Helmar Franz may have sold more injection molding machines than anyone else on the planet, and he had a hand in designing some of them. I thought about something Franz once told me while I was reading our excellent series on Pages 7-16 about the importance of good maintenance to make processing machines last longer.
Franz believed that it was important for an operator to have a special pride and connection with his or her injection molding machine. If that connection existed, the operator took extra efforts to make sure it was clean, well-maintained and operating better than any other molding machine in the plant.
Franz, now chairman of the strategy development committee for Haitian International Holdings Ltd., the world’s biggest manufacturer of injection molding machines, has 48 years in the plastics industry. He has sold injection molding machines all over the world. Just out of college, he led an East German team that developed the world’s first two-platen molding machine.
Haitian sold more than 32,000 injection molding machines last year.
Franz may have been recalling the days when there was one operator for each machine. Nowadays it is not unusual to see two operators on duty running 24 molding machines.
Our stories include information on maintenance software and built-in controller functions that help with scheduled maintenance. In the past, we also have written about wearable sensors that alert operators when a machine is not running up to standards.
But the human element cannot be eliminated, no matter how much we would like for it to be. Keeping a machine clean and properly maintained takes dedication. Paying attention to how it is running, the sounds it makes, and its operating speed are also important. The operators and plant floor technicians cannot depend entirely on the maintenance team to come around periodically and take care of this task.
Reading about machine maintenance is certainly not as exciting as reading about the bells and whistles on the newest presses or extruders. But good maintenance practices on the plant floor go directly to the company’s bottom line.
Companies that sell new processing machines recognize that and generally include maintenance training with every sale.
A couple years ago, I visited an injection molding company that was running 32 presses that averaged more than 15 years old. Most of them had been purchased used and rebuilt with new controllers and other features that matched the machines to the specific parts they were molding. The strategy worked because the plant had an extensive maintenance program that almost never saw a machine malfunction.
That strategy won’t work for every product, but you don’t necessarily need all those bells and whistles for every product. But you do need a good maintenance program, good training and good people to make it work.
Ron Shinn | Editor
Editor Ron Shinn is a co-founder of Plastics Machinery & Manufacturing and has been covering the plastics industry for more than 35 years. He leads the editorial team, directs coverage and sets the editorial calendar. He also writes features, including the Talking Points column and On the Factory Floor, and covers recycling and sustainability for PMM and Plastics Recycling.
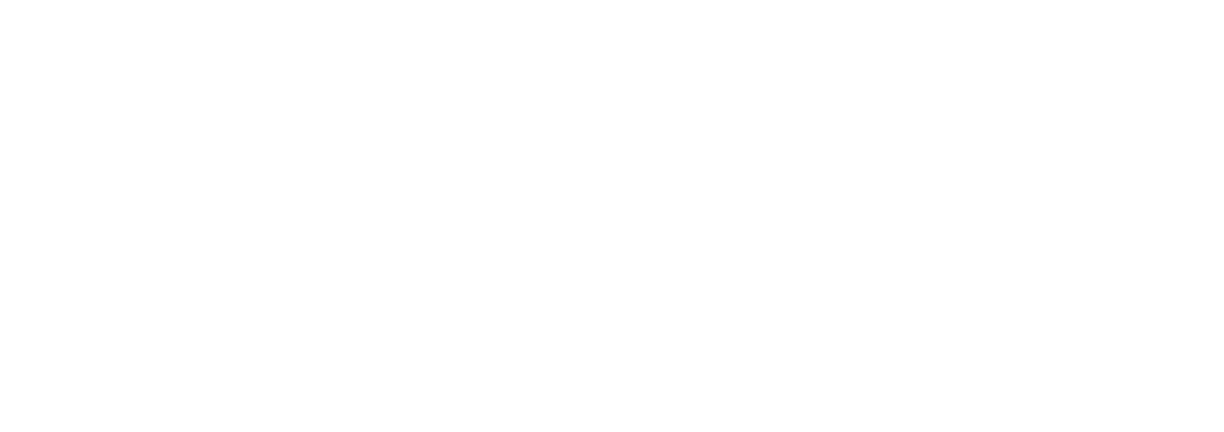