Remote-monitoring capabilities keep workers at safe distance
By Karen Hanna
Remote-monitoring systems are helping OEMs finding ways to boost productivity, reduce repetitive-risk injuries and, in this pandemic era, break the chain of transmission.
Arburg and Milacron, for example, both reported using Industry 4.0 and remote-monitoring solutions now more than ever to help their customers.
“If there is anything positive that we can take from the coronavirus pandemic, it is that it has propelled digitalization to the forefront of our operations,” said Gerhard Böhm, managing director of sales at Arburg.
Milacron’s M-Powered suite of customer-support services leverages Industrial Internet of Things (IIoT) technology and data from real-time machine learning to monitor equipment and send alerts, when appropriate.
“Nearly two in five issues can be resolved remotely, and there’s usually a smaller window of time needed to troubleshoot prior to a technician coming to the customer’s facility to intervene or repair the problem,” said Eddie Jump, digital analytics leader for the M-Powered business unit.
He said the company last year connected the same number of machines to M-Powered services as in 2019, but at a faster pace, owing to the four-month shutdown in operations it endured at the start of pandemic.
And Milacron’s customers continue to invest in the technologies, said Ron Gulbransen, a technical product manager for auxiliaries for the company.
“Some customers had some delays but are following through with their previous initiatives to become smarter or create smart factories. Using predictive analytics or monitoring downtime instances have become useful as some manufacturers are experiencing bottlenecks in production needs when compared to capacity,” Gulbransen said.
In addition, he said the company has conducted a record number of robot installations over the past year.
Karen Hanna, associate editor
Contact:
Arburg Inc., Rocky Hill, Conn., 860-667-6500, www.arburg.com
Milacron Plastics Machinery America, Batavia, Ohio, 513-536-2000, www.milacron.comKaren Hanna | Senior Staff Reporter
Senior Staff Reporter Karen Hanna covers injection molding, molds and tooling, processors, workforce and other topics, and writes features including In Other Words and Problem Solved for Plastics Machinery & Manufacturing, Plastics Recycling and The Journal of Blow Molding. She has more than 15 years of experience in daily and magazine journalism.
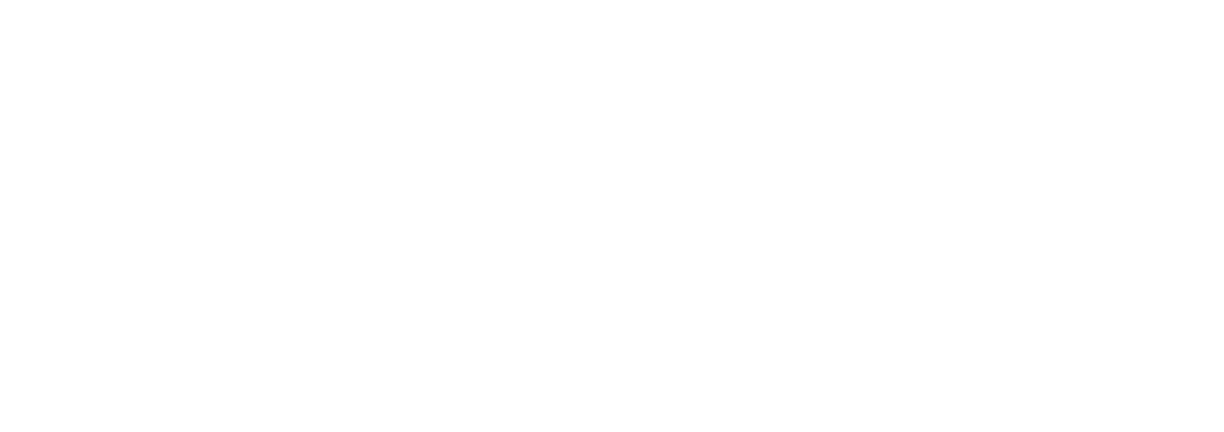