Composite tape process produces rigid, compact parts for vehicles
By Karen Hanna
In an effort to accommodate ever-more electronics within vehicles, Engel has pioneered a process it says will help vehicle-parts makers cram more into tight spaces, without compromising part stiffness.
To make the seat base, Engel and KTM created a composite of tapes and fabrics with a PP matrix, then inserted the matrix into both halves of the mold, said Franz Füreder, VP of Engel’s automotive and mobility business.
The process has potential for manufacturers of a variety of parts, he said.
“The technology can be used for a wide spectrum of semi-structural components in all mobility sectors aiming for less weight, less material and less part thicknesses while providing very high stiffness,” he said. “It always depends on the mechanical properties needed. In the case of the motorcycle seat bases, we can already meet the required stiffness with a single-layer UD-tape due to the specific mechanical properties of the sandwich structure.”
He said that tapes for the seat base are very thin, and because they don’t need to be preheated, the process is relatively energy-efficient.
Standard injection molding machines can perform the process, but they must be very precise, he said. To produce the seats, Engel used one of its victory presses.
In contrast with thermoplastic seat bases made by injection molding, the composite seat base requires less geometric stiffening — ribs for traditional seats can contribute to a relatively high thickness of up to 9mm — and offers two-thirds more installation space. Weight can be reduced by 26 percent.
“For this application, there is no need for tape stacking and consolidation, which makes the process more efficient and cuts both production time and costs,” Füreder said.
The structure is both resilient and compact. “Thanks to the sandwich structure, movements are absorbed very well, as the sandwich achieves greater rigidity in the edge areas of the component and more elasticity in the core,” he said.
The process has other benefits, too.
When using PP, the tape sandwich process reduces global warming potential (GWP) by 27 percent.
But, with PP from renewable sources, the GWP value is reduced by 85 percent.
“Due to the specific mechanical properties of the sandwich structure, we can already meet the stiffness required for motorcycle seat bases with a single-layer UD-tape,” Füreder said in a press release. “This means that the tape sandwich process requires significantly less energy and simpler production cell technology than conventional fibre-reinforced plastic composite processing methods. At the same time, the production costs drop.”
Parts made using the sandwich tape process are recyclable.
With vehicle makers of all stripes looking to integrate more electronics — especially as manufacturers electrify the drive train — the process has implications beyond motorcycles.
“We are accommodating increasing numbers of electronic components on the vehicle and need space for them,” said Hans Lochner, who serves as KTM’s head of material and applications.
Karen Hanna, senior staff reporter
Contact:
Engel Machinery Inc., York, Pa., 717-764-6818, www.engelglobal.com
Karen Hanna | Senior Staff Reporter
Senior Staff Reporter Karen Hanna covers injection molding, molds and tooling, processors, workforce and other topics, and writes features including In Other Words and Problem Solved for Plastics Machinery & Manufacturing, Plastics Recycling and The Journal of Blow Molding. She has more than 15 years of experience in daily and magazine journalism.
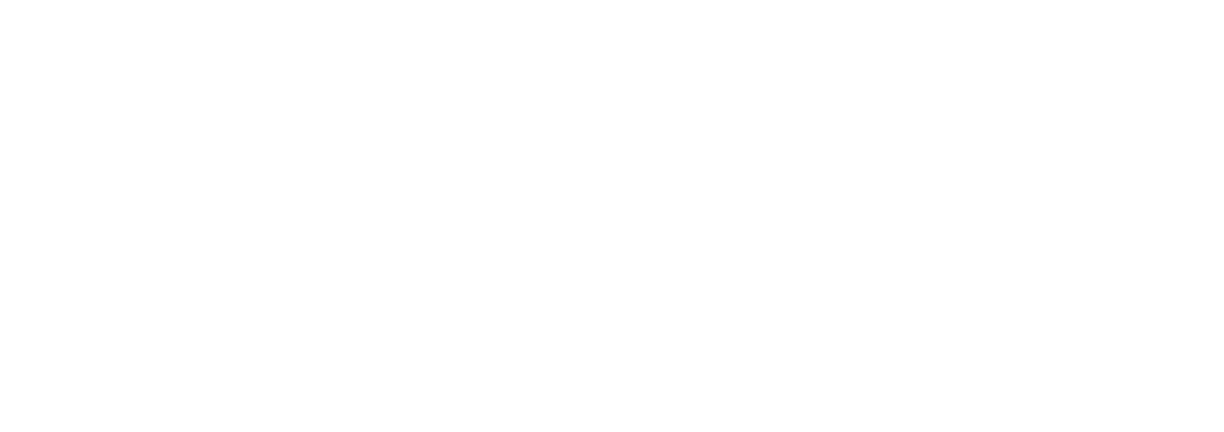