COVID brings worker safety and health into focus
Protecting workers means doing the fundamentals, such as maintaining machine-guarding around pinch points, creating traffic flows that head off possible collisions and providing safety goggles and gloves.
OSHA standards provide a basic template, but, as the pandemic has shown, risk mitigation is ever-evolving.
“I think COVID has taught a couple of lessons that need to be expanded into other areas. One is a narrow focus on your next safety improvement,” said Terry Mathis, who provides health and safety-related consulting services to workplaces.
“You can only think of a certain number of things at a time, and, when you add a major thing like COVID and say, ‘OK, go out there and do your job. Be careful not to get hurt like you’ve always done, but, in addition to that, make sure you don’t catch this awful virus.’ … We’re just spreading people’s attention thinner,” said Mathis, the founder and CEO of ProAct Safety consultants.
It’s a matter of priorities.
Mathis’ Texas firm has worked with companies for almost 30 years on more than 2,000 projects designed to protect employees. He said too many companies rely on employees knowing all the safety rules, both big and small, rather than knowing the logic behind them or putting their attention on the most likely — and most severe — risks.
He tells companies: “You don’t need to do more. You need to do better.”
Maintaining a good flow
When it comes to the COVID-19 pandemic, consultants and experts stress both individual behavior — physical spacing, masks, hand-washing and personal protective equipment — and a companywide approach. Recommendations from OSHA’s COVID-19 Guidance for the Manufacturing Industrial Workforce include: encouraging workers to stay home if they’re sick; establishing staggered shifts; discouraging the shared use of tools; and temporarily moving or repositioning workstations to create more distance or installing barriers between workstations, if necessary.
In manufacturing spaces, where a few operators might be well-spaced between work cells, it’s the enclosed, non-production areas that represent the highest risk of transmission. Dony singled out areas like restrooms, break rooms and meeting spaces.
“Organizations can mitigate this risk in a variety of ways, including limiting capacity, creating one-way traffic routes in highly used areas, reutilizing existing space to serve the same purpose as high-congregation space (e.g. redesignating a meeting room as a secondary break room, etc.),” Dony said.
Subodh Sharma, the founder and CEO of Oak Tree Engineering, which specializes in designing plastics plants, emphasized the importance of airflow, especially in the construction of new plants.
“The biggest thing you can do is look at airflow. … We look at the normal wind direction in the climate of the area and try to orient the plant in such a way that the airflow is streamlined with the plant process flow,” Sharma said. “If the intake wall of the plant is toward where the air is coming from for most of the time and the outlet is on the other end, that helps.”
State standards vary, but Sharma said he used to advise clients that their facilities should exchange air at least six to eight times an hour. Eight to 10 times an hour was average, but COVID has upped the stakes, and Sharma now recommends 10 to 15 air exchanges per hour.
Improving or replacing air-conditioning systems is one possible strategy.
“There are better airflow and air exchanges per hour,” Sharma said. “There are other low-cost solutions, for example, rooftop ventilators. They can be wind-driven. You don’t need any power. They can be fans.”
Dony cautioned that buyers should vet claims made in recent months regarding technologies, such as filtering systems, that have been specifically marketed to mitigate the risk of disease transmission.
“Many of these technologies do have prior use in hospital or food manufacturing environments and have been proven effective for mitigating certain types of infectious disease transmission. However, there has not been wide, scientifically validated study of these sorts of systems with respect to COVID-19,” he said. “That said, the basic principles of these systems (filtering, UV, etc.) would seem to prove effective in combating viral transmission, if the proper ones are put into place.”
If a worker tests positive for COVID, Dony suggested employers ensure contact tracing within the plant, and test those exposed.
“In many cases, the best risk mitigation would indeed be temporary suspension of work and deep cleaning both from a material-risk-mitigation perspective, as well as from a ‘doing-right-by-your-people' perspective,” he said.
Taking it all in
Too many companies put equal attention on 100 percent of possible risks — meaning employees don’t know what is most dangerous, Mathis said. He’s s a proponent of the 80/20 principle — the idea that 80 percent of outcomes result from 20 percent of possible causes
“I think everybody’s trying to push the mountain 2 inches, and what they need to be doing is taking scoops out of one side and hauling them around to the other side. You know the old saying: The way you eat an elephant is a bite at a time. The biggest mistake I see my clients making right now is trying to do too much at once.”
ProAct Safety serves companies that want to move beyond the basics, such as OSHA compliance. Mathis said four factors are vital in its work: company leadership that is committed to worker safety and health; an appropriate company culture; employee engagement; and data — including accident reports — that provides sufficient detail to illuminate possible changes.
In getting started, data can provide a roadmap.
Plastics processors wanting to improve the health and safety of workers should start by identifying the hazards in their work environment, said Bruce Main, the president of Design Safety Engineering.
A Michigan company that offers risk-assessment consulting and training services, Design Safety Engineering begins its process with a risk assessment. At this stage, the employer needs to examine the work environment and identify potential sources of harm.
“Basically, when you look at your plant, you want to say, ‘What do my people need to do, and where are the potential hazards where they could get hurt?” Main said. “That starts you on the risk-assessment process. Once you’ve identified the hazards, then processors need to look at a variety of risk-reduction measures that are appropriate.”
Sometimes, processors can find published standards that apply, and other times they need to use common sense to determine a feasible risk-reduction measure, Main said.
Typically, Main said his clients have gotten what they can out of HR initiatives and safety meetings. They want to know what to do next.
That takes strategizing.
“Even companies that are very strategic-thinking aren’t unified-strategic-thinking. They have one strategy for running the company and another strategy for running the safety program, and, more often than not, those two strategies compete and conflict with each other,” Mathis said. “They put their workers in a dichotomy out there: ‘Do I do the job the most productive and profitable way, or do I do it the safest way?’ And they actually have, a lot of times, two bosses, one coming around telling them to be more productive and another coming around to tell them to slow down and be safe. Which one wins almost always? The guy that can give them the raises. And that’s the productive part. Production trumps safety 99 times out of 100, if they conflict with each other.
“The trick isn’t to make safety a higher priority. The trick is to get the two strategies together and aligned with each other.”
Winds of change
Progress can come in stages, when safety and production goals collide.
When he began working in the blow molding industry more than 50 years ago, Dave Calderone remembers a heavy stench that saturated his clothing and skin. In the evenings, his wife would complain about the smell. But he used to joke that it smelled like money. A plant manager by the age of 25, he’s now the president of Alternative 4 Plastics LLC, a business coaching and consulting firm that serves blow molders.
“There was always an odor or smell that came off the resin as we extruded it in the late ’60s and ’70s,” Calderone said. “Nobody really thought it was harmful. We never really did much about it. We just let it go, and if the plant was running vinyl, the whole plant smelled like vinyl.”
Companies began making changes in the 1980s when people started realizing that those odors could be harmful and OSHA began establishing worker safety standards. First, plants installed vacuum hoods over extruders when necessary; now, at newer plants, air handlers bring in more air from the outside, which reduces the need for hood vents.
“They’re much more aware today than they were in the late ’60s,” Calderone said.
Even now, though, companies that run only a few machines or process small volumes of plastic might experience low levels of allowable off-gassing, Main said.
While those fumes might not pose a direct health risk, employers might choose to install vents over extruders or take other measures to improve ventilation.
“Maybe it doesn’t reach a level that would require ventilation, but you might decide that to make a safe and healthful workplace, or to enable your employees to work faster and safer and more comfortably, it is worthwhile,” Main said.
Monitoring day-to-day details
“The one thing about [plastics] industry is that you get either a little cut on your finger or you lose your finger,” he said. “There’s no kind of middle of the road for somebody to get hurt.”
Consultants can help companies identify risks, determine OSHA compliance and figure out solutions to keep workers safe.
Ted Sberna Sr. is the lead engineer and chief consultant with White Horse Safety. He and Main both said their respective consulting firms spend a lot of their time helping companies deal with hazardous energy.
For example, injection molding machines can cause crushing injuries when people are working in the mold clamping area. Processors need to ensure equipment and workers comply with OSHA requirements for lockout/tagout safety procedures to prevent machines from starting or moving while workers are in an area where they might be injured.
Most injection molding machines manufactured within the past three to four years have safety control circuits designed with redundancies that can prevent parts from moving during service or repair. However, older machines typically don’t come with such circuits, and companies often don’t understand how to use them to protect workers.
“This is a really big obstacle for these end users to overcome,” Sberna said. “It’s very difficult for them to sort through the nuances of evaluating equipment, preparing proper documentation and making sure the machines are set up to do that. They don’t have the internal resources that have time and the understanding on how to do this.”
White Horse Safety trains processors on alternative methods of controlling hazardous energy and can review designs for or field-test systems, such as control circuits, to validate that they work properly, Sberna said.
Other risks run the gamut, though Mathis said most companies experience some variation of the same kinds of threats — pinch points, collisions and injured backs caused by poor-form lifting.
Main ticked off some other areas of concern.
“When you’ve got heated plastics, you’ve got hot surfaces,” Main said. “You’ve got slip-and-fall [hazards] if some of the material gets on the floor. Dusts are concerns. Often, there are traffic hazards.”
Storing and moving materials could present other issues.
“You get material-handling issues, and that gets you into fork-truck traffic typically, unless you have a pneumatic conveying system,” he said.
Protecting workers from forklifts could involve marked pedestrian walkways or a physical barrier to separate vehicles and people. Convex mirrors can help workers see around blind corners. Awareness indicators, such as lights that shine forward and aft of the fork truck, can reduce collisions. Safety education for forklift drivers and pedestrians also can be key, as well as requiring workers to wear high-visibility safety vests.
Safety in focus
With more than half a century in the business, Calderone has seen firsthand that things are getting better.
In addition to progress on other fronts, a gradual adoption of all-electric machines is expected to improve safety within blow molding plants, Calderone said.
“It helps because you don’t have hydraulic oil leaks to worry about,” he said. Such leaks can cause falls.
More generally, equipment has become safer with improved lockout/tagout systems and the introduction of light curtains that better protect workers from moving machinery.
“Some of the very large equipment have light curtains so if you break the light curtain, the machine will kick off, and they’re usually 4 to 5 feet away from the machine,” Calderone said.
The smell of money doesn’t have to take precedence over workers’ needs for a safe and healthful environment.
“I think that a lot of companies have started to realize: ‘Hey, we need to pay more attention to this. We need to make their job easier. We need to make it safer. We need them to be happy when they come to work,’ ” Calderone said.
Bruce Geiselman, senior staff reporter
Karen Hanna, associate editor
Contact:
Alternative 4 Plastics LLC, Murfreesboro, Tenn., 615-785-4226, https://alternative4plasticsllc.com
Design Safety Engineering Inc., Ann Arbor, Mich., 734-483-2033, www.designsafe.com
National Safety Council, Itasca, Ill., 630-285-1121, www.nsc.org
Oak Tree Engineering LLC, Monroe, Mich., 734-244-5231, www.oaktreellc.com
OSHA, Washington, D.C., 800-321-6742, www.osha.gov
ProAct Safety, The Woodlands, Texas, 936-273-8700, https://proactsafety.com
White Horse Safety Inc., Georgetown, Ky., 859-333-5875, https://whitehorsesafety.com
Safe and sound
Find additional and expanded stories about keeping your plant safe and your workers healthy on our website:
- OEMs and clients are growing more comfortable with remote commissioning of machines around the world. plasticsmachinerymanufacturing.com/21207371
- Officials at Design Safety Engineering and White Horse Safety evaluate machinery and plant practices, and assess risks. plasticsmachinerymanufacturing.com/21207831
- Signage reminds workers of safe practices and social distancing during the pandemic. plasticsmachinerymanufacturing.com/21207817
- Consultant Dave Calderone uses his more than 50 years’ experience working in plastics processing to provide blow molders with training seminars, technical consulting services and management. plasticsmachinerymanufacturing.com/21207857
- Autonomous mobile robots are improving worker safety at plastics plants by replacing manually operated forklifts in high-traffic areas. plasticsmachinerymanufacturing.com/21207830
- Arburg and Milacron report increased interest in and use of their remote monitoring and maintenance capabilities. https://plasticsmachinerymanufacturing.com/21207739
Bruce Geiselman
Senior Staff Reporter Bruce Geiselman covers extrusion, blow molding, additive manufacturing, automation and end markets including automotive and packaging. He also writes features, including In Other Words and Problem Solved, for Plastics Machinery & Manufacturing, Plastics Recycling and The Journal of Blow Molding. He has extensive experience in daily and magazine journalism.
Karen Hanna | Senior Staff Reporter
Senior Staff Reporter Karen Hanna covers injection molding, molds and tooling, processors, workforce and other topics, and writes features including In Other Words and Problem Solved for Plastics Machinery & Manufacturing, Plastics Recycling and The Journal of Blow Molding. She has more than 15 years of experience in daily and magazine journalism.
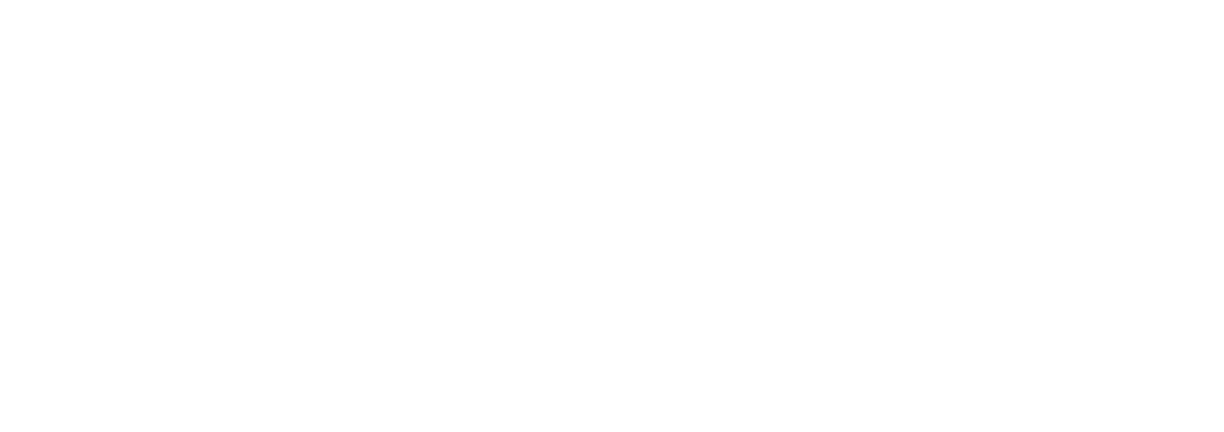