MuCell This physical foaming process for injection molding, developed by Trexel, adds a physical blowing agent, usually nitrogen, to the melt and allows users to produce lighter parts. Compared with conventional molding methods, the process uses less material and produces a smaller carbon footprint.
What’s new? KraussMaffei’s HPS-Physical Foaming universal screw for MuCell, designed to allow molders to use multiple materials in physical foaming processes. It incorporates a modular concept that allows users to bolt on appropriate screw components to deal with different materials, as well as variable fiber or filler proportions. KraussMaffei conducted trials with a range of materials, comparing the performance of traditional screws to the universal screw’s capabilities when provided with different components in its mixing and gas-supply areas, center backflow barrier and three-zone area.
Benefits Versatility. The new screw can be optimized for use with a range of materials, eliminating the need for a different screw to work with every material change. It also offers a 30 percent higher plasticizing performance than traditional screws, and it exhibits better wear behavior.
KraussMaffei Corp., Florence, Ky., 859-283-0200, www.kraussmaffei.com
David Tillett
Associate Editor David Tillett writes and edits for Plastics Machinery & Manufacturing, Plastics Recycling and The Journal of Blow Molding. He covers new products, industry news, patents and consumer and business equipment. He has more than 20 years of experience in daily newspaper, online and magazine journalism.
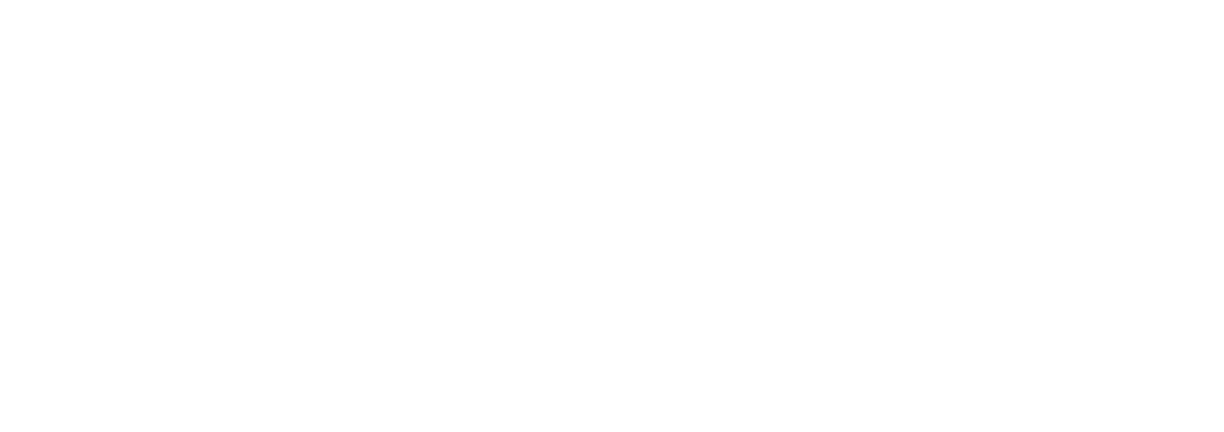