Epson robot allows injection molding company to cost-effectively automate production line
Have you found an innovative equipment solution to a plastics processing challenge? Let us know.
Problem: Cost for automation to stack and transfer a multi-component pack of parts put it out of one molder’s reach.
Solution: A SCARA robot and software from Epson allowed the molder to custom-program its own system.
By Bruce Geiselman
Project engineers at Plastic Designs Inc. (PDI), of Paxton, Ill., were looking for a fast-to-implement and cost-effective system to automate a pick-and-place operation for manufacturing low-cost plastic shims.
However, after contacting turnkey automation suppliers last year, they received quotes of up to $600,000, which company officials said was completely out of the question.
“That was one estimate that we received,” said Zach Allen, a PDI project engineer. “I think we received one other confirmed estimate in the range of, I believe, $250,000, but our management was confident that we could develop a solution in house for less.”
After further research, PDI’s project engineers discovered they could solve the problem themselves by using an Epson SCARA robot and Epson software at a fraction of the cost of the turnkey solution. In addition, the project could be completed in less than two months.
The robot and the included RC+ Express software cost less than $10,000.
“For the Epson robot itself, that’s correct,” Allen said. “There are other expenses with the rest of the automated solution, but in all, we’re under $100,000 for the whole solution.”
“We designed the PLC and the mechanical portion in house, so, with us three engineers working on it for a few months straight, that’s what added up to what Zach said,” said Dustin Kurtz, another PDI engineer.
One of the products PDI manufactures is the Glazelock Stackable Shim Pack, which consists of 16 injection molded plastic shims, each 0.0625-inch thick, used in the installation of windows, doors and cabinets. The shims are heat-sealed along one edge so that users can break off just the thickness they need from 0.0625 inch to 1 inch.
The Shim Pack is Glazelock’s most popular product with sales of more than 16 million shims each year, but the market is competitive and price-sensitive.
PDI molds the shims in bulk, but it has struggled in the past to stack them and transfer them to the heat sealer before packaging. PDI produces more than 90,000 shims per eight-hour shift or about 192 per minute.
“Originally, when we started, we had shims that we were sealing in stacks of 16, and it was a very manual process,” said Ben Zihlman, a third PDI process engineer. “We were having an operator grab the shims from a conveyor and put it on a machine [heat sealer] and that was just a little inefficient, and it was hard to keep it running. It was a long and strenuous process for the operator to sit there all day and continually grab shims and put them on this sealer. That’s the biggest reason we initially went into it [automation].”
In the past, PDI tried to address the need for high-speed stacking and transportation by building a gravity-fed conveyor to help operators hand-stack and hand-transfer the shims. However, the system was imprecise, so the company could end up with 15 or 17 shims in a stack instead of 16.
In addition, there was a lot of waste with shims falling on the floor, according to the company.
A third concern centered on worker ergonomics. Operators had to reach 42 inches to pick up the stacks of shims. While the shims are lightweight, the need for repetitive, long reaches caused workers discomfort over an eight-hour shift.
While realizing they had a need to automate the shim handling process, PDI engineers struggled to find a cost-effective solution. They discovered the answer in October 2021 while attending the Assembly Show in Rosemont, Ill.
The PDI engineers were intrigued by a demonstration at the Epson booth at the trade show, where the company was demonstrating its new RC+ Express software for easily programming robots. FPE Automation, of Elk Grove, Ill., an Epson distributor, followed up with PDI by presenting a quote for an Epson T6-B SCARA robot, which included the software and one day of training.
The Epson automation solution allows PDI to create simple applications for the Epson SCARA robot without the need for any coding. RC+ Express features a highly visual, block-style robot teaching environment with numerous premade templates for common operations. It also includes a 3D simulator to help users visualize and fine-tune applications before implementing them on the equipment.
The entire process of adopting the new automation system, after a one-day training session, took only about two months, according to the company. Most of that time was spent building a new heat sealer to work with the robot. Additional work was done on the PLC so it could communicate with the robot. The drag-and-drop nature of RC+ Express made programming the robot simple, Zihlman said.
“This solution allowed us to stack the shims in stacks of 16, which alleviated the operator from having to count,” Kurtz said. “Our SCARA robot currently picks up those stacks, and then the output is just sealed stacks of 16.”
Once the Epson system was in place, it resulted in improved product quality and reduced scrap while increasing production capacity by 20 percent, PDI said.
“That’s a pretty significant savings, and we’re able to pass that through to our customer,” Allen said.
In addition, the company cited several advantages to installing the Epson robot that went beyond what the team initially expected:
First, the robot is able to create a much straighter stack of shims coming out of the heat sealer than operators achieved when stacking shims by hand.
Second, troubleshooting the operation is now far easier. In the past, problems involving the heat sealer were difficult to pinpoint because it was difficult to know if operator error might have been to blame. But the automation system eliminates that potential problem.
Third, PDI has reduced the labor requirement from one full-time operator to one operator working one-quarter to one-half of his or her time on the stacking operation. This allows those employees to focus more on quality checks and other more-productive, less-repetitive tasks, said Zihlman.
And finally, after seeing the benefits of the Epson robot and software, PDI’s client, Glazelock, is considering new sizes and configurations of the Shim Pack product, Allen said.
“They are fully supportive of the automation,” Allen said. “The quality improvements are great, and we’re working with Glazelock closely to find other opportunities for their product lines where we can automate packaging and post-processing, handling and things like that, because their volumes continue to increase, and we’re able to support those with better processing and more automation.”
Future automation could be applied to existing Glazelock product lines, as well as new products.
Bruce Geiselman, senior staff reporter
Contact:
Epson Robots, Carson, Calif., 562-290-5910, www.epsonrobots.com
Bruce Geiselman
Senior Staff Reporter Bruce Geiselman covers extrusion, blow molding, additive manufacturing, automation and end markets including automotive and packaging. He also writes features, including In Other Words and Problem Solved, for Plastics Machinery & Manufacturing, Plastics Recycling and The Journal of Blow Molding. He has extensive experience in daily and magazine journalism.
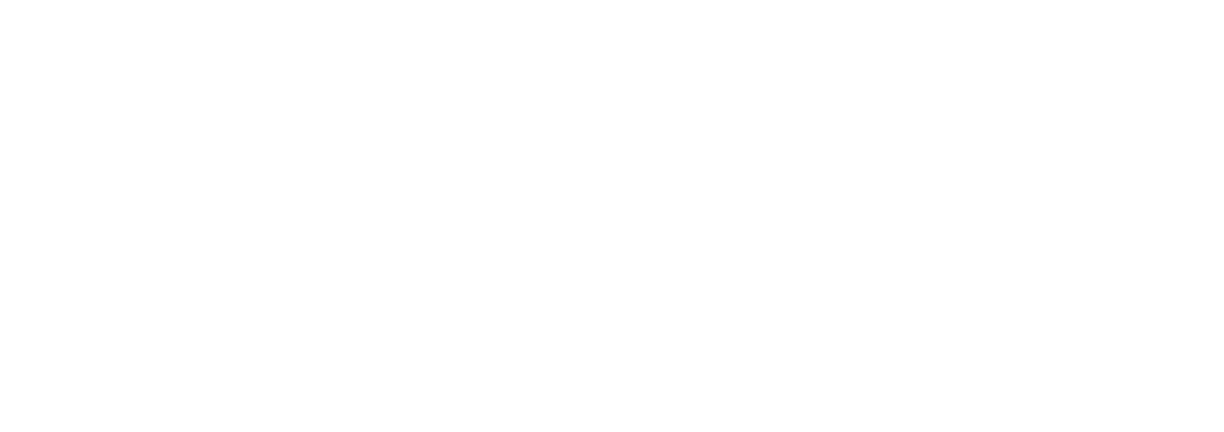