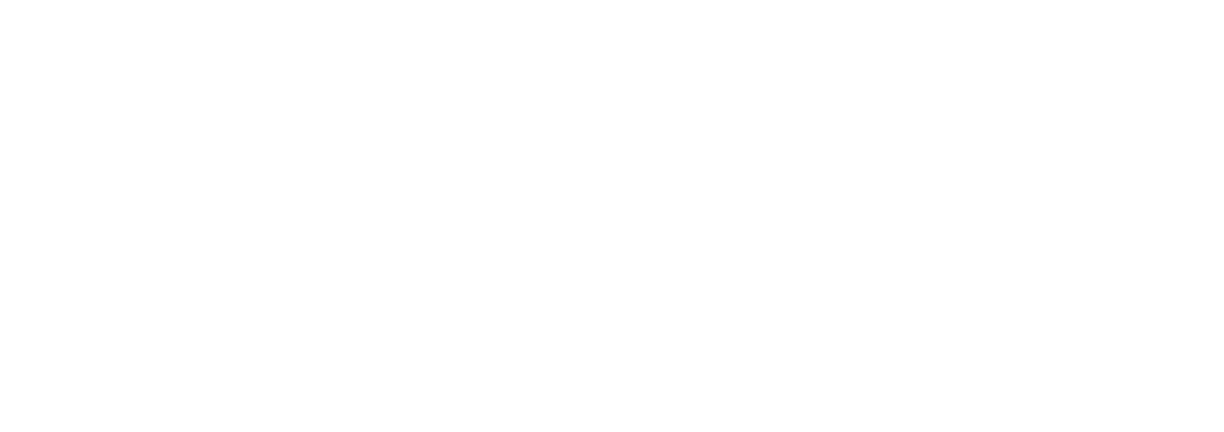