Constraints in rural areas pose workforce challenges for manufacturers
By Karen Hanna
Manufacturers in rural areas face distinct challenges in finding and retaining workers, and they should try to diversify their labor pools and offer employees more flexibility, according to a recent study, published by the Manufacturing Institute’s (MI) Center for Manufacturing Research, with support from public accounting firm Forvis.
At a time when manufacturers across the country are having trouble finding workers, “rural manufacturers have experienced shrinking working-age populations at a higher rate than urban areas,” states the study, titled “The Manufacturing Experience: Attracting and retaining manufacturing talent in a rural vs. urban setting.” Published in August, the study is no less relevant now — according to the U.S. Bureau of Labor Statistics, manufacturers reported 587,000 job openings in October, a slight drop from September, when 601,000 jobs went unfilled.
In surveys conducted in April for the MI study, 57.5 percent of manufacturers reported operations in a rural location. The 142 respondents represented a broad spectrum, including manufacturers involved with chemicals, appliances, machinery, and plastics and rubber products. More than 86 percent said they have been experiencing difficulties filling open positions.
More than 60 percent of urban manufacturers said the availability of labor is a perk of their location, but less than 30 percent of rural manufacturers said the same about their location. In fact, almost two-thirds of rural manufacturers say they face difficulties attracting new employees to their area.
While workers in urban areas are concerned about compensation and the cost of living, those in rural areas face challenges regarding access to services and amenities, such as quality hospitals and entertainment options.
“For rural manufacturers, the concerns in rural areas are more heterogenous and reflect the insufficiency of interrelated systems such as childcare, accessible transportation and affordable housing, which vary in availability from one rural community to another,” the study states.
However, the study found that only 5.5 percent of rural manufacturers provide housing support and only 4.1 percent of them provide childcare as an incentive.
But manufacturers are paying a price to maintain operations in rural locations. According to the study, “rural locations (29.9%) were more likely than urban locations (18.8%) to pay more than their competitors. This indicates that rural locations may feel more pressure to increase wages given the more limited labor supply.”
Manufacturers that responded to the study have devised some creative solutions to respond to workforce challenges. For example, one turned an old dormitory into housing for workers; others have worked with their local community to improve housing and education options.
To grow their own workforce, rural manufacturers are more likely to invest in training programs than their urban counterparts, which rely more heavily on staffing agencies, according to the study.
To find workers where they’re at, one company reported it’s started “Beers and Careers” events at local bars and breweries, at a cost of around $600.
The study recommends that rural manufacturers consider ways they can provide more flexibility to workers who might be struggling to shoulder care responsibilities for children or aging family members. As the population within rural areas continues to shrink, manufacturers also need to widen their search for prospective employees.
As the study states, “rural companies need to widen talent pipelines to include more women, veterans, refugees, second chance and neurodiverse individuals.”
Top benefits cited by manufacturers, by percent, in attempting to attract workers
Rural manufacturers:
Work/life balance (74 percent)
Sense of community (68.8 percent)
Cost of living (66.2 percent)
Career advancement (62.3 percent)
Urban manufacturers:
Access to quality healthcare (64.7 percent)
Work/life balance (61.8 percent)
Karen Hanna | Senior Staff Reporter
Senior Staff Reporter Karen Hanna covers injection molding, molds and tooling, processors, workforce and other topics, and writes features including In Other Words and Problem Solved for Plastics Machinery & Manufacturing, Plastics Recycling and The Journal of Blow Molding. She has more than 15 years of experience in daily and magazine journalism.
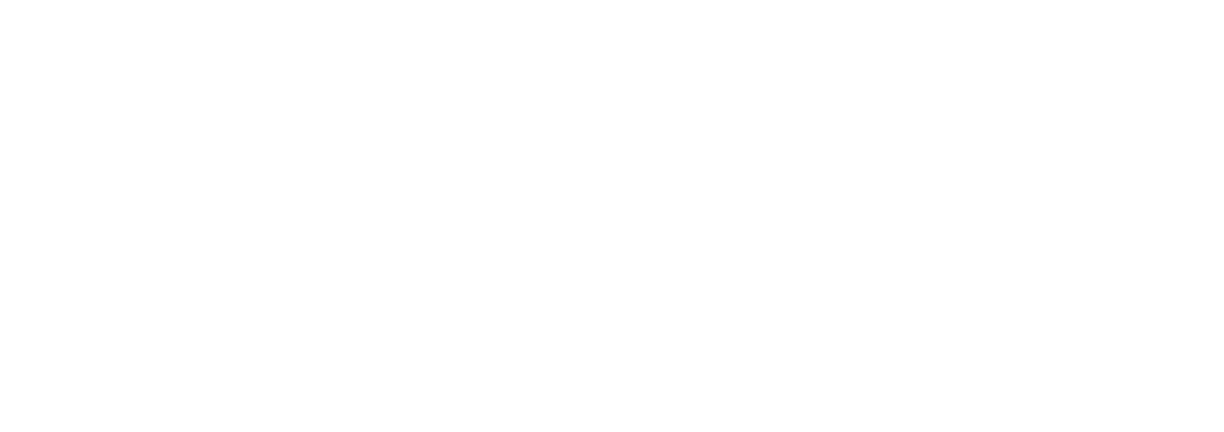