Read more on the labor crunch: https://plasticsmachinerymanufacturing.com/21248002/.
By Karen Hanna
Shuttered storefronts, delayed appointments, darkened fast-food dining rooms.
If you feel like a segment of the population just disappeared overnight, you’re not alone. Even economists can’t account for all the empty positions currently contributing to gridlock throughout the economy.
“I can’t give you a really good answer, because no knows where everyone went,” said Curtis Dubay, a senior economist for the U.S. Chamber of Commerce. “This is kind of unprecedented to see such a crunch on the labor front.”
For many people frustrated by slower service or missed deadlines, diagnosing the problem is simple: “No one wants to work anymore.”
The response is common among employers looking to fill positions in their plants, but three months after extended federal unemployment benefits expired in September — and six months after many states nixed them on their own — economists cautioned that the answer to where everyone went is much more complex. And when they will come back is anyone’s guess.
By the numbers
According to the U.S. Bureau of Labor Statistics, 7.4 million people were actively looking for work in October; however, employers had 10.4 million job openings in September — the month when the most recent, preliminary, job-opening statistics were available. Of them, the manufacturing sector recorded 897,000 openings.
Perc Pineda, chief economist for the Plastics Industry Association, had estimated that the plastics industry alone would see about 145,000 job openings between 2019 and 2029, but, thanks to the disruptions caused by the COVID-19 pandemic, he's tacked on an estimated of 5,700 additional openings — a 4 percent increase. His projection now tops 150,000.
Among manufacturing workers, unemployment in the sector fell in October 2021 to 3.3 percent from 5.2 percent in October 2020, according to the U.S. Bureau of Labor Statistics. At 5.4 percent, the rate was even higher in January 2020, right before the pandemic struck.
In response to surveys conducted as part of a Deloitte and Manufacturing Institute report, 77 percent of employers in the manufacturing sector said they expected ongoing challenges.
Strains on the labor market come as it grapples with a yearslong shortage of skilled workers.
“We’ve been experiencing labor shortages for the past couple of years, and really those shortages are due to the skills gap,” said Jason Alexander, national manufacturing sector leader at RSM, an audit, tax and consulting firm that specializes in supporting mid-sized companies.
In years past, some companies would have recruited foreign workers, Alexander said; however, in response to the pandemic, governments effectively shut their borders.
Some manufacturing companies have outsourced some of the jobs. Many have focused on substituting technology for labor, Alexander said, but that strategy underscores the need to develop workers adroit with advanced technologies, including automation and robotics.
“If you look at a significant portion of the current workforce right now, they don’t have the skillset to be able to operate within that environment,” he said.
According to the Deloitte and Manufacturing Institute report, “Creating Pathways for Tomorrow’s Workforce Today,” competition for workers prepared to perform in the smart factory of the future will be especially fierce. By 2030, 2.1 million jobs could go unfilled because of skills gaps, at a potential cost to the U.S. economy of more than $1 trillion.
Exit exam
Alexander, Dubay and Pineda attribute the current labor shortfall to a number of factors, most related to the COVID-19 pandemic. They include disruptions in the availability of childcare and continuing fear of the coronavirus. Top of mind for the economists, though, is an acceleration of the rate of retirements of older Americans, and the financial freedom of some younger Americans to delay a full return to the workplace.
Between Feb. 3, 2020, when the U.S. declared a public health emergency, and Nov. 17, 2021, the S&P 500 grew more than 44 percent. Since March 2020, Americans have built up $4.5 trillion in savings — about $2.6 trillion more than might have been expected in non-pandemic times, Dubay said.
“Around [17] percent of the U.S. labor population are in the ages of 55 to 64, and this was in 2020. So, if you were 64 years old then, last year, how bad was it to stay at home with stimulus checks and not go to work and [then] the following year retire?” Pineda said.
Extended unemployment benefits, along with other safety-net expansions, including a moratorium on evictions, have created options for younger workers, too. Alexander observed that a significant amount of wealth has transferred hands as a direct result of the pandemic.
“If you look at a not talked-about-enough impact of the 740,000 or so deaths that were caused by the pandemic, it’s created a windfall among some of the younger cohorts that is likely financing the walkaway of those workers from employment,” he said.
As of Nov. 17, the pandemic had killed more than 766,000 people in the U.S., including more than 150,000 under the age of 65, according to the Centers for Disease Control and Prevention. A recent study by Penn State College of Medicine projected that more than half of the people who have been diagnosed with COVID-19 worldwide will experience symptoms of long COVID, which can be debilitating; other studies have put forth significantly lower estimates.
The U.S. had recorded 47.4 million COVID-19 cases; worldwide, case counts were nearing 260 million by the end of November.
According to the National Center for Health Statistics, more than 874,000 people have perished in the U.S. since Feb. 1, 2020, in excess of the number of people who would have expected to die.
The virus’ impact on the economy, too, is still being felt, Alexander said.
“I think we’re still seeing some of the effects from the pandemic, in regards to the delta variant. If you look at the last wave of the pandemic, you’re involved in a delayed reopening of schools, as well as daycare,” he said, “which prevented a significant cohort that bears the brunt of the burden of either childcare or relating to the home, which is prime-age women age 25 to 54.”
Taking account of the dangers of the pandemic, as well as hardships created by disruptions to schools and daycares, he said workers have had more freedom — and more reasons — to decline work.
“If you look at the shock of the pandemic, it appears to have elicited a behavior change among younger workers that are really taking time to reassess their lives and their professional careers,” Alexander said.
Stops and starts in manufacturing
Due in part to the uneven and rolling shutdowns wrought by quarantines, the economy is out of sync, Pineda said.
Companies that reopened fully find themselves at the mercy of those that never totally regained traction, creating bottlenecks throughout the economy, Dubay said.
“You have lots of job openings, but at the same time, you have lots of jobs that, if you can’t finish your product, then you don’t need the workers,” he said.
With the labor participation rate at 61.6 percent in October — in contrast to 63.4 percent in February 2020’s — the manufacturing sector could be facing a competitive disadvantage. Salaries and wages are up 3.7 percent over the past 12 months, but the field doesn’t appear to appeal to everyone.
“It appears that not enough potential workers show an interest in making a career in manufacturing,” the Deloitte and Manufacturing Institute report states. “And this situation could get worse as major employers of warehouses and distribution facilities hire tens of thousands of new workers on wages that resemble manufacturing’s entry positions. These jobs can offer flexible schedules and can provide better work/life balance.”
Some people joined the gig workforce, or started their own businesses, Dubay said.
But, with so many choices, others just left, voting with their feet in an era that has already earned the sobriquet, “The Great Resignation.”
A record 3 percent of workers quit their jobs in September, following a summer with quit rates exceeding 2.5 percent; the figure includes 3.4 percent of private-industry workers and 2.7 percent of workers in the manufacturing sector.
Workers are taking stock of what matters most to them, and some are ghosting their employers, especially in the hospitality and retail sectors, Alexander said.
“A lot of the conversations that we’ve been having with our clients is workers are just walking away with no notice given,” he said.
End in sight?
To return to something like more normal labor conditions, Dubay believes the country must get past COVID-19. And people must spend down their savings, which will take time.
In the meantime, technology investments will continue to buoy companies as they try to weather the challenge, Alexander said.
“Hopefully, as we’ve seen schools continue to open and hopefully the virus continues to be in check, we expect over the next three to six months, we might see some improvement,” he said.
But some people’s disappearance from the labor market could be permanent, Dubay predicted.
“I do think you’ll see a reduction in the labor force participation rate, especially among women, who will decide that they’ve figured out ways to make it work with one income,” he said.
Dubay believes that the labor market will return to more predictable patterns by the middle of next year, but acknowledged there is a possibility it won’t.
“The other option is that this is a structural break, in that there’s just something that’s changed, and people have decided that they don’t want to work, don’t need to work and figured out how to make ends meet in other ways, and that therefore we’ll have a much longer-lived worker shortage than we initially feared,” he said.
Karen Hanna, senior staff reporter
Contact:
RSM US LLP, Chicago, 800-274-3978, https://rsmus.com
Plastics Industry Association, Washington, D.C., 202-974-5200, www.plasticsindustry.org
U.S. Chamber of Commerce, Washington, D.C., 202-659-6000, www.uschamber.com
Karen Hanna | Senior Staff Reporter
Senior Staff Reporter Karen Hanna covers injection molding, molds and tooling, processors, workforce and other topics, and writes features including In Other Words and Problem Solved for Plastics Machinery & Manufacturing, Plastics Recycling and The Journal of Blow Molding. She has more than 15 years of experience in daily and magazine journalism.
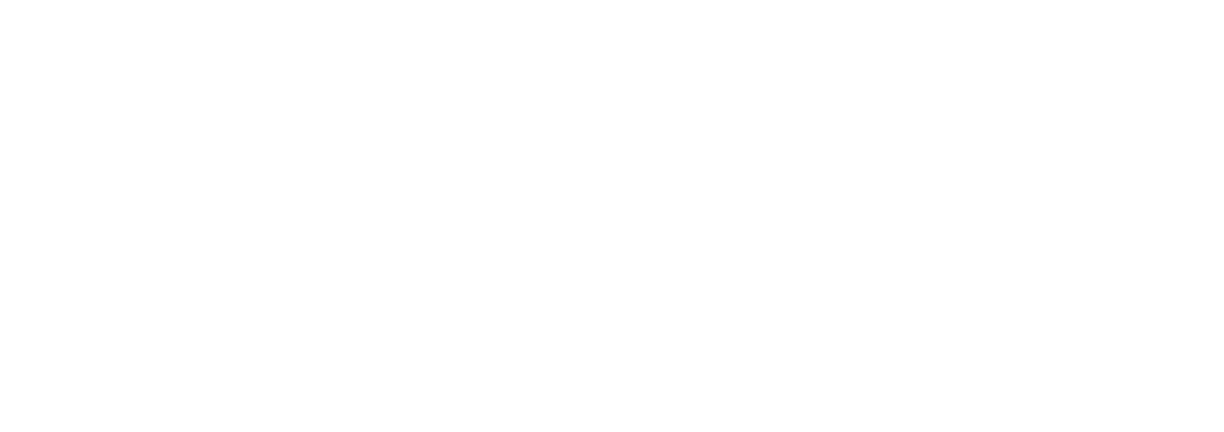