FactoryEye targets U.S. market with analytical software
FactoryEye, a division of Magic Software Enterprises Ltd., has sold its Industry 4.0 cloud-based software to a processor with two plants near Charlotte, N.C.
France’s Aplix Inc. manufactures a range of plastic hook-and-loop fastening systems for personal care products, diapers, packaging and applications in the aircraft, automotive and health care industries. But the company was not fully leveraging operating data from the machines at two of its U.S. production plants near Charlotte. Aplix is using FactoryEye’s eponymous Industry 4.0 cloud-based software to obtain the real-time data and analysis it needs to improve productivity.
“The FactoryEye solution will allow us to connect machine data through our MES [manufacturing execution system] to FactoryEye’s cutting-edge analytics system to provide a whole range of information on critical issues such as machine performance, machine downtime, raw material consumption, traceability, and product quality to help us identify target areas for improvement,” said Pete Connolly, who is responsible for finance and information systems at Aplix.
FactoryEye, based in Or Yehuda, Israel, specifically targeted mid-sized manufacturers with the plug-and-play IIoT solution.
“Up until recently, the only true Industry 4.0 solutions were tailor-made for the largest global manufacturers,” said Nancy Finnegan, VP of sales for FactoryEye North America. “That has now changed. FactoryEye provides mid-sized manufacturers with an attainable way to successfully implement Industry 4.0. We showed Aplix how they can achieve a significant return on investment by looking at machine availability, energy consumption, cycle time, efficiency and quality production.”
“We designed FactoryEye to help mid-sized businesses compete and deliver new performance levels by enabling, connecting, analyzing, and delivering up-to-the-second data for robust, informed decision-making,” said Terri Ghio, president of FactoryEye North America. “FactoryEye is an affordable Industry 4.0 solution for mid-sized manufacturers that transforms data into actionable intelligence and provides visibility from the shop floor to the top floor in real time.”
FactoryEye worked with Aplix to gain a deep understanding of its business processes and provide the platform for it to increase productivity and continually improve manufacturing processes, Ghio said.
At the North Carolina plants, which include injection molding machines and extrusion equipment, process and production data that is collected automatically is put into a key performance indicator format. In addition, shop floor operators can input other operational data manually into tablets. The goal is that within the first 90 days of installation, Aplix will have access to overall equipment effectiveness data that will allow it to start making incremental changes on the factory floor to improve productivity.
In addition, FactoryEye has a certified connector to JD Edwards, which is the enterprise resource planning (ERP) system used by Aplix. This connector and other features of FactoryEye will allow Aplix to capture data that is much more meaningful than what it previously could access, according to the company.
FactoryEye software fully integrates information from all of a company’s IT systems, including its ERP software, MES and systems for warehouse management, supply-chain management, product-lifecycle management and customer-resource management.
FactoryEye can help mid-sized plastics processors more fully embrace Industry 4.0, Finnegan said.
“When Industry 4.0 kept coming up in the market, and people kept talking about it, we realized the real gap was in mid-size manufacturing, and especially in plastics injection molding, because they are organizations that are capital intensive, obviously, because of the cost of the molds and machinery,” Finnegan said. “It would be a lot of risk for many mid-sized manufacturers to stop what they were doing and try to put in new technology.
“What we saw in the market was they had done bits and pieces of it. They had tried some integration … as people were buying new machinery, there were certainly more opportunities to get data out of that machinery, but what we see all the time is it’s very difficult for them to pull all of that information together.”
One of the key benefits of FactoryEye is helping users adopt more preventive maintenance, which reduces unexpected equipment downtimes and maximizes worker efficiency at a time when companies are facing a combination of a general labor shortage and a shortage of skilled labor.
“It really is all about preventive maintenance in many ways,” Finnegan said. “If they can start to not only get off of entering manual data on the production floor, which is great, but if they can start to understand where that production downtime may be coming from and how to prevent it, that is an absolute game-changer.”
If a company knows, for example, that it may be time to replace a bearing, it can schedule the maintenance and decrease the downtime from perhaps five days to only a few hours, Finnegan said.
FactoryEye software can pull data off manufacturing equipment PLCs for monitoring and analysis, and customers can install sensors on older equipment that might not be equipped with modern sensors.
“We have a very strong partnership with a sensor device [manufacturer],” Finnegan said. “That sensor device can measure sounds, temperature, vibration, etc. For older machines out there in the market, we can hook in this device.”
The sensors can transmit data over either a cell phone connection or Wi-Fi. They can be attached to chillers, hoppers and other auxiliary equipment.
“That’s an opportunity where we can start to understand exactly what’s going on with that machine,” Finnegan said.
In addition to collecting and transmitting data that can be reviewed on tablets, personal computers, cell phones or tablets installed on the production floor, alerts or push notifications can be sent to a machine operator or supervisor when an anomaly is identified. It can alert personnel to a machine operating outside of normal parameters that could indicate a maintenance issue or other reason for loss of production.
FactoryEye can be deployed within hours and features tight cloud security in which all communications are encrypted before being uploaded to the company’s servers, according to the company.
Contact:
FactoryEye North America, a division of Magic Software, Laguna Hills, Calif., 949-250-1718, www.magicsoftware.com/factoryeye
Bruce Geiselman
Senior Staff Reporter Bruce Geiselman covers extrusion, blow molding, additive manufacturing, automation and end markets including automotive and packaging. He also writes features, including In Other Words and Problem Solved, for Plastics Machinery & Manufacturing, Plastics Recycling and The Journal of Blow Molding. He has extensive experience in daily and magazine journalism.
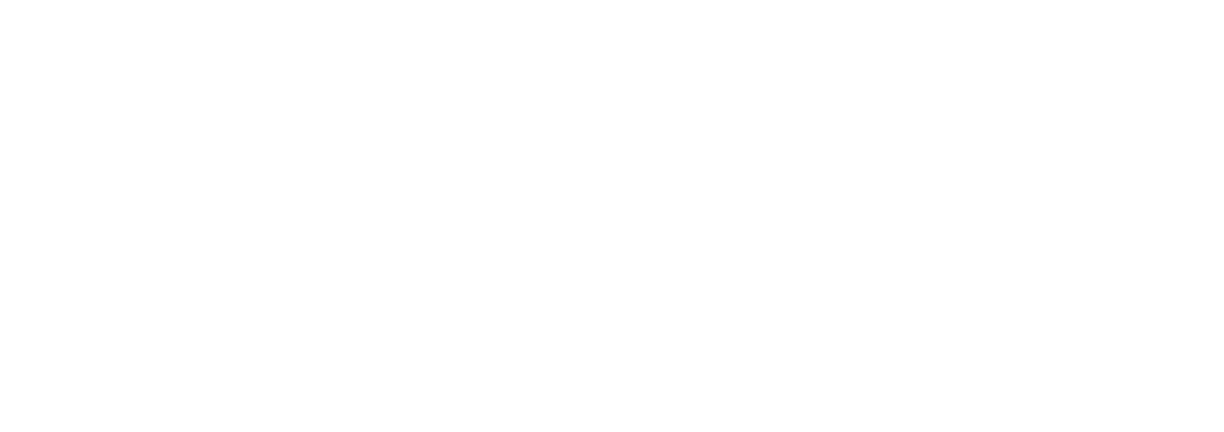