By David Tillett
Wittmann plans to integrate a range of novel elements to produce three-component to-go coffee cups on the K Show floor.
On a line anchored by a servo-hydraulic SmartPower 400/750H/210S/525L Combimould press with three injection units, the cups were to be made with a Bornewables PP blend from Borealis. The renewable raw material’s feedstock originates from bio-mass, waste and second-generation residual substances. Its product safety and performance features are comparable to modern polyolefins, and it offers a significant carbon dioxide footprint reduction.
Austrian firm Haidlmair supplied the mold, which is laid out optimally for processing Bornewables material. It also optimizes cooling using hybrid elements — conventionally processed tool steel with 3D-printed yellow bronze in the mold plate.
The machine will be equipped with a rotary unit and a two-station family mold. When the process starts, the first injection unit will provide a shot of a translucent Bornewables material, creating the cup. The rotary unit will turn, and the first injection unit will form a cup in the first station. In the second station, the cup will be overmolded with an opaque Bornewables material shot from the second injection unit. Wittmann’s Cellmould lightweighting technology will be used to foam the melt in the second injection unit, providing insulating properties that help keep beverages in the cup hot.
Simultaneously, the third injection unit will shoot its Bornewables material into a second cavity, forming the cup lid. Each of the three parts can be colored individually with its own masterbatch.
When the mold opens, a WX142 robot will remove the finished parts from the second station and deposit them on a conveyor belt. The rotary unit will turn, and the process will begin again. The parts will move down the conveyor to a flow wrapping machine and then on to be packaged. The packaging material also is part of the Bornewables product family.
The resulting finished cup is produced entirely from the non-petroleum-based Bornewables material. According to Wittmann, it’s reusable and advances the cause of the circular economy by being 100 percent recyclable. Wittmann has a range of displays, including in Hall 15, Booth C06.
Contact:
Wittmann USA Inc., Torrington, Conn., 860-496-9603, www.wittmann-group.com
David Tillett, associate editor
David Tillett
Associate Editor David Tillett writes and edits for Plastics Machinery & Manufacturing, Plastics Recycling and The Journal of Blow Molding. He covers new products, industry news, patents and consumer and business equipment. He has more than 20 years of experience in daily newspaper, online and magazine journalism.
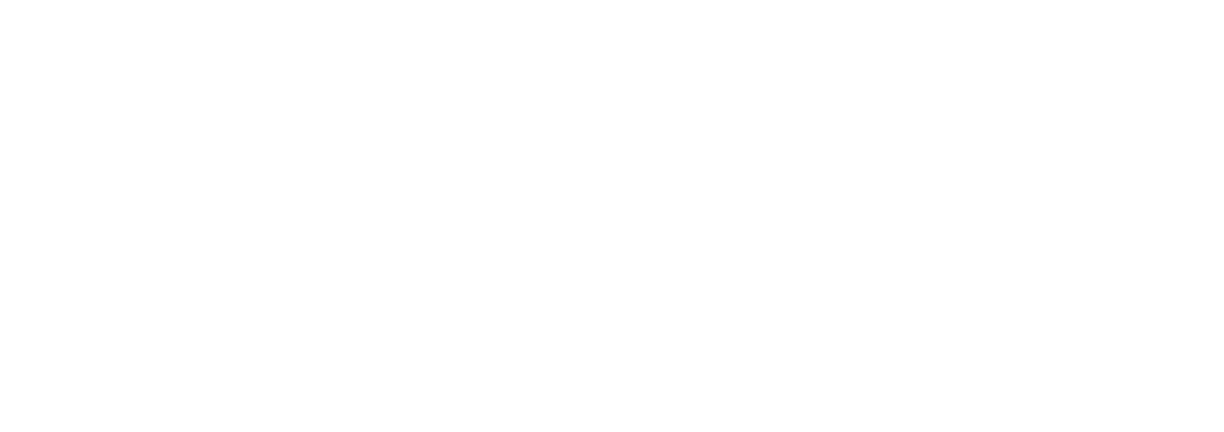