In my career working at Wittmann Battenfeld in our service, engineering and sales departments, the question of central vs. beside-the-press material handling has come up numerous times. This consideration is important not only to greenfield facilities, but also to facilities that are expanding, or looking for a more efficient process.
To help our customers, I came up with a list of priorities that will start an open discussion when implementing material handling equipment. Spoiler alert: Neither one is better than the other. It all depends on your priorities and goals.
Before we can compare the two, we need to understand what these two systems are.
A central system typically uses one or more vacuum pumps to deliver material to several molding machines via a common line orThese systems can also be hybrid. An example is a central conveying system that is used to convey material to beside-the-press dryers.
Below are some considerations that should be made when deciding between central and beside-the-press systems. This list is by no means comprehensive; however, these are the topics that have come up most often in my experience in service and sales.
Existing Equipment
When evaluating existing equipment, we need to take into consideration the type of system currently used, the age and reliability of the current equipment, and whether it would be beneficial to incorporate some of the existing equipment into the new systems. In central systems, components like the piping, pumps and even the receivers sometimes can be reused.
Floor Space
Floor space is a valuable resource. With the rising cost of commercial real estate, molders are looking for ways to fit more machines into smallerOther space-saving options include utilizing mezzanines. The mezzanine can house the drying and conveying system while leaving room for material sources such as gaylords and surge bins below.
Cost
Generally, the upfront cost of a central system is much higher than that of beside-the-press equipment. This is due to the upfront cost of purchasing tubing, pumps, battery dryers, hoppers and coupling stations. However, the cost of beside-the-press systems can exceed the cost of central systems in the long run depending on system size.
When making a decision based on cost, here are some things to consider:
- The size of the molding operation, as generally larger facilities gain more advantage with a central system
- The number of materials used, which can take more planning in a central system. One of the most important questions is, “How many materials need to be used at one time?” Drying hoppers or other material source locations can be designated for several small, infrequently used materials.
- Potential costs saved from being able to purchase materials in bulk quantities, such as by railcar or truck, and then storing those materials in silos.
- The available capital to purchase the equipment .
In beside-the-press applications, each press has its own means to convey material. This means using an integral loader that has its own motor or Venturi loader, which uses compressed air to load machines and drying hoppers. A central conveying system uses one or more vacuum pumps, each conveying material to several destinations. Although these central pumps are much larger, they are more efficient than smaller motors, and they start and stop less frequently.
This also applies to central drying, as you will have fewer blowers and heaters in the system.
One of the main questions that molders often bring up about central drying is, “If the system is not operating at full capacity, are you wasting energy?” Today’s central drying systems, such as Wittmann Battenfeld’s FC Plus system, use variable-frequency drives and smart flow valves. The intelligent processor in the drying hoppers monitors the return air temperature and adjusts the airflow-control valve. The dryer constantly monitors the differential pressure between the air-supply and return lines and slows the blower down, if needed. This allows drying systems to be slightly oversized to handle periods of high demand.
There have been a lot of improvements in portable dryer energy consumption, as well. Wittmann Battenfeld’s Aton dryer line uses technology, such as ECO mode, that will index the wheel instead of continuously running at times of reduced throughput or reduced moisture content in the resin. This allows the dryer to reduce the regeneration temperature without compromising quality. This has resulted in significant energy savings.
The risk of dried materials re-absorbing moisture increases the further the material has to travel. This can be an issue in central systems that are improperly designed or maintained. Using purge valves, dry air conveying and proper balancing, the central system can decrease the risk of moisture regain.
Even though the issue is more prevalent in central drying systems, moisture regain can be an issue with portable dryers, as well. This often happens when material hoses are too long or purge times are not set properly, or there is too much material in the vacuum receiver on the throat of the machine.
Blending
If possible, central blending should be avoided. Material that is blended far away from the machine can experience separation. This is caused by variables such as different bulk densities, pellet geometry and static electricity. If floor space is a concern, blenders and feeders can be mounted directly on the throat of the machine.
Inventory Management
One advantage with central systems is inventory management.
By design, central systems have one source feeding multiple machines. This allows molders to have fewer open containers of the same material, decreasing the amount of partially used containers being placed back in the warehouse.
Central systems also afford a better opportunity to utilize silos that can be filled by truck or railcar. This can result in significant cost savings.
Traceability
Today’s central system controllers, such as Wittmann Battenfeld’s M7.3, add the ability to track lot numbers. This is becoming more common not only in the medical industry but other industries, as well.
Mold Change Time (with material changes)
With a central system and a coupling station, materials can be staged for future jobs, which is especially advantageous with dried materials. When a operator needs to change materials, he or she can simply change the position of the quick disconnect on the coupling station.
Industry 4.0 Capability
Beside-the-press systems allow for Industry 4.0 integration, facilitating communication among peripherals such as temperature-control units, blenders, dryers and robots. With Wittmann Battenfeld’s 4.0 work cells, this allows for some powerful features, including Smart Machine, Smart Work cell, Smart Production and Smart Service.
Redundancy has always been a big concern in deciding between beside-the-press or central systems. Central systems have pumps and dryers, which serve multiple machines at the same time. By design, beside-the-press systems have a distinct advantage over central systems when it comes to redundancy. This is due to the fact that each molding machine has its own conveying and drying system. A failure in a beside-the-press system usually results in the shutdown of one machine, rather than multiple machines.
When designing a central system, it is highly recommended to incorporate redundancies (spare pumps, spare filters, spare dryers, etc.) to minimize downtime caused by equipment failure or planned maintenance.
Clean Rooms
Due to exhaust from integral loaders and dryers, placing portable equipment in a clean room is not a desired practice. In this situation, it is best to use a central system and place the central pumps and filters outside the clean room. Alternatively, portable drying/conveying equipment, such as Wittmann Battenfeld’s ATON VS systems, can be placed outside the clean room and then piped into the clean room through the bulkhead.
Human Error
Let’s face it, mistakes happen. All of us have experienced materials being dried at improper temperatures, and even being conveyed to the wrong press. One common misconception about central systems is that it is easier to make mistakes due to the remoteness of the equipment. However, Wittmann Battenfeld has several options that can significantly reduce human error.
- RFID-coded coupling stations use RFID technology to prevent a tube from being connected to the incorrect source.
- Wittmann Battenfeld’s optional Coded Material Source software feature requires that material handlers scan the material bin with a bar-code scanner to verify that the material matches the M7 control systems stored database.
- Remote alarms can be installed to inform personnel outside of the material room of a problem or a material shortage.
- VNC connections can be used to remotely monitor the control system from inside the plant or anywhere in the world.
Expansion Flexibility
Both beside-the-press and central systems have advantages when it comes to expansion.
With the beside-the-press system, molders can simply order an additional dryer and integral loader for new work cells. Expanding a central system can be just as easy and, in some cases, even easier. A lot of our customers have us design their material handling systems around future expansion; when a new molding machine is added, expanding the conveying and drying system is quick and easy.
With the vast differences between molders today, one cannot simply say that one system is better than the other. The best decision always comes down to what your goals are and how you prioritize.
Beside-the-press systems offer: | Central systems offer: |
Faster ROI | Lower cost in the long run |
Greater flexibility | Greater energy efficiency |
4.0 Integration | Less need for production floor space |
Greater redundancy | Easier material management |
Less chance of moisture regain | Faster material change times |
Jonathan Fowler is an inside sales manager — material handling and auxiliaries for Wittmann Battenfeld. After spending 10 years in the U.S. Navy as an auxiliary technician and instructor, he joined Wittmann Battenfeld as a service technician. He spent three years installing, starting up and training customers on material handling systems. He then moved into sales and system design, working for six years with material handling systems.
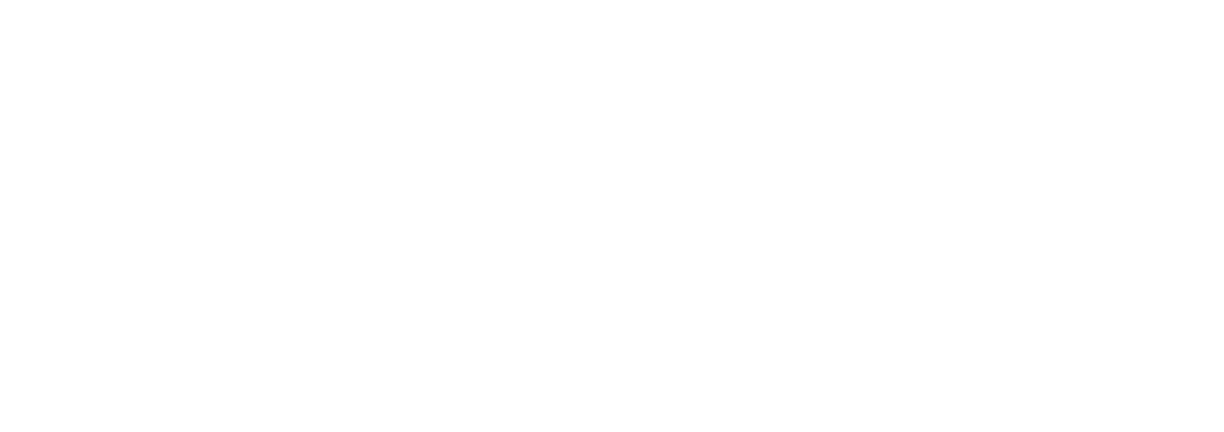