By Bruce Geiselman
Matrix Tool, established 48 years ago as a custom full-service injection molding business, has evolved to specialize in the design and construction of micro and high-precision plastic injection and metal injection molds. It also produces micro and tight-tolerance plastic injection molded components.
“In some respects, our involvement in micromolding was a natural progression of the high-precision niche work for which our customers have relied upon Matrix for nearly five decades,” sales manager Tom Moyak said.
Related: Micromolders find their fit
The challenges resulting from the steadily decreasing sizes and wall thicknesses of customers’ products and product features led the company to specialize in micromolding, an area for which there was no blueprint at the time, he said.
Matrix takes a holistic approach to the micromolding process.
“We bring all facets together,” Moyak said. “Through advance product quality planning, we gather input from mold designers, tool makers, process and automation engineers, and quality personnel to ensure all processes work together efficiently. In addition, we challenge ourselves to continuously improve our micromolding process. For instance, we are steadily decreasing our mold sizes and increasing our throughput and shot-to-shot repeatability while maintaining high levels of quality. It’s very exciting to see the results.”
“There is an artistry in what is able to be created in steel and ultimately molded in plastic, but the key to all of this is know-how,” Moyak said. “We look at each project on a case-by-case basis and consider resin selection, feature size, manufacturability and more to determine if we’re confident in our approach to be able to offer our customer a viable manufacturing solution.”
Matrix has micromolded components, including battery safety devices, electrical and automotive connectors and medical devices, for various end-use industries. The company specializes in complex features and geometries in parts that use engineering-grade resins.
“As examples, we are often contracted to produce micro, ultra-fine pitch and micro-featured electrical components or a medical tool where our end customer needed an outside-of-the-box solution,” Moyak said.
The company uses customized Sodick injection molding machines.
“Some challenges with micromolding include part containment, handling and inspection, inserting of gates and other small features in tooling, handling of tooling for preventative maintenance, and, especially, dealing with [manufacturing] paradigms,” Moyak said.
Mold designs, material selection, mold alignment and metrology all are more challenging when dealing with micromolded products, he said.
“Think of it as a continuous chain where one broken link along the manufacturing cycle will result in it not being as useful,” Moyak said.
Quality control also is particularly challenging.
Matrix employs 15 engineers with most of them coming from the Penn State plastic engineering technology program. The company conducts in-house training and has several engineers with Master Molder I and Master Molder II certifications from RJG Inc.
“In addition, we have double-digit journeymen toolmakers with several being full-time tool designers,” Moyak said. “This unique mix of skills allows Matrix Tool to offer our customers cutting-edge engineering services.”
Contact:
Matrix Tool Inc., Fairview, Pa., 814-474-5531, www.matrixtoolinc.com
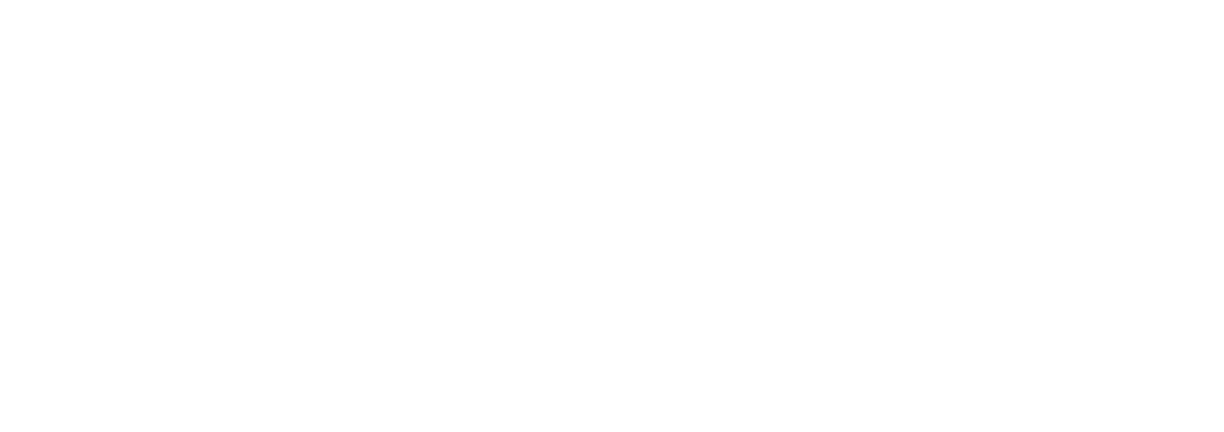