Have you found an innovative equipment solution to a plastics processing challenge? Let us know.
Problem: Testing the clamping force of injection molding machines was a time-consuming task for one Indiana plant.
Solution: New technologies from Gefran offer the plant a convenient way to troubleshoot molding problems and spot issues that could lead to broken tie bars.
By Karen Hanna
With 34 injection molding machines (IMMs) in operation to produce closures and mechanically inserted plug and flange assemblies and drums, the Auburn, Ind., TriMas Packaging facility of Rieke Corp. takes troubleshooting seriously. But things can always go wrong — in the past year, it’s experienced four broken tie bars.
“Normally, tie-bar damage and clamp issues are minimal, but we wanted to be sure we had the equipment to validate issues when they arise and not wait for a technical service person to be brought in,” said Gary Conley, facilities manager at the plant, which has used strain gauge technologies for maintenance and diagnostics.
The plant’s IMMs represent technologies from a broad swath of manufacturers, including Husky, Van Dorn, Toshiba, Toyo, Haitian, KraussMaffei and Arburg. About 175 people work at the plant.
In March, the plant turned to a new tool — the QE2008-W wireless strain-measurement system, officially released in North America in July by Gefran, an Italian multinational company that specializes in sensors, systems and components for the automation and control of industrial processes.
“One of the service technicians we had on a call used one, and it seemed far easier than the dial indicator method we were using,” Conley said. “We made the purchase to step up our preventive maintenance (PM) program.”
According to Gefran, the QE2008-W strain-measurement system can measure clamping force, and bending and cavity pressure to help manufacturers maintain quality control, protect equipment from damage and enable effective collaboration. It can sample as many as 1,000 measurements per second.
“We have had the ability to perform the clamp force testing, but it was not user-friendly,” Conley said. “With the QE2008-W, it is a simple, quick process to perform force testing. Additionally, it has some new features we plan to integrate into our quality systems.”
Equipped with eight sensors that mount magnetically to tie bars, the system also helps with mold alignment to ensure that force is equally distributed, thus minimizing issues like flash, plastic deformation and mold damage. It renders fast readings of the cavity pressure profile — an indirect indicator of pressure on the tie bars during the injection cycle.
“To mitigate the impact of bending forces, the QE2008-W uses four sensors, evenly distributed around the tie bar, mounted at 90-degree intervals. By averaging the readings from these sensors, the QE2008-W measures maximum tension to determine the angle and direction of the bend, achieving greater accuracy of tension and compression measurements for each tie bar,” Gefran product manager Theng Theng Chua said, according to a company press release.
At its Auburn plant, Rieke is using the technology to troubleshoot molding issues, and, Conley said, “for clamp force validation and broken tie bar detection in our PM program.”
“This system cuts our clamp pressure checks by 50 percent, and the digital accuracy is great compared to dial indicators,” Conley said.
The strain-measurement system has provided improvements over technologies used previously by the plant, which anticipates pressing the technology into service for other applications in the future.
“Our use of the system is still in the infancy stage,” Conley said. “We have used it to validate equal pressure for troubleshooting issues. We have also performed a couple PMs, in which we ensure the clamp pressures were correct. We have yet to explore the bent bar and injection cycle portions of the package.”
One benefit of the technology both Conley and Gefran lauded was its ease of use.
According to Gefran, technicians can install the strain-measurement system in minutes. No wiring is required. They also can move the non-invasive sensor between different machines and several types of molds.
Compared to permanent methods of measurement, the system costs less to operate, Gefran said.
The QE2008-W, which features a low-energy Bluetooth communication system, is the first wireless strain-measurement system with an integrated accelerometer, Gefran claims. This allows it to be mounted easily, according to the press release, “with no diameter-dependent templates or guessing required."
Using integrated RAM, each sensor of the QE2008-W can take measurements at a rate of 1 kilohertz and save them during the measurement period. Once a measurement is complete, the sensor seamlessly transmits the saved data to Gefran’s free Sensormate app for further analysis and reporting.
The Sensormate app allows users to capture, analyze and share measurement data via smartphones, tablets and computers.
“Gefran’s Sensormate app serves as the digital interface for the QE2008-W system and with a connection to your network, users can locate the sensors wirelessly through our app and then download measurements as raw data or put the information in a chart,” Gefran product specialist Nikunj Patel said. “You can quickly summarize all your test values and measurement data into a PDF report, include screenshots and add comments to give readers contextual details or troubleshooting notes.”
According to Conley, checking the system is a quick process.
“Prior to the Sensormate, we used a strain gauge system involving dial indicators. The time to use the old system varied quite a lot due to infrequent use and if a second person was available to assist,” Conley said. “With the new system it is very simple for one person to perform the checks and send the results to me.”
That makes PM easier — and ensures that Conley and his department can keep machines up and running, and making parts. “It is highly important that machines are tuned up and making quality parts,” he said.
Karen Hanna, senior staff reporter
Contact:
Gefran, Inc., North Andover, Mass., 888-888-4474, www.gefran-gobeyond.com
TriMas Packaging, www.trimaspackaging.com
Karen Hanna | Senior Staff Reporter
Senior Staff Reporter Karen Hanna covers injection molding, molds and tooling, processors, workforce and other topics, and writes features including In Other Words and Problem Solved for Plastics Machinery & Manufacturing, Plastics Recycling and The Journal of Blow Molding. She has more than 15 years of experience in daily and magazine journalism.
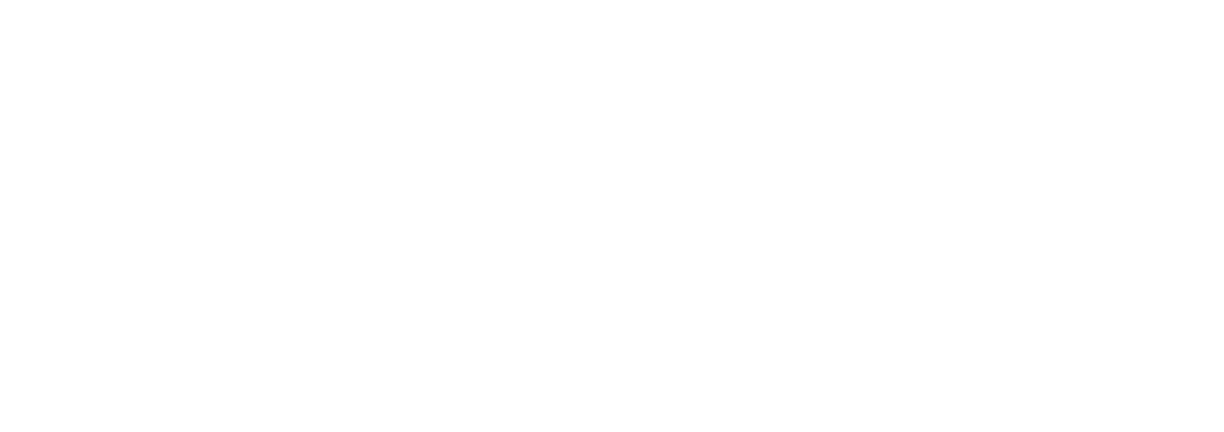