Exhibitors at Amerimold 2019 introduced conformally cooled products, offered updated software and announced a deal between a Chinese company and a U.S. company to make available in North America a wider range of mold base sizes for mold makers.
CONFORMALLY COOLED HOT-RUNNER GATE INSERTS
Next Chapter Manufacturing (NXC MFG), a designer and manufacturer of tooling for the plastics industry, and PCS Co. joined forces to offer two conformally cooled products — hot-runner gate inserts and a sprue bushing. PCS is a manufacturer and distributor of mold components, mold bases, hot-runner products and molding supplies.
The conformally cooled hot-runner gate inserts are 3-D printed by NXC MFG and distributed by PCS, which is the exclusive distributor of the company’s mold components, according to Jason Murphy, president and CEO of NXC MFG. The gate inserts are available in four sizes and fit most hot-runner systems.
“Mold makers will install the gate inserts into their tooling to benefit the injection molder,” PCS sales manager John Harding said. “We sell this concept to the injection molder, so that they can specify the product to the mold maker. The injection molder will benefit in part quality, reduced blushing and better control of heat at the gate tip.”
The gate inserts, which are installed in the nozzles, can fit most hot-runner systems because they are produced with additional machining stock that the mold maker finishes to fit the hot-runner nozzle.
“There are so many different diameters available from hot-runner companies,” Harding said. “We offer four standard gate insert sizes that are made with stock material on them. The mold maker will machine away that extra material so that the inside diameter of the gate insert will match the outside diameter of the hot-runner nozzle, based on recommended tolerances.”
This versatility provides benefits to the injection molder, as well as the mold maker, because the gate inserts are off-the-shelf components, according to Murphy.
“This is a cost-effective solution that can be adapted to most hot-runner systems,” Murphy said. “Mold makers don’t have lots of apprentices as they did 20 years ago. They have to be able to quickly look in an equipment catalog, identify the right solution and modify it rather than make a custom part from scratch, which adds cost.”
That saves the mold maker time, which saves the owner of the mold money.
“The value we offer is the intricate conformal cooling channel,” Murphy said. “Our design envelopes the whole tip and gate insert area. It provides thermal stability. You don’t want to simply blast lots of cooling and cold water in there. You want to be able to control the cooling to keep the mold surface and gate surface consistent with the rest of the mold, so you don’t have heat spikes or heat sinks that cause problems, such as freeze-off or drool.”
The gate inserts are designed to produce parts that have tight tolerances for cosmetic appearance or other characteristics.
“They could be used for medical devices or diagnostic equipment or for parts with critical tolerances, such as a syringe or other medical device,” Murphy said. “The conformal cooling will help prevent heat blush, which causes visual defects. They can be used to produce clean packaging without thermal distortions or wherever there is a need for highly cosmetic parts.”
This is the first time 3-D printing has been used to produce standard, off-the-shelf conformal cooling gate inserts, according to Murphy. The gate inserts are 3-D printed using H13 steel, which is used for high-wear, high-volume applications.
CONFORMALLY COOLED SPRUE BUSHING
Murphy said mold makers can use the conformally cooled sprue bushing as a drop-in replacement for a conventional sprue bushing. Like the conformally cooled hot-runner gate insert, the off-the-shelf product is 3-D printed out of H13 tool steel and its cooling channel is patent-pending.
The sprue bushing transfers melt from the nozzle tip to the mold runner, which guides the molten plastic into the cavity of the mold. The conformal cooling channel is designed to quickly cool the sprue so the part can be ejected more quickly, which improves cycle time.
“The ideal application for the conformalcooled sprue bushing is when you have a small part size compared to a large sprue,” Harding said. “If you are waiting for the sprue to set up before you can open the mold and eject the part, that hurts cycle time. If you can quickly cool the sprue, you are able to eject the part faster.”
Customers using the conformally cooled sprue bushing have reduced their cycle times dramatically, according to Harding and Murphy.
“Case studies show processors are saving from 20 percent to 80 percent cycle time by using conformal-cooled sprue bushings instead of traditional sprue bushings,” Murphy said.
Harding added, “The cooling portion is 70 to 80 percent of the entire injection molding cycle time. If you reduce the cooling time, that will have a big effect on cycle time.”
PCS, LKM PARTNER ON MOLD BASES
In another deal involving PCS, the company shared a booth at Amerimold with LKM, a Chinese mold base manufacturer, to announce a new partnership. PCS will represent LKM in North America as the sales and marketing arm for its custom- machined mold bases.
“LKM approached us to partner to grow their business in North America,” said Jeff Dennis, mold products technical specialist at PCS. “It’s a good fit because we have restrictions on the size of mold base that we can offer. Some of our customers would ask PCS to quote a mold base, but it was beyond our capacity — either too small or too big — and we could not do business with them.”
Prior to the deal, PCS could not provide mold bases outside of the standard sizes it manufactures, which range from 8 inches by 8 inches up to 2 feet by 2.9 feet, he said. Now the company can provide any size mold base up to 14.7 feet by 14.7 feet, ranging from a 0.875-inch thick base to a 2.3-foot-thick base.
“Our mold-making machines were purchased to handle a standard range of mold sizes,” Dennis said. “It’s difficult to do the larger, heavier sizes without adding cost. Now we can be price- competitive on large, heavy molds. We did not want to send our customers to competitors for mold sizes we did not offer.”
The deal benefits LKM because it was not equipped to handle sales, service and delivery issues in North America.
“It was a logistics issue for LKM,” Dennis said. “They don’t handle shipping freight forward and shipping to precise locations in North America. Our network can handle all that.”
PCS agreed to partner with LKM because it is known as a high-quality mold base shop, Dennis said.
“They have very good machining capabilities,” he said. “They are the largest mold base builder in the world. They have over 300 CNC machines, and they run three shifts with 900 machinists. LKM quality is high, and customers trust us.”
R.E.R. SOFTWARE UPDATES SCHEDULING, PRODUCTION SOFTWARE
R.E.R. Software supplies the tooling industry with technology designed to increase efficiency and provide operational oversight. Its products include its InFocus Machining software, as well as InFocus Labor Tracking and InFocus Scheduling.
In March, the company introduced an updated version of InFocus Scheduling that includes Level 4 Automated Scheduling. R.E.R. Software President and CEO Roger Bassous promoted the updated software from his booth at Amerimold.
Automated Scheduling is an update that removes the need for manual scheduling throughout a plant. The automated scheduling update aligns engineering, purchasing, machine scheduling, mold making and product delivery.
“Level 4 Automated Scheduling aligns jobs so that users understand when a project will be ready for each department,” Bassous said. “It assures the correct order of work to meet job due dates, while also ensuring that your resources are not sitting idle. It is an automated planning solution that will adjust and shift tasks in real time.
“For example, if you say, ‘We are going to shoot 1,000 parts, and this is our delivery date,’ and you have 20 of those jobs, it will schedule those in the order that is near-optimal and display the capacity to show if you are going to be late on anything, so you can deal with any shortcomings.”
It achieves this through an artificial intelligence planner that’s in direct and constant communication with all plant resources.
“It will do real-time tracking of all manufacturing resources from job kickoff to delivery,” Bassous said. It also allows users to shift and test different manufacturing scenarios without impacting the actual schedule.
InFocus software is flexible enough for any manufacturing operation, according to Bassous.
“Many of our customers are mold makers,” he said. “Omega Tool Corp. has been using InFocus Scheduling for years, and they updated to the Automated Scheduling option.”
R.E.R. Software also recently updated its module for Job Tracking and Operations Analysis for Press Injection and Production. This machine monitoring software is part of InFocus Machining.
“With the advanced operations analysis software, you can monitor your performance based on certain feeds, temperatures and pressures so you can produce the best parts possible. For example, if you try three different pressures or temperatures, you can analyze the data to optimize future production runs,” Bassous said. “It is an advanced system of operations analysis.”
Bruce Adams, senior staff reporter
Contact:
Next Chapter Manufacturing,
Grand Rapids, Mich., 616-773-1200, www.nxcmfg.com
PCS Co.,
Fraser, Mich., 800-521-0546, www.pcs-company.com
R.E.R. Software Inc.,
Rochester, Mich., 586-744-0881, www.rersoftware.com
Bruce Geiselman
Senior Staff Reporter Bruce Geiselman covers extrusion, blow molding, additive manufacturing, automation and end markets including automotive and packaging. He also writes features, including In Other Words and Problem Solved, for Plastics Machinery & Manufacturing, Plastics Recycling and The Journal of Blow Molding. He has extensive experience in daily and magazine journalism.
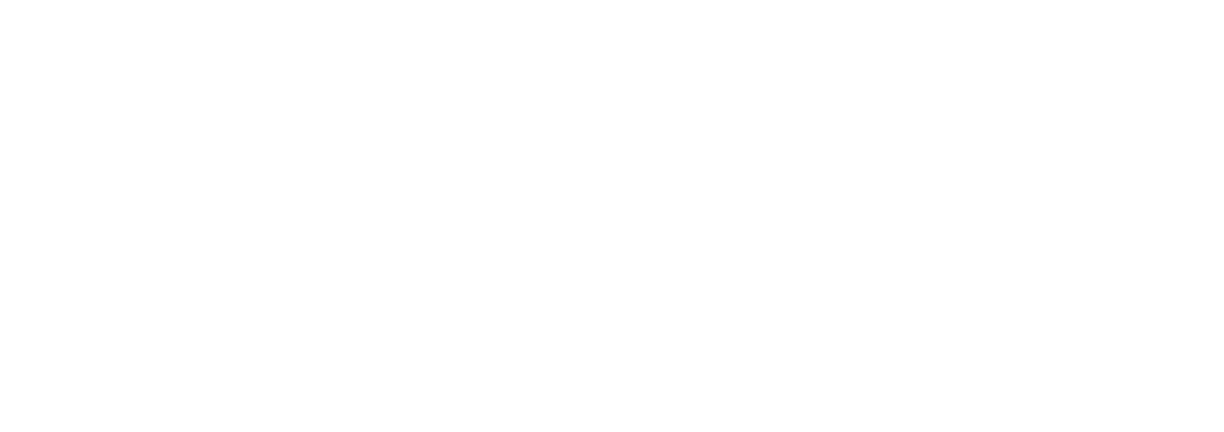