Artificial intelligence isn’t just the stuff of science fiction
By Bruce Geiselman
Artificial intelligence (AI) has long been the subject of science fiction, but the truth is that AI to improve operational efficiency has been available for some time, said Steve Bieszczat, chief marketing officer for the DelmiaWorks product line at Dassault Systèmes.
“When we hear the term artificial intelligence, it’s easy to conjure up the cautionary tale of the HAL 9000 computer in ‘2001: A Space Odyssey,’ ” Bieszczat said. “However, plastics processors have been taking advantage of generative AI for years to assimilate large amounts of historical and real-time data in order toprovide actionable insights. We usually don’t think about the AI tools, though, because they are embedded in software for handling specific functions, such as inventory control, statistical process control and forecasting, to name just a few.”
With AI, manufacturers can benefit from insights derived from voluminous data that would be difficult or impossible for a human to analyze. With capabilities that include automated scheduling, predictive maintenance, product-quality monitoring and machine learning, AI provides more opportunities for manufacturers to automate into the future, according to Anahita Khanlari, solution marketing director at Aspen Technology, also known as AspenTech.
Automated scheduling
DelmiaWorks provides manufacturing execution system (MES) and enterprise resource planning (ERP) software that can help automate manufacturing business tasks, from order processing to scheduling to production and shipping, according to the company.
AI is particularly beneficial when it comes to scheduling repetitive tasks, Bieszczat said. For example, if a plastics processor has 20 or 40 primary processing machines – such as injection molding machines, blow molding machines or extruders – and numerous products running on the machines, calculating optimal scheduling based on available time slots and constraints related to labor and raw materials is extremely complicated. Bieszczat compared it to playing a three-level chess board.
While challenging for a human, perhaps armed with a spreadsheet, efficient scheduling of production can be accomplished within minutes using ERP platforms or dedicated scheduling software that uses AI to analyze large data sets, Bieszczat said.
Predictive maintenance
Predictive maintenance software, which can either be freestanding or part of another software product, such as an ERP, analyzes the run time on a piece of equipment since it was last serviced, along with process monitoring data captured from tooling and equipment.
“Take the case of a scheduled production run that will require a tool to run 20,000 cycles,” Bieszczat said. “If the tool is rated at 100,000 cycles and has already run 90,000 cycles, the predictive maintenance AI function will alert operations that it will be necessary to stop the job at the halfway point to service the tool or risk a mid-job tool failure.”
AI can alert plastics processors to maintenance needs prior to a machine breakdown or work stoppage.
“When we do an automated schedule, we run thousands and thousands of computations against when is it due; when's the raw material going to be here; which machine does it run best on?” Bieszczat said. “It's machine intelligence, artificial intelligence of the traditional nature, coming up with guidance and answers for somebody in the factory.”
Statistical process control
AI also plays a key role in statistical process control (SPC), which uses statistical methods to monitor and control a production process to ensure product quality. High-volume plastics processors are the most likely to use an SPC AI engine, which stores production and process monitoring data. That data is then compared against real-time operating parameters, and if operating conditions begin trending out of bounds, the AI-driven SPC software will trigger an alert or even initiate an automatic shutdown of the machine, Bieszczat said. Such variations could be related to machine temperature that could affect a plastic part’s dimensions, for example.
“Some very smart code is looking at a lot of data and running computations far faster than any human being could do it and advising and predicting an outcome,” Bieszczat said. “We do the same thing for maintenance, repair and operations.”
ERP systems can use AI to set up workflow alerts, Bieszczat said. For example, the software could issue an alert if it determines a plant will run out of a particular material before it can fulfill a purchase order. In that case, it can “wake up” the purchasing agent to order more. If that purchase order is then routed to someone in the finance department who fails to act on it, it can issue another alert.
“These are … the most common applications of AI that you’ll find in plastics processing plants today, but they point to a broader trend in applying generative AI to manufacturing,” Bieszczat said.
Generative AI is a type of artificial intelligence that can produce various types of original content, including text, imagery, audio and data.
“We see some of the largest companies creating their own applications using the latest iterations of generative AI, such as ChatGPT. However, a majority of plastics processors and other manufacturers will continue to expand their use of manufacturing applications that take advantage of embedded AI engines to improve their operational efficiency, productivity and decision-making.
Machine learning
AspenTech, provides a variety of industrial software that uses AI to help plants in asset-intensive industries run their machinery more profitably and sustainably, with greater resilience, Khanlari said.
The company’s customers include polymer manufacturers, as well as chemical producers, design and construction companies, oil and gas exploration and production companies, renewable energy producers, mining operators, and utility companies.
AspenTech’s software uses machine learning (ML) – a subsegment of artificial intelligence that involves feeding large amounts of data to algorithms, Khanlari said in an email. The algorithms start to recognize patterns and learn insights that are used to make better decisions.
“The workflow goes from sensing/input to reasoning and lastly to action,” she said. “ML has different areas such as supervised/unsupervised learning, cognitive
AspenTech’s software relevant to the polymer and plastics industry includes asset performance management software that can predict equipment failure, manufacturing and supply chain systems software for scheduling production campaigns or forecasting demands, Aspen Hybrid Models software that can model complicated unit operations, and advanced process control software to holistically control the operation of entire plants, she said.
“Process control and asset performance are certainly two main areas that benefit from leveraging AI,” Khanlari said. “However, AI applications are not limited to these areas. For example, AI can be used to create soft sensors. We worked with a polymer producer in Asia as a proof of concept to predict the color and haze of the produced polymer based on process conditions. For this purpose, we leveraged a rather large amount of lab-generated data to feed it into our algorithms. This is an example of predicting a property that is not normally measured through simulation or models.
“Another example is an LDPE producer. The goal was to minimize waste by reducing the transition time between grades of production, and to be able to predict some of the product properties like melt flow index or density. The producer leveraged AspenTech’s Hybrid Modeling and was able to optimize their process to cut their transition time to less than half.”
In addition to its other tools, AspenTech offers ProMV, which relies on AI for online process monitoring and providing actionable insights to address potential issues before they impact production key performance indicators.
AI also can help plants optimize energy usage and reduce emissions.
Big versus small
Big companies are making hefty investments in creating and adopting AI-based technologies, but that doesn’t stop many small and mid-sized companies from venturing into the AI world.
“Smaller companies, due to limited resources, might not be able to have large investments in this area, but this does not mean they can’t be early adopters,” Khanlari said. “For small- and mid-sized manufacturing companies, AI-based applications are another tool to keep them competitive in today’s market conditions. We are working with both large and small manufacturing companies on proof of concept and deployment of our technologies.”
“Smaller-sized specialty chemical or polymer companies can leverage this technology to be a fast mover in the market. Hybrid modeling is a good example. It is difficult for a specialty polymers producer to build models for their complex processes or recruit in-house expertise. However, once there is the right amount and type of data, small manufacturers can benefit significantly from this technology. … A hybrid model combines first principles of engineering (e.g., flow equations or reaction kinetics) with AI and analytical algorithms. In this way, we can make sure that the generated result makes physical sense.”
Examples of areas where a company might employ Aspen Hybrid Models include:
- batch processes, which can be too varied to systematically model,
- fluidized bed processes with complex chemical and fluid behavior and
- complex refining units.
The future of AI
The importance and acceptance of AI will continue to grow among manufacturers in the future, Khanlari said.
“Yes, for a variety of reasons,” she said. “There is great demand in the market for automation technologies, including AI. The workforce transition is one of the most important motives. AI and automation are helping industrial companies fill the gap of a retiring workforce by getting new employees up to speed faster and more efficiently."
Another reason for a growing interest in AI is the need for more autonomous operations to improve safety and security, Khanlari said.
“AI is a type of automation,” she said. “Most manufacturing facilities are somewhere along their automation journey, often with the ultimate goal of having a self-optimizing operation. Any application that makes it easier for the user to run the operation reliably, including better demand and production forecasting, equipment-failure prediction capability, and guiding virtual assistants, will be of interest to operation leaders.”
Contact:
Aspen Technology Inc., Bedford, Mass., 781-221-6400, [email protected], www.aspentech.com/en
DelmiaWorks, Dassault Systèmes, Waltham, Mass., 800-693-9000, www.3ds.com/products-services/delmiaworks, [email protected]
Bruce Geiselman
Senior Staff Reporter Bruce Geiselman covers extrusion, blow molding, additive manufacturing, automation and end markets including automotive and packaging. He also writes features, including In Other Words and Problem Solved, for Plastics Machinery & Manufacturing, Plastics Recycling and The Journal of Blow Molding. He has extensive experience in daily and magazine journalism.
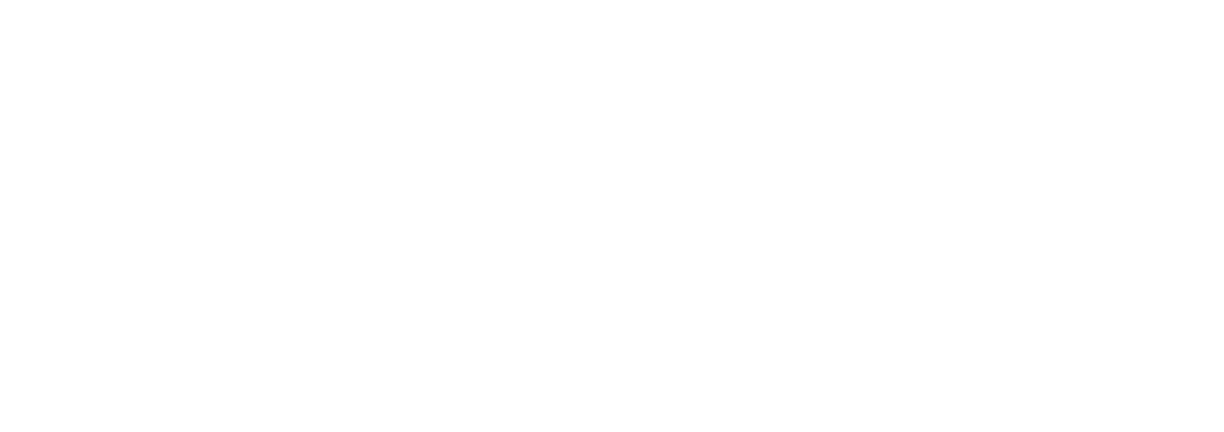