The economics of increasing injection molding capacity through aftermarket upgrades
By Edward Jump, M-Powered IIoT digital analytics leader, and Kevin Stanley, regional service manager, aftermarket field services
Milacron
With the ongoing pandemic, U.S.-based injection molders are experiencing continued growth as medical, construction and other markets are reshoring operations, or rival manufacturers have shut down operations.
For some, this is forcing manufacturers into a capacity bottleneck. Expanding the machinery floor to accommodate this can be costly; some companies are instead electing to expand their machinery utilization and production by upgrading their existing assets to boost the bottom line. All resolutions must fit within one overarching principle: Your overall operation must be effective and profitable.
Before you allocate any funds, ask yourself a serious question: Do you require an additional machine short-term or long-term? If it’s a short-term need, it’s time to consider reaching a greater overall equipment effectiveness (OEE) with your existing machinery.
Finding a machinery assessment provider
Machinery assessments will minimize your initial expenditure to discover any shortcomings or deficiencies in your machine fleet, while minimizing the effect of downtime for your equipment. These teams should focus on failure analysis, safety measures and increasing your production capacity. The challenge is identifying a provider that can accommodate your precise needs including:
Examining each functional area of your machine. Summarized findings should be organized into a comprehensive written report outlining present conditions, as well as recommended maintenance and productivity enhancements.
Comprehensive planning and strategies to triage any service or repairs to maximize productivity and reliability.
A complete safety assessment to ensure your machines are functioning safely and advise on any upgrades necessary to meet current ANSI safety standards.
A tailored preventive maintenance program to augment up-time based on your cycle and production requirements.
Upgrading and supporting existing machinery
Your profitability depends on more than a functioning molding machine. It also depends on having access to deliverable parts prior to unplanned downtime and expert service technicians to aid in improving the performance and longevity of your fleet. Some upgrades or retrofits may be the more conservative choice when compared to acquiring a new machine.
Customized screw designs or heater bands: Even after a machine has been running for a long time, many manufacturers neglect to consider newer or improved screw and barrel technology to advance efficiency, performance and material handling over the clamp end. The variety that exists by industry segment, resin material, part design and general application are lengthy. Considerations such as the size of the machine, potential for screw wear, heat, cycle time, melt temperature, color mix and recovery time can make for a complex equation.
Specialized feed screws maximize conductive melting to provide:
Higher production rates
Lower melt temperatures
Uniform melt temperatures
Improved mixing
Reduced shear energy input
Improved energy efficiency
Increased conductive melting
No hot spots and no splay due to excellent melt quality.
Control retrofits: Upgrading from an obsolete machine control to a current technology can keep an older machine in production for years to come. A modernized control provides many features, including digital feedback devices, VNC-integrated auxiliary control and OBE valving, along with closed-loop control. On some models, a considerable cycle-time reduction can be seen due to the additional features. Many customers also see the added benefit of a common control on all their machines for maintenance and operator teams, as well as the reduced spare-part inventory cost.
Mold gate: This technique of adding multiple sequential mold gate valves to machines helps to control the flow of material into multiple cavities. By controlling the sequence and cavity pressure, this can lower your tonnage requirements to allow parts to be molded on a smaller press. The clamp tonnage required to fill one cavity at a time is much less than when multiple cavities are filled simultaneously. It also provides more uniform part quality from all cavities or can sometimes result in a shorter shot.
Secondary injection units: Both vertical and horizontal injection units work along with rotary platen applications. A multi-component machine can manufacture products in a single production cell that would normally require additional injection molding machines or downstream processes.
Core-pull valving: Simply put, core pull allows a cavity or void in the part design to minimize some downstream processes for a part. Multiple core-pull circuits can also be added as needed. This method can be timed or controlled specific to the tooling.
Leveraging an IIoT solution to maximize efficiency
An understanding of capacity utilization within any manufacturing system is critical in setting operational strategy. Production lines and machines must have their performance accurately tracked and available for reporting if a business is to continually improve its OEE. Data from an IIoT platform can provide unique insights on your current changeover processes or recipes that can help to scale through highlighting process and operational inefficiencies in a short time.
In the digital world of IIoT, scheduled maintenance and reactive maintenance are no longer synonymous with the term preventive maintenance. Digital IIoT tools collect and leverage data to provide recommendations based on how each unique OEM is using and operating all of its assets. Not only will this reduce unplanned downtime, it provides timely and necessary guidance and recommendations to leverage maintenance actions during planned downtime. This improved efficiency comes into play as generated data drives maintenance schedules, so you don’t under- or over-maintain your assets.
Additional efficiency benefits are found when this data detects wear and tear of critical components. Milacron refers to these actionable insights as Plastinomics, which allows us to understand the economics of molding and providing cost-effective intelligent solutions that augment a machine fleet and capacity. Data-generated health scores help molders to justify when components like feed screws, hydraulic pumps or heater bands are negatively impacting the cycle and/or efficiency of the machine before these components fail.
Simple and customizable actions can be provided in real-time from edge-computing devices or cloud-based monitoring, which can prompt your maintenance team to order a component to make lead times a thing of the past. As the component begins to impact your cycle, part quality or energy consumption, your team knows when it’s time to take action.
Through all of these solutions, your team can realize breakthrough results and create a competitive advantage while solving difficult molding problems in order to maximize efficiency and machine utilization.
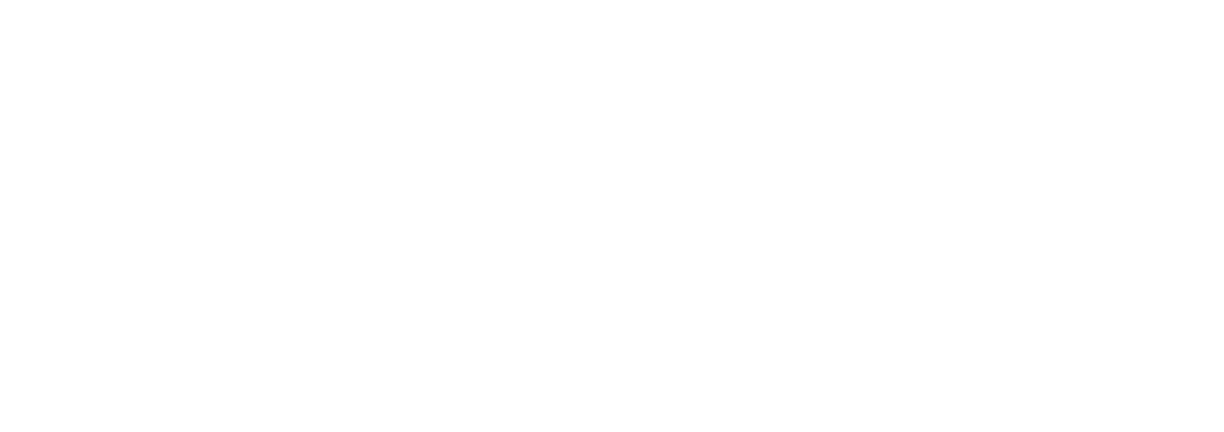