Laser shock peening. A patent for a method and device to improve mechanical properties of additively manufactured metal parts, such as mold components, was awarded to Ecole Polytechnique Federale de Lausanne, Lausanne, Switzerland.
The method the patent describes reduces or may eliminate the need for post-processing steps that follow traditional selective laser melting (SLM), also known as direct metal laser sintering. In lieu of those steps, the patent incorporates laser shock peening (LSP) or warm laser shock peening (WLSP) during the build process. LSP uses a pulsed laser to produce shock waves near the surface of the material. WLSP is similar, but the part is heated and a temperature usually below 350 degrees Fahrenheit is maintained during the process.
In some embodiments, a single laser may be used in a continuous mode for SLM and in a pulsed mode for LSP, or a dedicated laser may be used for each process. After a number of layers of the part have been created via SLM, a confining layer — which may be either a liquid or a solid that allows the laser to pass through it — is applied to the part. “By directing the shock waves to the surface of the material the confining layer ... is increasing the depth of shock wave penetration.” The use of the confining layer in combination with LSP thus boosts what is known as a beneficial compressive residual stress field within the part.
By using LSP at various critical portions of a part as it is being built, the part’s strength is increased when compared to traditional SLM methods that rely on post-processing steps, which typically harden only a shallow area beneath the surface of the part.
Patent 10,596,661; issued March 24
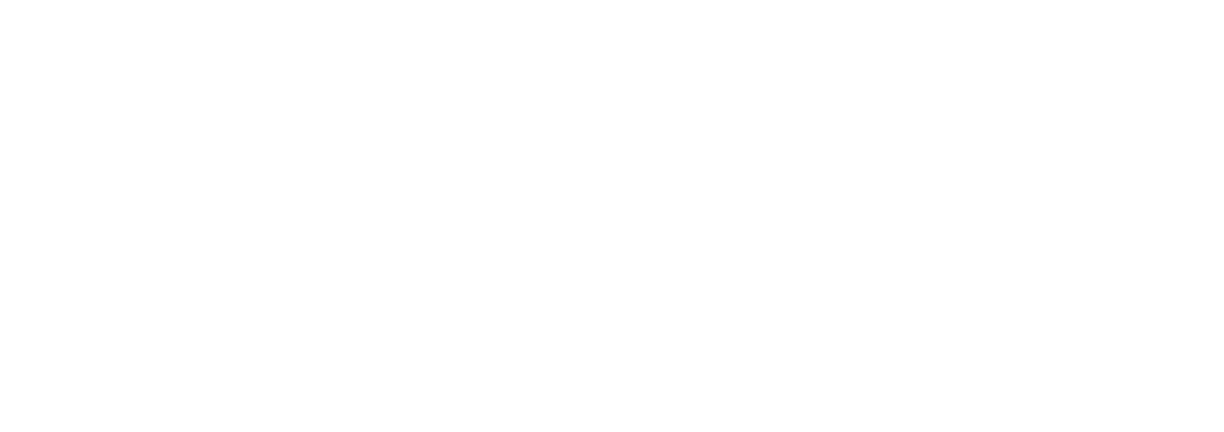