The wheeled trash cart most people roll out to the curb every week is an example of how difficult it can be to develop new uses for recycled resin, but also how a savvy processor willing to invest in state-of-the-art equipment can solve the problem.
Cascade Cart Solutions in Grand Rapids, Mich., a division of Cascade Engineering Inc., has injection molded an estimated 35 million trash, recycling and compost carts in the past 40 years. The carts have included post-consumer resin (PCR) and post-industrial resin (PIR) content for many years, primarily PCR from carts at the end of their life.
But for the past 18 months, Cascade Cart’s trademarked EcoCart has also included up to 10 percent post-consumer curbside resin (PCCR). That is a breakthrough.
“PCCR is material that is pulled out of the curbside programs,” said Brian Miller, Cascade Cart sales manager. “Residents are recycling plastics at the curb, it goes to an MRF, then to a plastics recycler and back to us to go into an EcoCart.”
Depending on the color a customer orders, an EcoCart can contain up to 50 percent total recycled material, but the current practical limit of PCCR is 10 percent.
The reason for that limit is that PCCR can contain materials, additives and colorants that make it difficult for Cascade Cart to meet its high standards for durability and appearance. On the other hand, the company knows exactly what is in the material it recycles from carts that have reached the end of their life.
“There is an issue with consistency,” Miller said. The cart has to pass extensive physical wear testing and meet color standards. “Carts can take a lot of abuse from the collection truck’s grabbers and tipping system, so it has to pass all our physical testing and meet a three-lifetimes standard.
“Ten percent is the sweet spot right now with the stream of PCCR material we have available today,” Miller said. “But we think we have just scratched the surface with this PCCR material. It’s an ongoing development and evolution for PCCR. As advancements come in sorting equipment and things like that, we fully hope to be able to continue to increase that amount.”
The effort to use more PCCR came about after China stopped taking plastic waste from foreign sellers. That material has value, Miller said. “We’ve created a market with our EcoCarts and domestic markets are what we need.”
Cascade Cart’s 96-gallon roll-out cart contains 30 to 33 pounds of resin, so as much as 16 pounds could be PCR, or 13 pounds of PCR and 3 pounds PCCR, depending on the color of the cart.
Cascade Cart has used a variety of molding machines over the years, but is now on track to switch to Engel presses. It has eight injection presses averaging 4,000 tons of clamping force. One of the older processing machines is a Battenfeld 9000, which is actually two 4,500-ton machines in tandem.
An Engel duo 4,400-ton machine equipped with iQ weight control software was delivered in October 2020 and another one just like it was delivered in October 2021. Why Engel presses?
“What’s important to us is process control,” said Plant Manager Ron Hoppa, who has nearly 25 years at Cascade Cart. “Even though we are making a trash can, we want to make sure the trash can we make today is the same trash can we make a year from today and as durable then as it is today.”
Hoppa said the first Engel press with iQ weight control became Cascade Cart’s fastest press and best in terms of part weight consistency. The 96-gallon carts currently run in a 66-second cycle time in a single-cavity mold, but Hoppa believes that can come down to 60 seconds.
Engel’s iQ weight control software automatically adapts the injection profile, switchover point and holding pressure profile to match the material for every shot. That enables Cascade Cart to use more PCR and PCCR despite its inconsistencies.
The second Engel press has recently gone into production and Hoppa said he believes Cascade Cart will invest in more Engel machines in the future.
The company’s machine replacement strategy is evolving. In the past, it maintained machines well and ran them until they died. But that philosophy is changing.
“Technology is changing so quickly,” Miller said. “I think it speaks to the quality you are trying to achieve. Generally speaking, you can get better quality if you have newer machines.”
Cascade Cart primarily uses HDPE. The plant has its own rail spur and material comes in by railcar, truck or sometimes gaylords. There are four silos and resin is pulled from them to a Conair material handling system located on a mezzanine. Different resins, additives and colorants are mixed in blenders on the mezzanine, then the resin goes directly to the molding machines.
Hoppa said automation is important to Cascade Cart, and leadership meets every week to discuss new opportunities. “If we can incorporate more automation into building the cart, we can utilize the labor we have elsewhere,” Hoppa said.
The plant uses robots from Sepro, Reis and Fanuc. Fanuc has become the robot of choice, Hoppa said. “We can save a few seconds in and out of the tool with these Fanucs,” he said.
The plant produces 4,000 to 8,000 carts per day. Thousands of finished carts are stored at the plant in the event a customer needs a quick shipment. Customers generally fall into three groups: large public trash haulers, municipalities and small mom-and-pop haulers.
Carts that come from the mold have wheels and a lift bar attached manually. An operator also adds a radio-frequency identification (RFID) tag that records the entire life of the cart. A photo is taken of the complete cart with RFID tag and that becomes a sort of “birth certificate,” Hoppa said. It is also their poka-yoke system to prevent carts being shipped with errors.
Every cart is tested before it is shipped. The testing weight standard is 3.5 pounds per gallon, so a 96-gallon cart must withstand testing for a load of 336 pounds. Carts are warranted for 10 years.
There is a wheel tester that is basically a rotating drum to simulate a wheel drop. There is also an automated grabber tester and a semi-automatic tipper tester. All the testing equipment, including software, was built in-house.
Cascade Cart has a large oven where carts are tested from 150 degrees Fahrenheit down to minus 40 degrees.
The plant has about 100 employees. Maintaining the workforce for a 24/7 schedule has been a challenge, Hoppa said. Recently it brought in five temporary employees from Texas to Grand Rapids.
Material handlers, die setters and technicians are required to complete self-paced courses from Routsis Training. Hoppa said the plant has a structured system for advancement.
“I’m a prime example of that system,” he said. “I started as a Level A [basic] operator and it was going to be a part-time gig. I progressed to Level B operator then Level C. That’s when you have to decide if you want to go into supervision or technical. I took the technical route to material handling, then die setting and finally process engineering. We want to develop people, so we have a very structured pathway for them.”
Cascade Cart also has a staff social worker who helps people on welfare transition into the company, as well as those who were formerly incarcerated.
The plant uses an enterprise resource planning system from QAD Inc. and also has an enterprise asset management system from IBM to track mold and machine maintenance.
In addition to molding the carts, Cascade Cart can deliver new carts directly to a home and link the cart’s RFID number to the house number.
Cascade Cart’s parent company is a certified B Corp business, which means it balances purpose and profit. B Corps are legally required to consider the impact of their decisions on their workers, customers, suppliers, community and the environment. They undergo audits every two years to measure performance and maintain certification.
Using more recycled material helps Cascade meet its environmental goals.
Ron Shinn, editor
Just the Facts: | |
Company: | Cascade Cart Solutions |
Location: | Grand Rapids, Mich. |
Process: | Injection molding of wheeled trash carts |
Plants: | 1 |
Employees: | 100 |
Parent company: | Cascade Engineering Inc. |
Ron Shinn | Editor
Editor Ron Shinn is a co-founder of Plastics Machinery & Manufacturing and has been covering the plastics industry for more than 35 years. He leads the editorial team, directs coverage and sets the editorial calendar. He also writes features, including the Talking Points column and On the Factory Floor, and covers recycling and sustainability for PMM and Plastics Recycling.
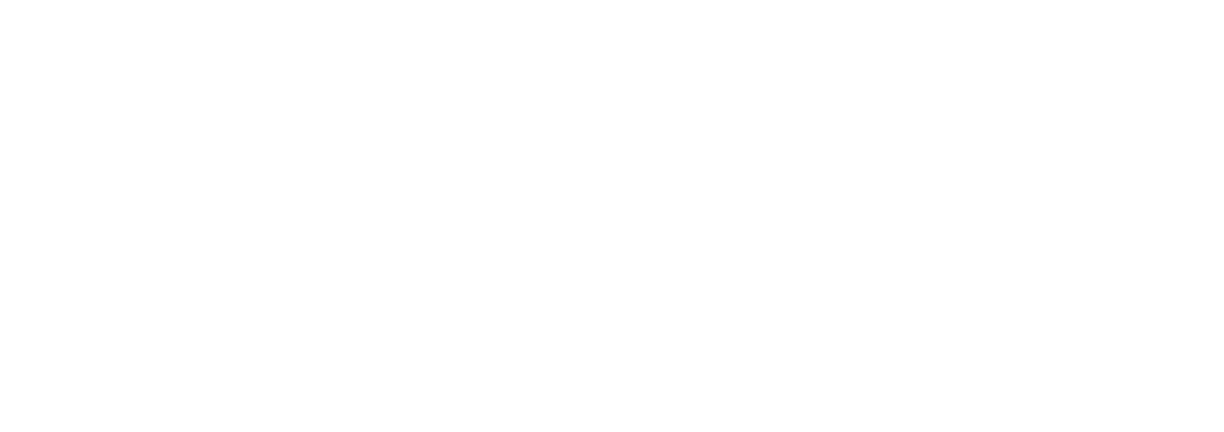