Ineos Composites: Value efficiency is key in automotive industry
By Bruce Geiselman
The ramifications of the transition from internal combustion engine (ICE) vehicles to battery electric vehicles (BEVs) are still playing out, according to at least one industry veteran.
“We’re trying to digest it, and certainly change or adjust our business accordingly,” said Dan Dowdall, a business development manager for resins manufacturer Ineos Composites, who has been in the business for 35 years. “From my perspective, I think the OEMs have always had key priorities, and they’re just shifting a little bit. Some of it is good for plastics, and some of it maybe is not so good for plastics.”
A part of the Ineos Group, a British petrochemical company, Ineos Composites sells resins to many Tier I suppliers as well as smaller compounders. Its resins are used extensively in exterior body panels, pickup truck beds, electric vehicle (EV) battery enclosures and front-end trunks.
The No. 1 priority for OEMs continues to be value efficiency, Dowdall said.
“They’ve been screaming for lower-cost products forever, but I think now as EVs come on more, they bring a lot of cost with them,” he said. “It’s even more important for the OEMs to try to find offsets to the cost of these batteries and motors and everything else.”
The increased demand for cost reductions could benefit the plastics industry because molding plastic parts can reduce the need for welding together several metal parts.
“Historically, plastics are really good at that — at taking four or five welded parts and putting it into a single molded part or integrating attachments and locators and storage compartments, steps on bumpers, dividers and pickup boxes,” Dowdall said. “Plastics generally are pretty good when creative designers get their hands on them at integrating functions.”
Replacing steel body panels with plastics or composites can result in a 30 percent to 50 percent mass reduction, he said.
Dowdall also sees new opportunities for plastics with products for EVs that didn’t previously exist.
“Our business particularly is seeing a lot of growth in frunks, as we call it, or front trunks,” he said. “Because they’re big parts, they lend themselves well to plastics and composites. They’re big and strong, and they have to resist corrosion.”
Another growing area is plastics for battery enclosures. In addition, OEMs are interested in body panels into which sensors and components for sensors and autonomous vehicles can be embedded.
“Vehicles are just full of sensors and electronics right now,” Dowdall said. “They can be attached or molded in the plastic parts with a lot more ease and provide advantages.”
Ineos also is engaged in developing plastics and composites formulated with additives or fiberglass veils that can act as shielding for electromagnetic or radio interference generated by electrical systems on EVs.
While EVs are presenting some new opportunities for plastic parts makers and resin suppliers, there are some negatives, Dowdall said.
“As the world moves to 30 percent electric vehicles, or 50 percent, we’re going to see a lot less engine covers and intake manifolds and radiator supports — some of the traditional areas where plastics has had a dominant position. They’re going to start going away. So, it’s good that we’re finding new applications to replace that business.”
Bruce Geiselman, senior staff reporter
Contact:
Ineos Composites, Dublin, Ohio, 614-790-9299, www.ineos.com/businesses/ineos-enterprises/businesses/ineos-composites
Bruce Geiselman
Senior Staff Reporter Bruce Geiselman covers extrusion, blow molding, additive manufacturing, automation and end markets including automotive and packaging. He also writes features, including In Other Words and Problem Solved, for Plastics Machinery & Manufacturing, Plastics Recycling and The Journal of Blow Molding. He has extensive experience in daily and magazine journalism.
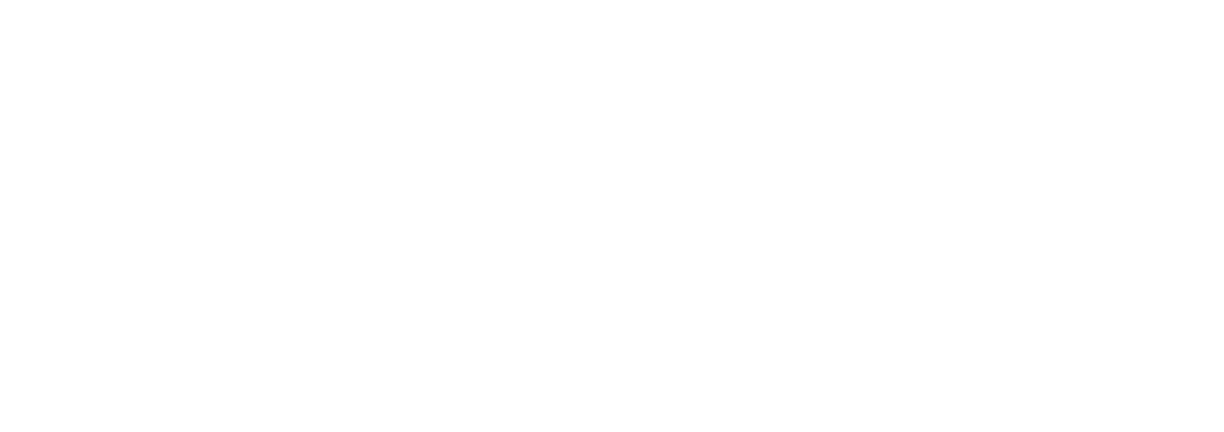