By Karen Hanna
A new series of electric injection molding machines offers a raft of features that improve usability and efficiency.
Available through Maruka, the Si-6s line from Toyo Machinery & Metal Co. Ltd., Akashi, Japan, offers presses ranging in clamping forces from 55 tons to 1,050 tons. Features include systems to curb waste during material changeovers, and to more efficiently and accurately set up the presses. The presses also boast a control system designed to be used in a manner similar to a smartphone. Additionally, users can opt for a system for monitoring and adjusting melt parameters.
Kevin Bruce, VP of sales for the plastics injection molding division for Maruka, which distributes Toyo presses in the U.S., Mexico and Canada, touted the series’ Auto Purge function, which Toyo characterized as an improvement over other presses’ purging procedures.
While other presses with an auto-purge function automatically build up a full shot and purge it out over a prescribed number of injections, the Toyo presses add motion to the screw to rid themselves of the material that’s being purged. During a material or color changeover, the screw moves rapidly clockwise and counterclockwise, almost like a washing machine, cutting in half the time and material necessary to complete the changeover. This movement is so effective users don’t need to pull the machine’s screw to clean it.
“This reversing motion of the screw scrubs the material off the screw, making for a 50 percent quicker material change while using 50 percent less material. It is also being used by customers to get rid of black specs in their parts,” Bruce said. “That means 50 percent less material waste being introduced into the environment, and the material savings go immediately to our customer’s bottom line.”
Other new features on the Si-6s presses include Fill Only, the System800 control and Meltcon.
Fill Only takes the guesswork out of machine setup, overseeing first-stage filling prior to running parts. It’s designed so that operators can simply enter the number of cycles and turn the machine on, without having to enter hold pressure or time parameters.
“They turn this feature on at the beginning of a run. It checks to make sure it has the correct first stage fill over a selected number of cycles,” Bruce said.
After performing the set number of first-stage filling cycles needed for setup, the machine automatically switches over to the parameters required for part manufacturing. The screw is held steady throughout the Fill Only verification.
Designed for smartphone-like operation, the System800 control responds to gestures, like pinching, swiping, dragging and dropping. Users also can input handwritten notes, and upload videos, training documents, or PDFs showing information from machine manuals or part drawings. Users need no special software to input their own machine sequences, which the control automatically checks for safety.
Available as an option, Meltcon automatically adjusts temperatures within specific ranges in order to keep melt viscosity within certain parameters. This eliminates the possibility for part variations due to material lot changes and improves repeatability.
The machines can be equipped with standard, high-pressure, high-speed and ultra-high-speed injection units. They have an open-access design that allows easy accessibility to the mold and ejectors.
Karen Hanna, associate editor
Contact:
Maruka USA Inc., Lee’s Summit, Mo., 816-524-1811, www.marukausa.com
Karen Hanna | Senior Staff Reporter
Senior Staff Reporter Karen Hanna covers injection molding, molds and tooling, processors, workforce and other topics, and writes features including In Other Words and Problem Solved for Plastics Machinery & Manufacturing, Plastics Recycling and The Journal of Blow Molding. She has more than 15 years of experience in daily and magazine journalism.
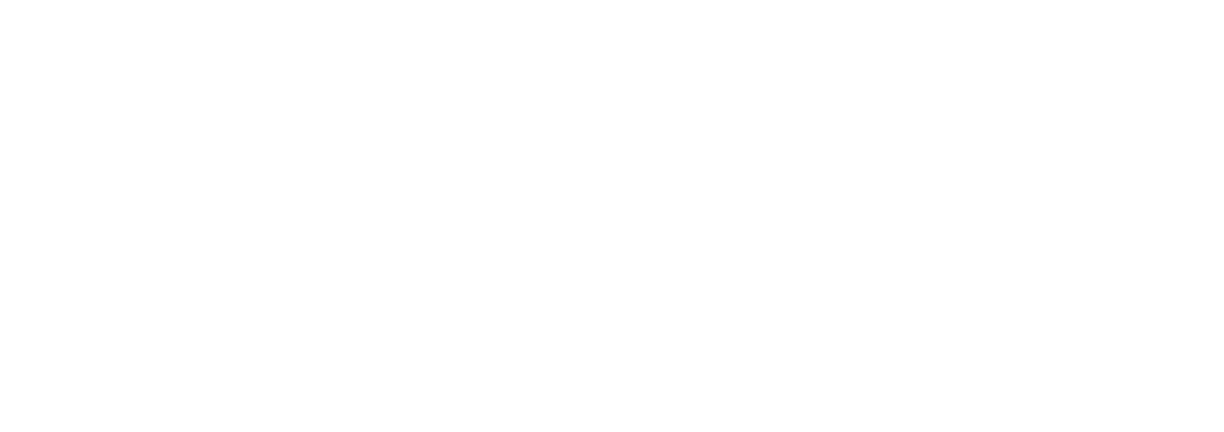