AI can play a role throughout the plastics manufacturing process: Deloitte
By Bruce Geiselman
Artificial intelligence (AI) can help plastics processors improve efficiency throughout their operations, starting with factory design and ending with quality control vision inspections of final parts.
For example, manufacturers can use AI tools within CAD (computer-aided design) software, such as Autodesk, to customize the layout of factories. AI features within the software help designers identify how best to use available space and how to optimize the space for the most efficient flow of materials, said Jimmy Asher, managing director and Smart Factory CTO, Deloitte Consulting LLP. Asher helps companies adopt digital technologies.
Quality control software using AI technology paired with cameras can examine finished parts to identify defects such as cracks, burns or crazing, he added. This can reduce inspection time and increase accuracy when compared with human inspections.
“There is an AI algorithm running that’s either directly on a PC or on a cloud instance [network],” Asher said. “They will take several different readings across the lot as it comes in, enter those readings into the software, and that will give them recommendations on the temperature profile and the pressure profile to optimize for the speed and quality [of the injection molding process].”
Another typical application for AI among plastics processors is for predictive maintenance of an IMM.
“Again, looking at the actual temperature and the pressure correlation of that plastic along with surface defects, [AI can] determine wear and tear for the nozzle, the heating zone, the screen, etc.,” Asher said. “The number of runtime hours, etc., will be fed into those.”
In addition to monitoring the performance of the IMM, AI technology deployed downstream can help identify problems with the injection molding process.
“If I have resin coming in, I mold the part, downstream I’m running screws into that part, and I’m seeing torque values change in that downstream process, that indicates that the geometries of the holes changed, which links back to the molding process,” Asher said.
Beyond the factory floor, AI can help a manufacturer examine supply chain resiliency.
“That can be things like, ‘How likely am I to get my next shipment of resin by the order promised date?’ ” Asher said. “Those have dependencies on things such as weather or broader supply chain disruptions. ‘If I have three suppliers of resin, what’s my expected deviation from my lead time?’ That is an AI type of optimization that is often done to ensure that they meet their lead time. You’re trying to balance between the amount that you stock inside your factory and not running out.”
Weather forecasts, past historical data about suppliers, as well as data involving trucking and rail companies all play into AI supply chain optimization, he said.
“There are a number of different software pieces that are used across the manufacturing stack, and AI is deployed in each and every one of those,” Asher said. “It would start inside of ERP [enterprise resource planning] as there are some AI tools applied there. In long-term planning and MMRP [manufacturing material resource planning], there will be tools there. Inside of MES [manufacturing execution system] scheduling, there will be AI tools there. The computer vision use case that I mentioned, that’s a stand-alone system that’s deployed in the inspection process either through canned AI algorithms or cloud AI algorithms.”
In addition, AI software can help manufacturers navigate the resin market, Asher said.
Design software, such as SolidWorks or Autodesk, offers AI tools to optimize strength-to-weight ratios, he said.
Generative AI and other future applications
In addition to the areas in which AI has traditionally played a role in plastics manufacturing, new opportunities are arising in the “generative AI spectrum,” Asher said. Generative AI is a type of artificial intelligence technology that can produce various types of original content, including text (such as ChatGPT), imagery, audio and data.
“Those areas would be optimizations around continuous improvement, looking at lessons learned from logbooks, manually recorded activities, or maintenance functions to make recommendations,” Asher said. “There are items within factory scheduling of how to optimize a particular batch between color changes, for instance.”
Generative AI can play a role in providing environmental health and safety training for employees.
“They can scan in, for example, a manual from an equipment supplier. An injection molding [machine], for instance, would come with a manual. Inside that manual there would be certain recommendations for both maintenance procedures and safety procedures. Generative AI could be used to scan those manuals to make certain recommendations feed into the EHS [environment, health and safety] systems or to the EAM [enterprise asset management] solutions.”
AI can play a role in path planning for automated mobile robots and autonomous guided vehicles.
“The AI application there is for things like collision detection by the robot itself looking at vision or lidar input, path planning for optimization either by [reducing] congestion or to minimize the number of trips,” Asher said.
AI within cybersecurity software looks for vulnerabilities and anomalies in the manufacturing process, in the flow of information in the IT and OT networks and even outside the factory that might indicate a cybersecurity threat.
New uses for AI regularly are being developed.
“AI is a broad spectrum of software,” Asher said. “There’s a lot of different ways it can be deployed.”
Many of the AI technologies Asher discussed can be seen by visitors to the Smart Factory @ Wichita by Deloitte on the campus of Wichita State University in Wichita, Kan. Deloitte and Wichita State University joined forces to build “a groundbreaking and immersive experiential learning environment” on the school’s Innovation Campus. The smart factory is a highly digitized and connected production facility that uses technologies including AI, Internet of Things and robotics to autonomously optimize manufacturing operations.
Contact:
Deloitte, New York, 212-492-4000, www2.deloitte.com/us/en.html
The Smart Factory @ Wichita by Deloitte, Wichita, Kan., [email protected], www.thesmartfactory.io/
Bruce Geiselman
Senior Staff Reporter Bruce Geiselman covers extrusion, blow molding, additive manufacturing, automation and end markets including automotive and packaging. He also writes features, including In Other Words and Problem Solved, for Plastics Machinery & Manufacturing, Plastics Recycling and The Journal of Blow Molding. He has extensive experience in daily and magazine journalism.
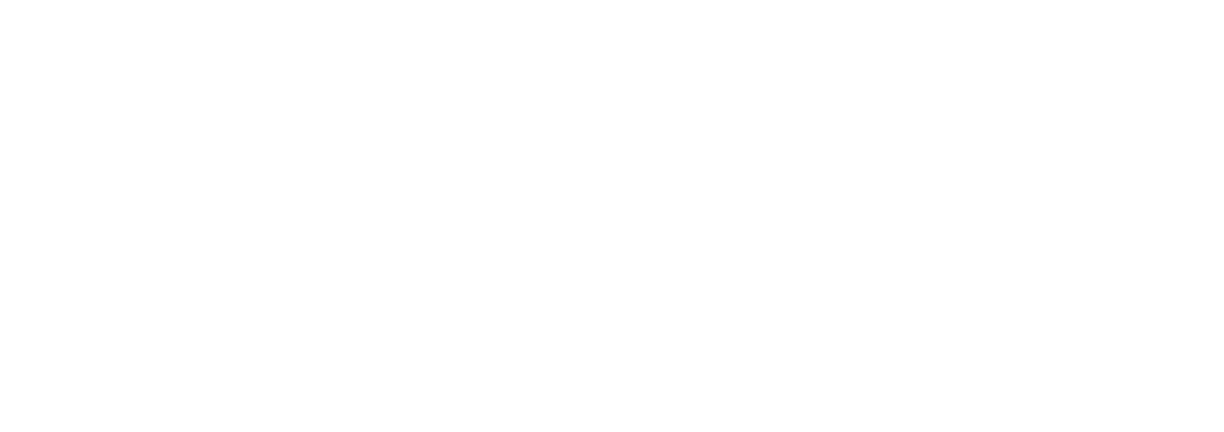