By Karen Hanna
A DME service to help injection molders prototype parts more quickly and with less expense is going full-scale.
Based on part designs submitted by molders, DME now can use a proprietary software program and components of its Master Unit Die (MUD) Quick-Change system to 3-D print mold cores and cavities for installation on its quick-change mold frames. The process takes only a few days, and molders can install or remove molds in minutes, allowing fast transitions between short runs and full production.
“If you have a molding machine, you can become a prototype house,” said Mike McCutcheon, a DME product manager.
Often, he said, molders rely on outside firms and traditional mold makers to produce prototypes. But this process — which includes designing molds, securing machine time and materials, and producing tooling — can take weeks. And it’s expensive, especially using conventional, all-metal molds.
“The current process of aluminum prototype molding is time-consuming and costly, especially if the plastic part is subject to multiple revisions in design, which in some cases requires starting the process over and purchasing new plates or inserts and more machine time,” McCutcheon said. By comparison, according to the company, DME’s rapid prototyping program can cut turnaround time by 90 percent and costs by 70 percent.
Originally introduced at NPE2018, the MUD Quick-Change Prototype Adapter System has so far been available on a case-by-case, custom basis, but DME now is building up stock of standard ear plates, locating pins, support pillars and mold straps. Jig plates, replete with pre-drilled holes where 3-D printed cavities can be installed, are available in two sizes: 12 inches by 12 inches, or 12 inches by 15 inches.
“This system allows prototypes to go from design to molded part within five days without the cost of buying aluminum plates and/or inserts to machine the cavity and core of part,” McCutcheon said.
As part of the MUD system, custom-made cavities are hung from standard frames. A number of styles are available, including frames that accommodate one or more cavities.
McCutcheon cited the Double H-Frame, which like other MUD components, is designed for versatility; it can accommodate four cavities that all can be swapped out easily. For example, a molder might want to manufacture four Disney characters. The set might include two that are in greater demand. With the Double H-Frame, the molder could rotate through the characters, devoting three cavities to the two most popular toys and the fourth cavity to either of the less-popular characters. This ensures maximum mold uptime, even while giving the molder lots of options in what it’s able to produce batch to batch.
“The frame remains in the molding machine while the inserts are changed at will,” McCutcheon said.
Because DME makes cavity cores using 3-D printing, the design and manufacturing process takes just a fraction of the time of traditional mold making. The 3-D-printed plastic components don’t last as long as those made from conventional materials; however, they are resilient enough for prototyping. McCutcheon acknowledged one other possible disadvantage: There’s no ejection system. “Every time you run a shot, you have to physically pull the cavity core apart,” he said.
But, for molders that wish to land either prototyping work or new jobs based on how quickly and well they can turn around a short run, the system provides convenience and cost benefits. McCutcheon said the MUD Quick-Change Prototype Adapter System might be of interest to manufacturers in the aerospace, automotive, communications, consumer products, industrial, medical, and the robotics and automation industries.
Karen Hanna, associate editor
Contact:
DME Co., Madison Heights, Mich., 248-398-6000, www.dme.net
Karen Hanna | Senior Staff Reporter
Senior Staff Reporter Karen Hanna covers injection molding, molds and tooling, processors, workforce and other topics, and writes features including In Other Words and Problem Solved for Plastics Machinery & Manufacturing, Plastics Recycling and The Journal of Blow Molding. She has more than 15 years of experience in daily and magazine journalism.
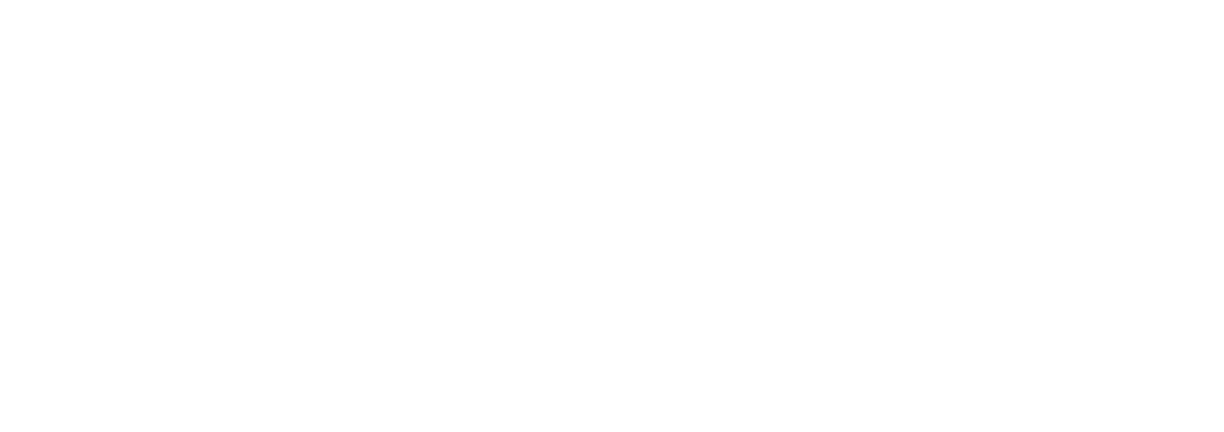