Mobile robots are starting to appear in plastics processing plants, generally to replace forklifts that move similar payloads to and from the same places over and over during a day. But what’s a robot to do if the payload, pickup or drop-off heights change, or it needs help in transferring the payload?
Until now, those could be limiting factors for using the robot. Available solutions involved adding more traffic to the plant’s busy Wi-Fi network to help the robot navigate.
Danish mobile robotic equipment manufacturer ROEQ has unveiled a suite of sensor-based add-ons for Mobile Industrial Robots (MiR) models that shun the Wi-Fi network.
The new ROEQ products are designed for the MiR250, MiR500 and MiR1000 models when equipped with ROEQ’s top roller system.
The first new products are GuardCom and GuardCom Connect, which enable the robot to connect to conveyor stations. GuardCom is installed on a stationary conveyor station and GuardCom Connect goes onto the autonomous mobile robot. Once the mobile robot arrives at the conveyor, GuardCom signals to the conveyor that the robot is ready to receive or deliver a package. When the transfer is complete, both units are signaled so the robot can leave.
GuardCom works on any conveyor system and replaces third-party wireless connections. Multiple GuardCom Connects can work with the same GuardCom and vice versa, according to ROEQ. The company said the new system eliminates wait times, errors and accidents at cargo transfer points.
The connection between the GuardCom and mobile robot is wireless. GuardCom includes a barrier for the conveyor that goes up when the robot is not ready to receive a load.
Scott Albrecht, VP of advanced control technologies at Hartfiel Automation, which distributes ROEQ products in the U.S., said the GuardCom products could change the way robots are used in manufacturing plants.
“In the past, significant engineering development and third-party hardware was required to manage moving material from a stationary conveyor onto a mobile robot, which added substantial cost and time to deployments,” Albrecht said.
Other new products are the ROEQ TR500 Auto and TR1000 Auto roller modules with automatic lifting mechanisms. These are designed for the larger MiR models that can move up to a 2,200-pound payload. The TR modules automatically adjust the height of the robot platform to pick up or drop off at different heights. The platform height range is 21.5 inches to 31.3 inches from floor to rollers.
The final new products are the TR125 Manual 250 and TR125 Auto 250 rollers, which are compatible with MiR’s newest robot, the MiR250.
Ron Shinn, editor
Contact:
Hartfiel Automation, Eden Prairie, Minn., 800-331-7301, www.hartfiel.com
Ron Shinn | Editor
Editor Ron Shinn is a co-founder of Plastics Machinery & Manufacturing and has been covering the plastics industry for more than 35 years. He leads the editorial team, directs coverage and sets the editorial calendar. He also writes features, including the Talking Points column and On the Factory Floor, and covers recycling and sustainability for PMM and Plastics Recycling.
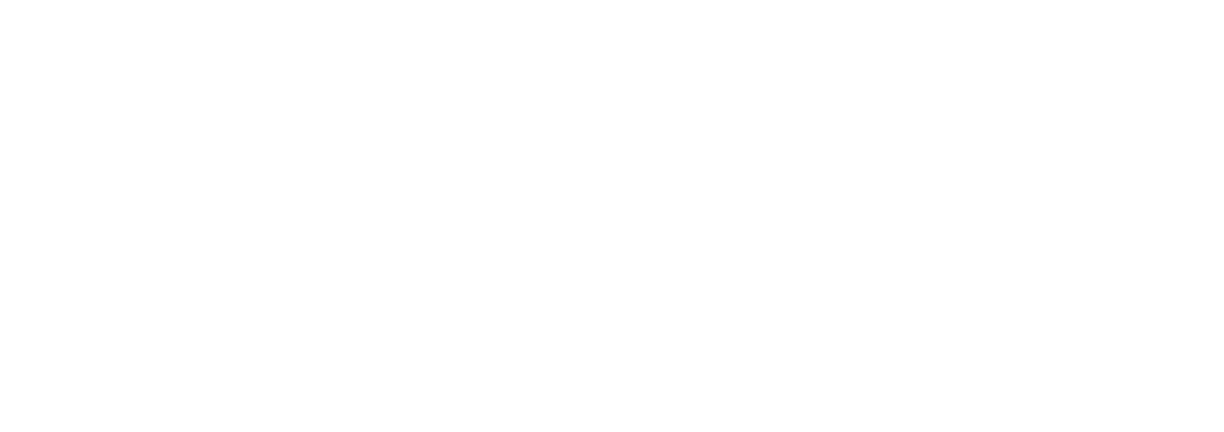